For decades, the art and science of metal fabrication have relied on various instruments and processes to achieve precision and quality in metalwork. Among these, the laminatoio per piastre, or plate rolling mill, stands as a critical component in the intricate dance of transforming raw metal into usable forms for multiple industries. Understanding its complexities and advantages is essential for anyone involved in metal fabrication.
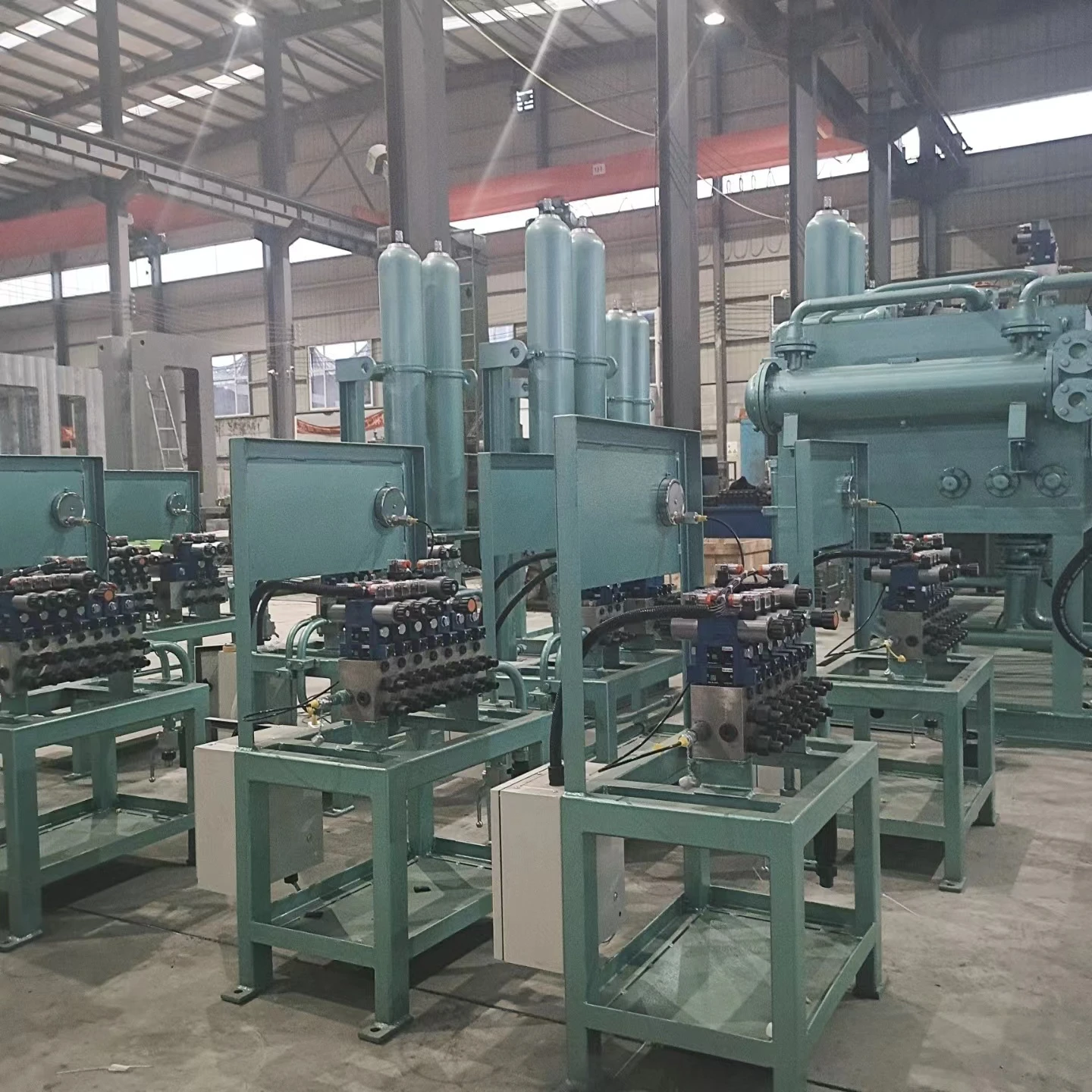
The primary function of a laminatoio per piastre is to reduce the thickness of metal plates while increasing their length. This process is essential for industries ranging from automotive to aerospace and construction, where specific size specifications are critical. Through a sequence of rollers, heat treatments, and cooling schedules, a plate rolling mill shapes the metal while enhancing its structural properties.
