Rolling mills are quintessential in the metalworking sector, holding a pivotal role in transforming raw materials into precisely shaped products. The cost associated with rolling mills is a multifaceted subject that touches on various factors intrinsic to the manufacturing and operational processes. Introducing a well-rounded understanding of these costs requires a blend of real-world insights and industry-specific expertise.
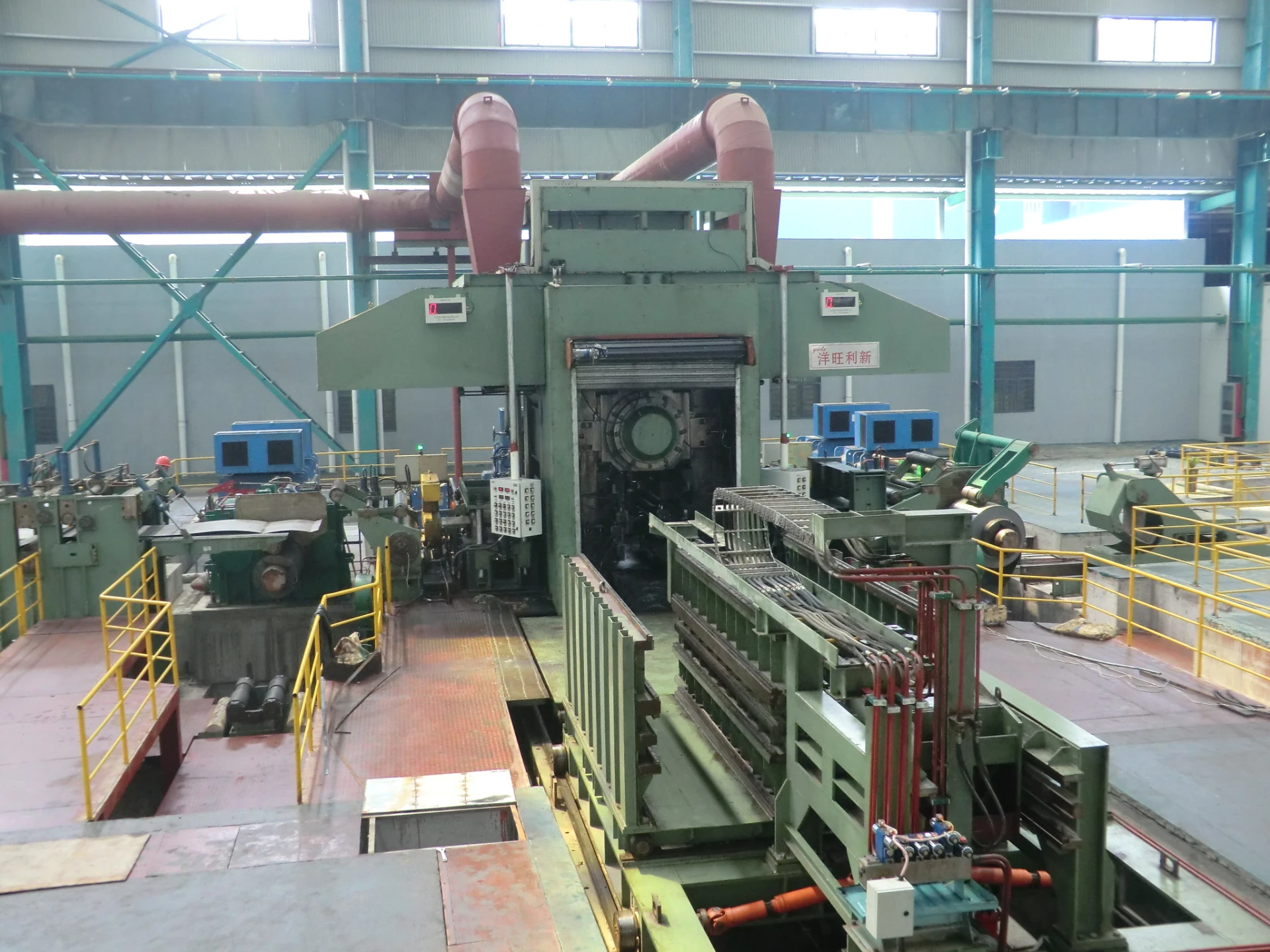
Initially,
the cost of a rolling mill is influenced by the type of mill being procured. There are several varieties, including hot rolling mills, cold rolling mills, tandem rolling mills, and more specialized configurations. Each type possesses unique capabilities and limitations, meaning their operational efficiencies and subsequent costs vary. For instance, hot rolling mills, which function at high temperatures, typically incur costs associated with the maintenance of heating elements and insulation materials, contrasting with cold rolling mill operations, which primarily involve expenses linked to cooling systems and surface finish refurbishments.
Operational expenditure plays a critical role, encompassing aspects like energy usage, labor, and maintenance. Rolling mills are energy-intensive machinery; thus, the cost of electricity or alternative power sources can substantially impact overall expenditure. The cost might also vary depending on the geographical location due to differences in energy pricing. Meanwhile, skilled labor, essential for operating complex machinery efficiently, and periodic maintenance to prevent unexpected downtimes further contribute to costs. Expertise in balancing these operational elements ensures not only optimal performance but also cost-effectiveness.
