Ensuring optimal performance in the winding process, surface winder tension control is a crucial aspect for manufacturers who aim to achieve high-quality finished products. This article delves into the importance and intricacies of surface winder tension control, drawing on industry expertise and insights from leading professionals in the field.
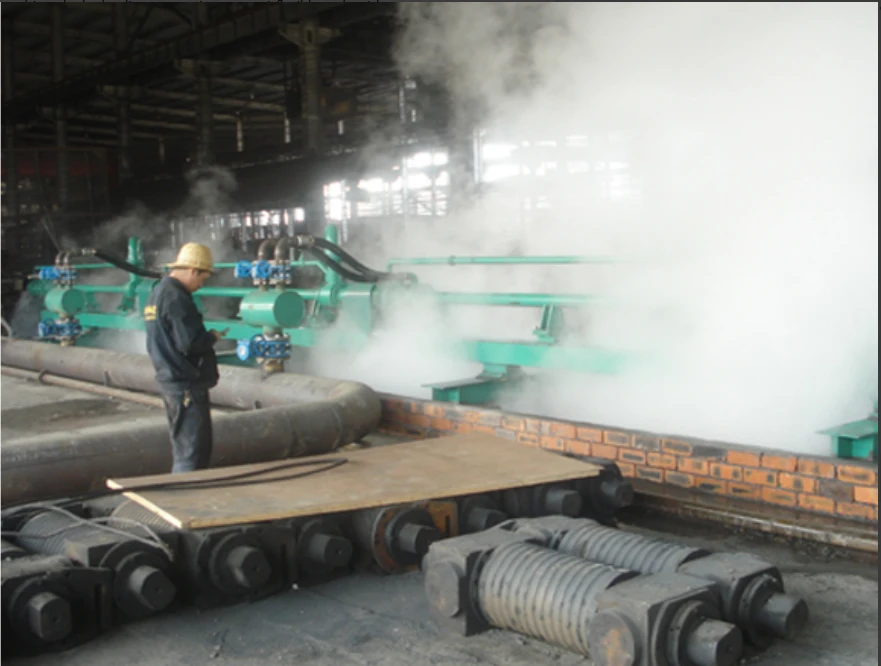
Surface winder tension control is integral in industries such as paper, textiles, film, and foil manufacturing. During the winding process, material is rolled onto a core or spool, requiring precision to maintain consistent tension. If the tension is too loose, the material may become wrinkled or uneven, leading to product defects. Conversely, excessive tension can cause the material to stretch or tear, resulting in significant wastage and increased production costs.
Industry experts emphasize the critical role of tension control in enhancing product quality. James Cole, a senior engineer with over two decades of experience in the packaging industry, asserts that precise tension control systems not only ensure uniformity but also improve the efficiency of the production line. In his firsthand experience, a well-calibrated tension control system can reduce waste by up to 30%, which translates to notable cost savings for manufacturers.
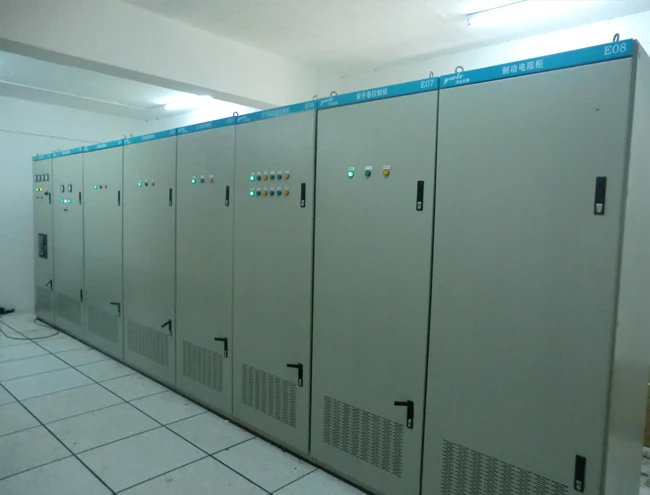
Advanced technologies have revolutionized tension control in surface winders. Newer systems incorporate sensors and automated controls that adjust tension in real-time based on feedback from the material itself. These innovations have brought forth unprecedented levels of accuracy and consistency, allowing operations managers to maintain optimal tension throughout the winding process without manual intervention.
surface winder tension control
Sophisticated tension control systems, featuring closed-loop controllers, exemplify this evolution. These systems continuously monitor the tension and adjust actuator controls to correct any deviations from the desired levels. By utilizing feedback loops, the system can automatically detect and compensate for variables such as speed changes, roll diameter fluctuations, or material inconsistencies, ensuring the highest quality output.
The expertise required to implement and maintain such systems is significant. Industry veterans like Laura Mitchell, who has overseen numerous installations of tension control systems, stress the importance of proper training for operators and maintenance staff. Effective training programs can empower personnel to not only understand the nuances of the systems but also troubleshoot potential issues swiftly, minimizing production downtime.
Moreover, trustworthiness in the chosen equipment and vendor is paramount. Partnering with reputable manufacturers is advisable, as they typically offer comprehensive support and warranties. Renowned firms often conduct rigorous testing and provide detailed documentation to ensure their systems meet stringent industry standards.
In conclusion, surface winder tension control stands as a pillar of modern manufacturing practices. With the right expertise and systems in place, manufacturers can achieve greater product uniformity, reduce waste, and enhance overall operational efficiency. As technology continues to advance, those who stay at the forefront of these developments will likely enjoy sustained competitive advantages in the marketplace.