Nestled in the heart of industrial innovation, rolling mills in steelworks represent a cornerstone of modern metallurgy. These engineering marvels are not just pivotal to steel production but are exemplary of advanced manufacturing processes. At the epicenter of this transformative industry is the concept of rolling mills—crucial for converting raw steel into sheets, bars, and other forms demanded by countless sectors globally.
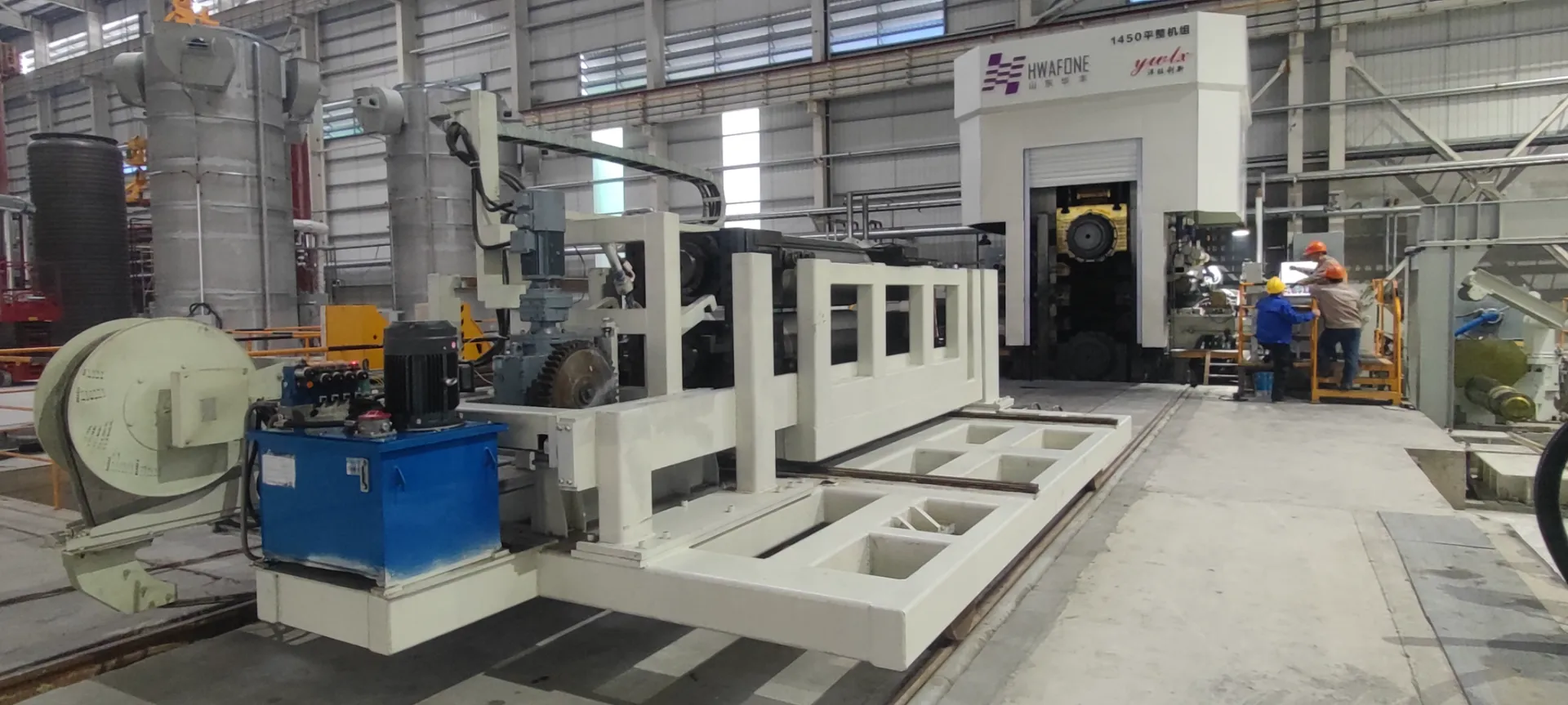
Steelmaking is an art and science amalgamation that begins with melting raw materials in a blast furnace. This molten steel then transforms into slabs, blooms, or billets, prepared meticulously for the rolling process.
Rolling mills in steelworks play a crucial role here. This process involves passing the steel through a series of rollers, each designed to reduce thickness, alter the cross-section, achieve specific mechanical properties, and refine its external finish. The precision of this machinery not only influences the steel’s physical properties but ensures optimal product quality, meeting stringent industrial standards.
In integrating advanced technology, these rolling mills have undergone significant evolution. Modern mills utilize sophisticated sensors and automation technologies to monitor and control parameters such as speed, temperature, and pressure. Such automation ensures consistent product quality and enhances operational efficiency by reducing human error, energy consumption, and material wastage—contributing to sustainable industrial practices that align with global environmental directives.
