In the industrial landscape, the rolling mill plant, known as impianto laminazione in Italian, is a cornerstone for manufacturing and metallurgy. This intricate system, pivotal for shaping metals, offers unparalleled efficiency, precision, and robustness in producing metal sheets and other profiles. Understanding the intricacies of a rolling mill plant not only requires expertise in metallurgy but also demands insights into operational efficiency and technical innovation.
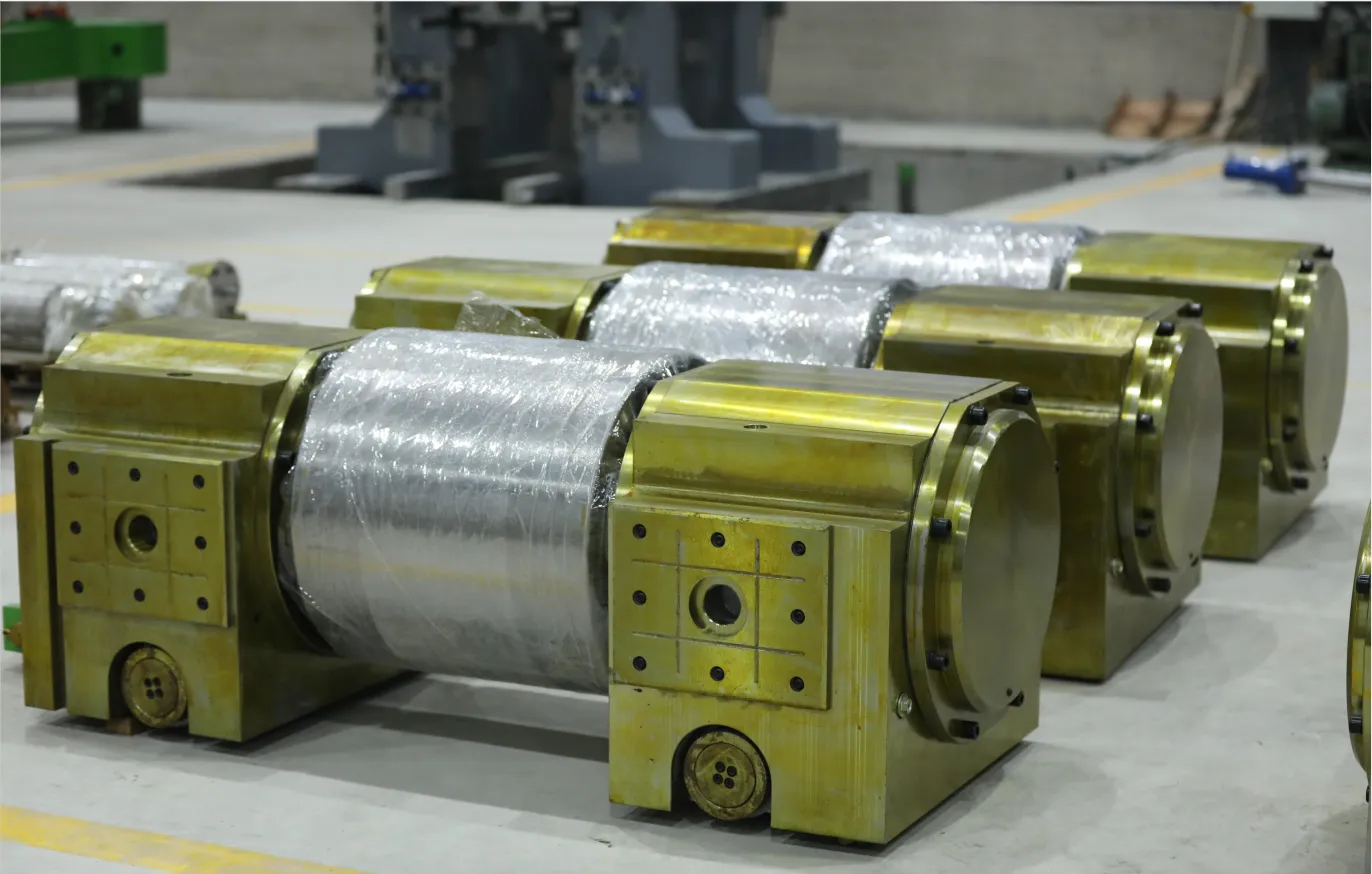
The experience of operating a rolling mill plant is akin to orchestrating a symphony where precision is paramount. Each component must perform seamlessly to ensure that the metal's structural integrity is enhanced rather than compromised. The rollers, crucial for this process, exert a controlled force that gradually reduces the thickness of the metal, transforming it into the desired shape and size. Operators skilled in the nuances of metallurgical science and machinery coordination bring about this transformation with dexterity.