When selecting a laminatoio per piastre for any operation, it is crucial to understand the different types available. These include two-high, three-high, four-high, cluster, and tandem rolling mills. Each type serves a particular purpose and offers various advantages
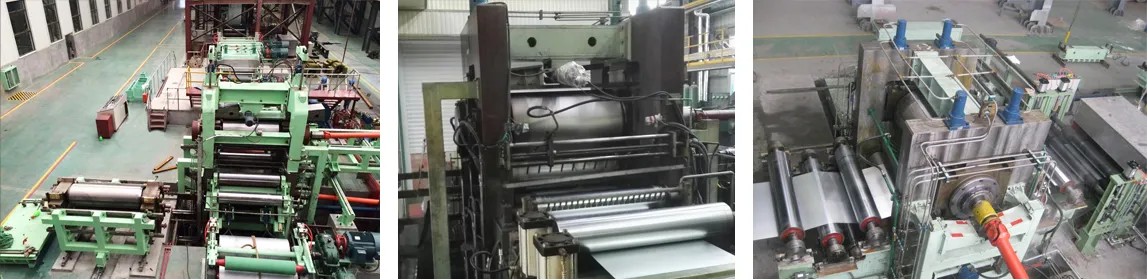
1. Two-High Rolling Mills Known for their simplicity and cost-effectiveness, these mills are best suited for small-scale operations or where initial thickness reduction is desired. They comprise two opposing cylindrical rollers that compress the metal.
2. Three-High Rolling Mills Featuring an additional roller, these mills allow for continuous rolling through multiple passes without needing to adjust the work piece’s position manually.
3. Four-High Rolling Mills Equipped with a backup roller for each working roller, these mills provide greater strength and precision. They are indispensable in environments requiring thin plates and high finish quality.
4. Cluster Rolling Mills Designed for high production and precision, these use multiple smaller diameter rollers to achieve a higher degree of control over the metal thickness and finish.
laminatoio per piastre
5. Tandem Rolling Mills Comprising a series of rolling mill stands arranged in tandem, these are ideal for large-scale operations needing constant, high throughput.
The choice of laminatoio per piastre impacts not only the production rate but also the product quality. Selecting the right material for roll construction, such as high-grade steel alloys, ensures the durability and precision of the rolled plates. Furthermore, incorporating advanced control systems enhances the accuracy of plate dimensions and surface quality, making modern plate mills indispensable in industries demanding high-caliber outputs.
Experience in operating and maintaining a laminatoio per piastre contributes significantly to optimizing output quality and operational efficiency. Regular maintenance checks, calibration of rollers, and meticulous monitoring of temperature settings are part of daily routines that experienced operators follow to ensure smooth operations and consistent product quality.
Moreover,
as automation and Industry 4.0 technologies become more prevalent, integrating smart sensors and IoT (Internet of Things) technologies into plate rolling mills can provide real-time data on performance metrics, wear and tear of equipment, and even predict potential malfunctions. This leads to proactive maintenance strategies, minimizing downtime and maximizing productivity.
Environmental considerations are also influencing the development and use of a laminatoio per piastre. Implementing energy-efficient technologies and optimizing rolling processes to reduce waste and emissions are becoming standard practices. These practices not only benefit the environment but also contribute to a company's sustainability goals and cost savings over time.
Trust remains a cornerstone when investing in such sophisticated machinery. Partnering with reputable manufacturers who provide extensive warranties, after-sales support, and regular updates can ensure a lasting investment. Engaging with industry certifications and peer-reviewed studies can further bolster the credibility of both the equipment and the operations using it.
Ultimately, the laminatoio per piastre is more than just a tool; it is a linchpin in the metal fabrication industry that, when properly selected and maintained, delivers excellence across various applications. For those seeking precision, efficiency, and quality, leveraging the expertise of seasoned operators and the reliability of leading manufacturers forms the backbone of success in metal processing endeavors.