In the realm of metallurgy, the skin pass process stands as a pivotal technique, particularly for steel manufacturing. Rooted in technical expertise and refined through years of industrial evolution, this process is essential for enhancing both the functional and aesthetic qualities of steel products.

The skin pass process is essentially a cold rolling step, indispensable in achieving the desired surface quality and mechanical properties of steel. Typically, this process occurs after the initial hot rolling phase and involves passing the steel through a set of rollers at room temperature. This step is nuanced; while it achieves surface refinement and improves certain mechanical aspects, it also serves to correct aspects like shape issues, tensile strength, and surface texture.
One might ask, what specific transformations occur during the skin pass process? Primarily, it reduces the thickness of the steel slightly (usually by 0.5% to 1.5%) and rectifies any unevenness in thickness, creating a more uniform surface finish. By increasing surface contact with the rolls, this process effectively minimizes surface roughness. Such refinements are pivotal for applications requiring visual uniformity, such as automotive exteriors and home appliances.
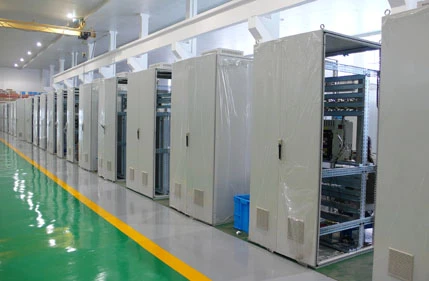
But the skin pass process goes beyond mere aesthetics. On a mechanical level, it enhances the yield and tensile strength of the steel without substantially altering its overall mechanical properties. This delicate balance is achieved by introducing work hardening—a process that results from the rearrangement of microscopic dislocations within the steel's crystalline structure. Work hardening increases the material's strength and hardness, thus ensuring durability without compromising its ductility.
It’s imperative to consider the authoritative backing in conducting and refining this process. Institutes dedicated to metallurgical research have extensively studied and validated the methods involved, such as the American Iron and Steel Institute and the World Steel Association. These institutions emphasize the importance of process control and expertise to optimize the balance of strength, surface quality, and cost-effectiveness.
skin pass process steel
Furthermore, expertise in the skin pass process involves a deep understanding of the equipment used. Modern skin pass mills are engineered to allow precise control over force, speed, and reduction ratios. The integration of advanced technologies such as computerized controls and real-time monitoring systems plays a crucial role in maintaining consistency and quality. For instance, real-time monitoring can help detect deviations from desired parameters, allowing immediate adjustments to ensure the final product meets specified standards.
Trust in this process is further solidified through the testimonials and experience of leading steel manufacturers. Companies with decades of experience in steel production attest to the consistency and high quality yielded by the skin pass process. For example, organizations such as ArcelorMittal and Nippon Steel Corporation have set industry standards by employing advanced technologies and rigorous quality assurance protocols.
It’s also notable how the process impacts downstream processes and product excellence. A well-executed skin pass not only ensures the quality of the final product but also enhances subsequent processes such as coating and painting. The smooth finish achieved through this process provides an excellent substrate for coatings, thereby extending the lifespan and aesthetic appeal of the steel product.
In summary, the skin pass process in steel manufacturing exemplifies a sophisticated blend of metallurgical science, engineering precision, and industrial innovation. Its significance in achieving high-caliber steel products is undeniable. As the demand for quality steel products grows, the need for expertise in this area becomes increasingly critical. Through a combination of authoritative research, practical expertise, and ongoing innovation, the skin pass process continues to be a cornerstone of modern steel manufacturing, setting benchmarks for quality and reliability in the industry.