From an expertise standpoint, the selection of materials and components for a rolling mill plant is critical. High-grade alloys for rollers, advanced control systems for temperature and pressure, and cutting-edge software for process monitoring collectively ensure the plant's capability to produce high-quality outputs. The continuous casting process, where molten metal is solidified into a semi-finished billet, forms the bedrock of efficiency and precision. Expertise in maintaining optimal casting conditions and mitigating thermal stress in metals is essential for preserving material properties and enhancing product quality.
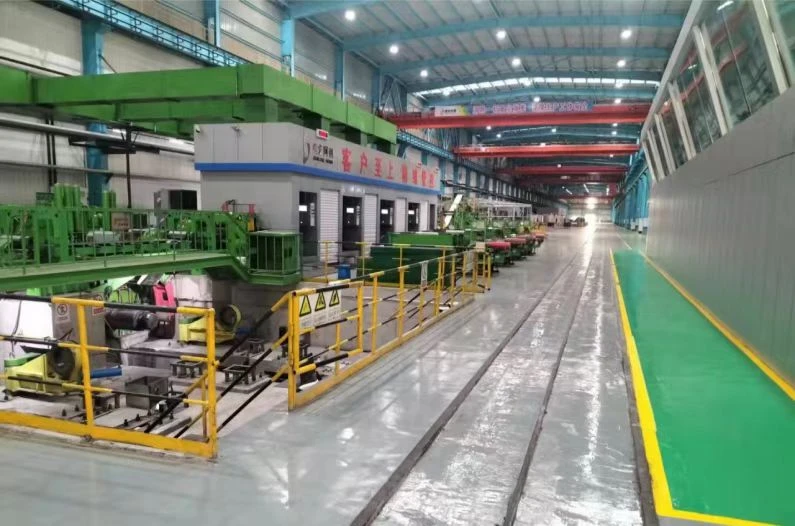
Authority in the domain of rolling mill plants often stems from a track record of implementing and refining cutting-edge technologies in metal processing. The history of technological advancements in this sector underscores the significance of continuously evolving methodologies. Adopting state-of-the-art automated systems and integrating AI-driven analytics have revolutionized operational workflows, reduced energy consumption, and minimized error margins. Those who lead in deploying these innovations offer unparalleled value and reliability in metal shaping industries.
impianto laminazione
Trustworthiness in the context of an impianto laminazione is deeply rooted in the reliability and durability of the products produced. Stakeholders from various industrial sectors, including automotive, construction, and appliance manufacturing, rely heavily on the structural integrity and precision-finished surfaces of rolled metal products. Adhering to stringent quality standards and possessing certifications from recognized industry bodies fortifies the trust placed in a rolling mill's output. Furthermore, sustainable practices in manufacturing and waste management augment the plant's reputation as an ecologically responsible operation.
Navigating the challenges of modern-day metal processing within a rolling mill plant involves a keen understanding of the dynamic requirements of global economies and ecological considerations. The shift towards sustainable practices is reimagining the traditional impianto laminazione into green, energy-efficient powerhouses. Formulating strategies to minimize carbon footprint and integrating renewable energy resources resonate with the industry's broader commitment to environmental stewardship.
In summary, a rolling mill plant encapsulates a domain where experience, expertise, authority, and trustworthiness converge to define excellence in metal processing. The sophistication with which these plants operate underpins the advanced manufacturing capabilities that serve as the backbone of myriad industries. Through continued innovation and adherence to stringent standards, the rolling mill plant solidifies its position as a vital asset in the manufacturing and metallurgical landscape.