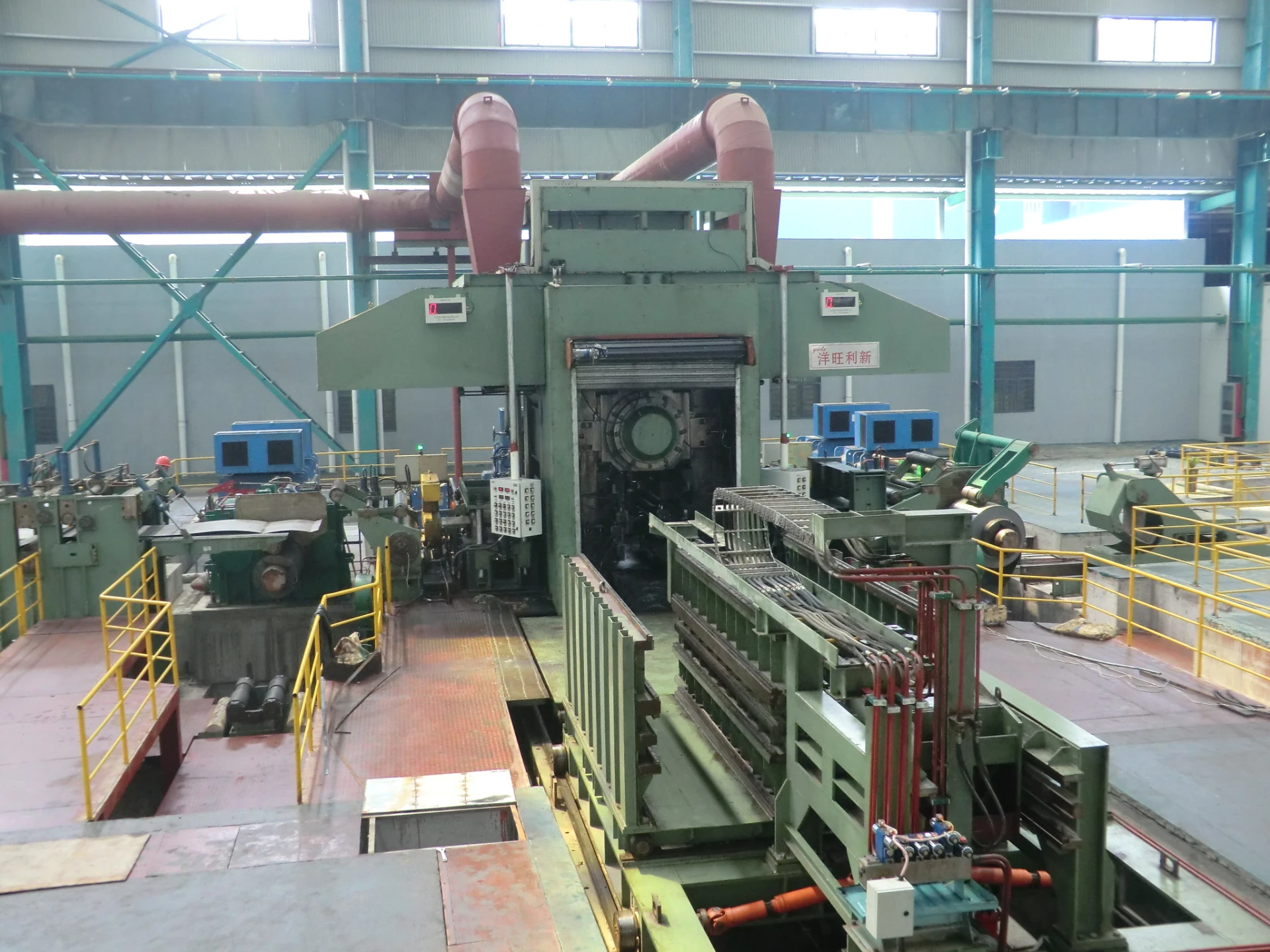
Experience in operating rolling mills is crucial for maintaining precision and quality. Skilled operators, with years of experience, bring an intrinsic understanding of the machinery and its complex intricacies. Their expertise lies in fine-tuning settings, preempting potential issues, and ensuring a seamless production line that maximizes yield without compromising quality. Real-world scenarios often depict how seasoned professionals can avert production stoppages, highlighting their critical role in problem-solving and decision-making under pressure.
walzwerk im stahlwerk
Expertise in rolling mill operations extends into R&D, where continuous improvements are a staple. Metallurgists and engineers work relentlessly to augment rolling capabilities, researching new materials and innovative techniques to expand product range and improve material characteristics. Their authority is evidenced by publications and patents that often propel the industry forward, providing sustainable, efficient solutions to meet modern technological demands.
Trustworthiness within this sphere is cemented through adherence to safety and quality standards. Trusted rolling mills operate under internationally recognized certifications such as ISO standards, which assure customers of consistent, high-quality steel products. Transparency in supply chains adds another layer of trust, with reputable firms often providing comprehensive documentation and traceability of materials, reinforcing credibility and confidence in their products.
In summary, rolling mills in steelworks encapsulate a blend of innovation, expert knowledge, and unwavering commitment to quality. They serve as the bridge between raw steel potential and its versatile applications, impacting sectors from construction to automotive engineering. Through continuous technological advancements and adherence to global standards, these rolling mills not only bolster the industry’s growth but also champion a model of sustainable and efficient production. Their reputation rests on the foundation of expertise and trustworthiness, nurturing robust partnerships across continents, and reflecting a relentless pursuit of excellence.