Achieving precision in winder tension control is indispensable for the efficiency and quality of winding processes across various industries, including textiles, paper production, and flexible packaging. These industries often grapple with maintaining consistent tension, which, if not properly managed, can lead to defects, material waste, and decreased operational efficiency.
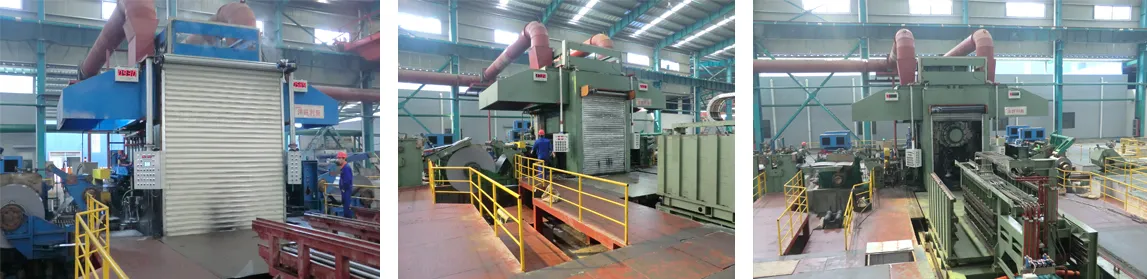
The winder tension control system is the linchpin ensuring the smooth unwinding, processing, and rewinding of materials. When exploring innovations in tension control, it is crucial to focus on the following aspects Experience, Expertise, Authoritativeness, and Trustworthiness.
Experience in winder tension control often involves leveraging accumulated insights from years of practical application. Operators and engineers collectively hold a wealth of knowledge on how variables such as material properties, environmental factors, and machine conditions affect winding operations. For instance, a high-humidity environment can lead to material stretch, requiring real-time adjustments to tension parameters. Employing advanced control systems equipped with sensors that can adapt to such variables promises a significant reduction in downtime and material defects. These systems, backed by decades of collective industry experience, result in markedly improved productivity.
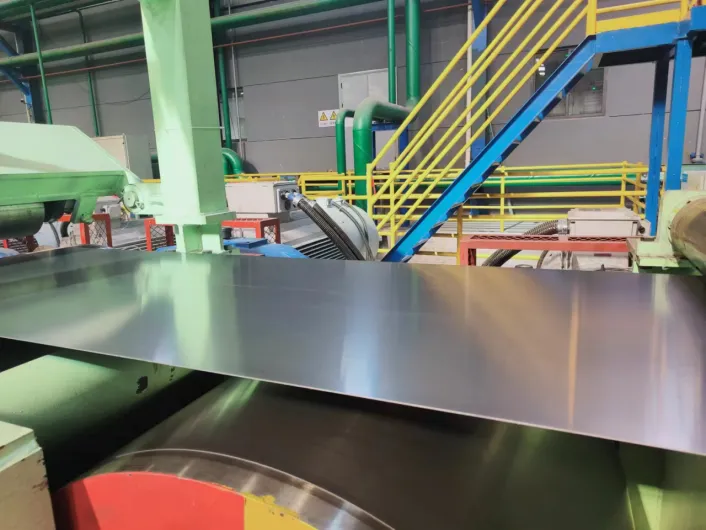
Expertise is reflected in the sophisticated design and implementation of tension control systems. An expert understands that effective tension control balances elasticity, tension, and velocity through precision algorithms and mechanisms. Sophisticated PID controllers, machine learning algorithms, and adaptive control systems represent the zenith of technological advancement in ensuring precise operation. Innovative technologies like closed-loop control systems, which automatically adjust tension based on feedback from torque sensors, allow for compelling real-time corrections, fostering high-quality output with minimal manual intervention.
Authoritativeness in tension control solutions is derived from leading industry players who set the benchmarks for excellence. Companies and professionals who influence industry standards are instrumental in driving innovations, thus enhancing operational reliability and efficiency. Collaborations, such as joint research efforts and shared technological breakthroughs within industry consortiums, lend further credibility. Authority is also established through visible success stories and case studies, where particular companies have markedly improved their efficiency and output quality by adopting cutting-edge winder tension control systems.
winder tension control
Trustworthiness is paramount and is denoted by a commitment to safety, reliability, and long-term performance. Manufacturers of tension control systems assure their clients through rigorous testing, transparent reporting, and adherence to stringent industry regulations and standards. For example, validation processes include stress-testing equipment under various operational scenarios to ensure robustness. Positive endorsements and testimonials from existing users serve as powerful indicators of a system’s reliability, reinforcing the buyer's decision.
Moreover, future trends in winder tension control point towards increasing integration with IoT and Industry 4.0. Modern systems now incorporate features that allow real-time data collection and remote monitoring. This connectivity facilitates predictive maintenance, where data analytics identify potential points of failure before they occur, drastically reducing unforeseen downtime. For businesses, this means operations are not only smooth but also cost-effective.
Furthermore, the lean manufacturing principles are increasingly shaping the way tension control systems are designed and operated. By minimizing waste and optimizing every component of the material handling process, manufacturers can enjoy better margins and reduced environmental impact. In relation to lean principles, tension control plays a critical role in ensuring that no excess material is used, tangibly contributing to waste reduction efforts.
Finally, competent tension control underpinned by robust technology directly contributes to sustainable operations. Industries are under more pressure than ever to adhere to environmental mandates, requiring both reduced energy consumption and minimal wastage. As winder tension control systems become more precise and energy-efficient, they substantially lessen the carbon footprint of manufacturing processes.
In essence, winder tension control is not just a technical process—it's a cornerstone of advanced manufacturing strategies centered on quality, efficiency, and sustainability. Industry leaders must continue developing solutions that are not only efficient but also adaptable to emerging challenges and opportunities. By focusing on experience, expertise, authoritative knowledge, and trustworthiness, these systems offer transformative impacts on productivity and product quality, meeting the ever-evolving demands of modern manufacturing.