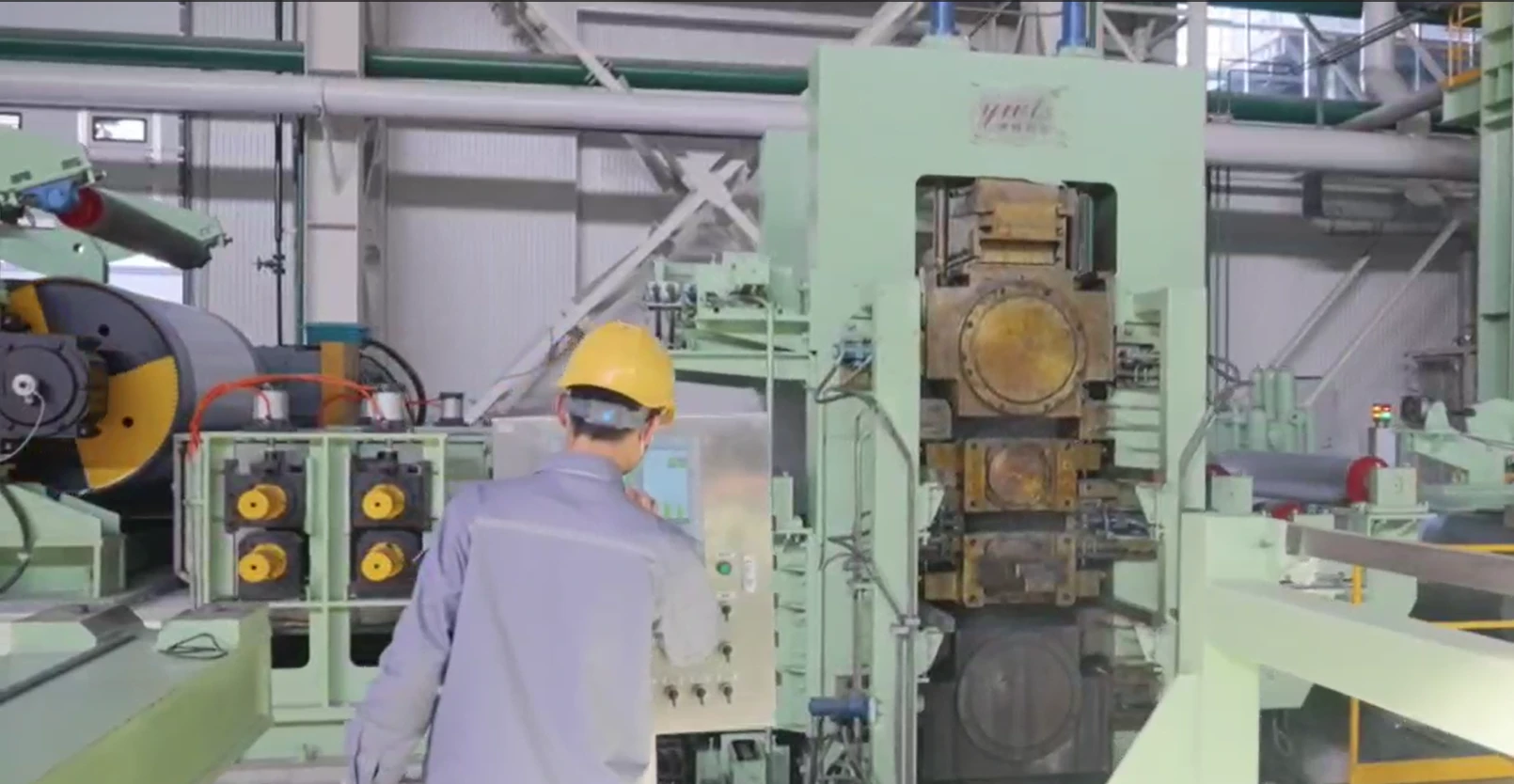
Another significant expense variable is the acquisition and integration of advanced technology. Modern rolling mills employ sophisticated automation and control systems to enhance precision, efficiency, and safety. The initial cost of installing such technology may be high, yet it often leads to reduced long-term costs by minimizing human error, reducing waste, and optimizing resource usage. Investing in cutting-edge technology can provide a competitive edge, making a rolling mill operation more attractive to discerning clients seeking consistent quality.
rolling mill cost
Material costs, subject to fluctuations in global markets, are another expense consideration. The procurement of metals, whether steel, aluminum, or copper, can vary dramatically, influencing the cost dynamics of operating a rolling mill. Companies often need to employ purchasing strategies that mitigate the impact of price volatility, such as establishing long-term contracts with suppliers or utilizing hedging strategies.
In addition to these factors, regulatory compliance is pivotal in determining cost structures. Adhering to safety and environmental regulations is non-negotiable, which necessitates investment in safety protocols, environmental impact assessments, and emissions control technologies. While these measures can represent a sizable initial investment, they are imperative for sustainable operations and long-term legal compliance, often reducing the risk of costly sanctions or operational halts.
Trustworthiness and authority in the rolling mill sector stem from transparent operations and consistent quality production, which also influence cost. Building a reputation that clients can rely on often requires investments in quality control systems and certifications that assert product standards and ethical operations.
In conclusion, while rolling mill costs are integral to the financial planning of any relevant business, understanding them through the lenses of experience and expertise is indispensable. From choosing the right type of mill to implementing advanced technology, managing operational efficiency, navigating material market trends, and ensuring regulatory compliance, each aspect contributes to a comprehensive cost structure. Businesses that adeptly manage these components, while maintaining a focus on quality and sustainability, can not only better navigate the complexities of rolling mill costs but also establish enduring, profitable operations.