In industrial machinery, the backup roller serves as an indispensable component in numerous applications, prominently in rolling mills. This auxiliary roller supports the primary roller, enhancing the precision and efficiency of the rolling process. Its role is both adaptive and vital, contributing to the machinery's overall capability, longevity, and reliability.
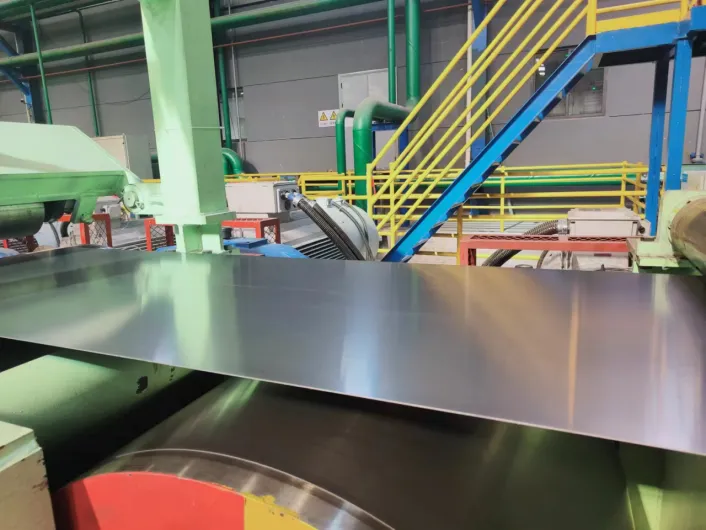
The primary function of a backup roller is to distribute the load and reduce the force exerted on the primary rollers, thereby mitigating wear and tear on the equipment. This load distribution is crucial in operations such as metal forming, where maintaining consistent pressure is central to achieving desired specifications in materials. Industries relying heavily on high-precision engineering find backup rollers integral to maintaining product quality.
Experience confirms that choosing the correct backup roller is fundamental to optimizing machine performance. Over the years, manufacturers have focused on designing backup rollers that can withstand extreme conditions, including high temperatures and significant mechanical stress. These rollers are typically crafted from high-grade steel or special alloys to ensure durability and resilience, catering to diverse industrial demands.
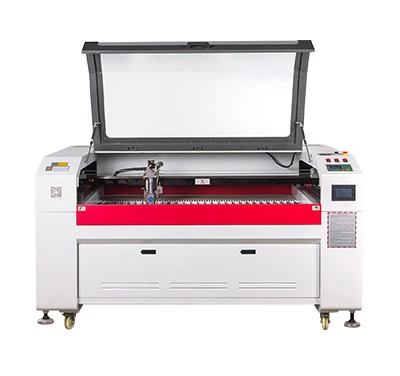
From an expertise perspective, understanding the mechanics of backup rollers and their interaction with other components is essential. The design of a backup roller involves complex engineering to ensure seamless integration with the machinery. Engineers consider factors such as roller diameter, surface finish, and alignment carefully, aligning these elements with the specific needs of the machinery. The precision with which these rollers are manufactured directly impacts their effectiveness and the operational success of the entire equipment assembly.
backup roller
The authority of backup roller manufacturers in the industry stems from their consistent delivery of high-quality products and commitment to innovation. Leading manufacturers invest significantly in research and development,
aiming to enhance roller materials and designs. This ongoing innovation ensures that backup rollers can accommodate the evolving demands of modern industrial practices, such as higher processing speeds and increased loads.
Trustworthiness in the backup roller market is built through rigorous testing and quality control processes. Manufacturers implement stringent testing protocols, including performance under simulated operational environments, to verify the rollers' reliability and durability. Customers can rely on certified backup rollers, assured by these comprehensive evaluations, attesting to their long-term performance.
Selecting backup rollers from reputable suppliers offers an additional layer of confidence. Esteemed suppliers provide comprehensive support, from technical consulting during purchase to after-sales service, ensuring that customers receive optimal value from their products. This level of service underscores the importance of collaboration between manufacturers, suppliers, and end-users in achieving operational excellence.
In summary, backup rollers are not just supplementary components; they are pivotal to the efficient operation of heavy industrial machinery. Their ability to distribute loads, withstand harsh conditions, and maintain performance over extended periods demonstrates their significance in industrial applications. Understanding this component's critical role and relying on expert advice when selecting and maintaining backup rollers can significantly advance manufacturing efficiency, product quality, and equipment lifespan, proving their necessity in the contemporary industrial landscape.