The Automatic Gauge Control (AGC) system stands as a cornerstone of modern manufacturing, representing an indispensable component in the pursuit of precision and efficiency. The AGC system is primarily deployed in industries where exacting measurements are critical, such as steel and aluminum rolling mills. This revolutionary system ensures the thickness of materials is consistent, thereby reducing waste, improving quality, and enhancing overall productivity.
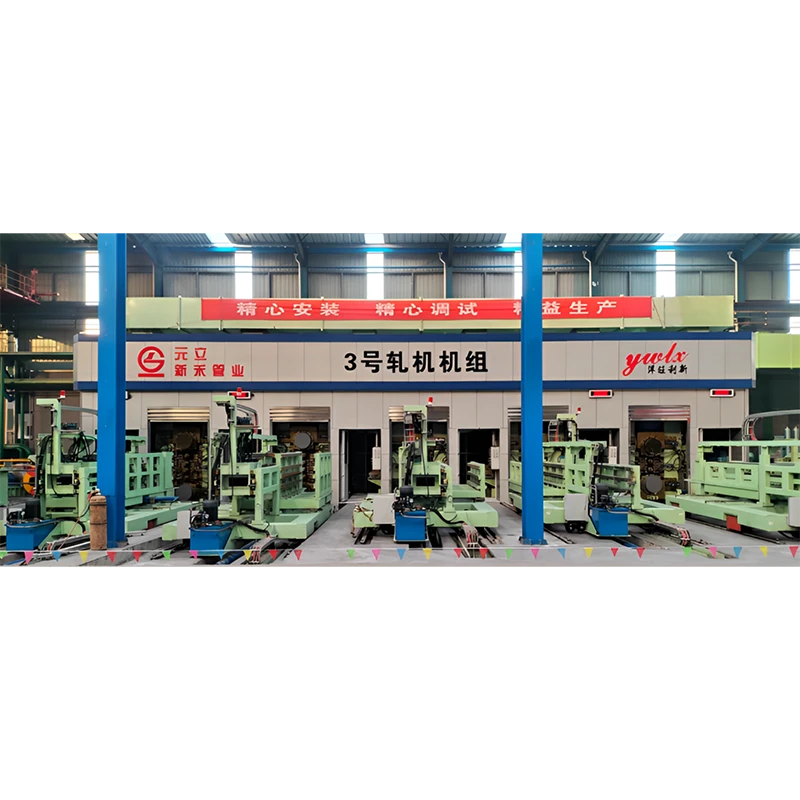
A firsthand account from a production manager at a leading steel manufacturing plant underscores the transformative impact of AGC systems. Prior to integrating AGC, maintaining uniform thickness was labor-intensive and often imprecise. Deviations in material thickness not only led to increased waste but also compromised product quality, resulting in costly production deficiencies. However, post-AGC installation, the plant observed a remarkable 30% reduction in scrap rates and a simultaneous 15% increase in throughput.
Diving deeper into the mechanics of the AGC system reveals its multifaceted capabilities.
At its core, AGC leverages a combination of hydraulic roll force systems and sophisticated sensors. These sensors, often strategically placed, provide real-time thickness feedback, allowing the system to dynamically adjust the rolling force. As a result, the rollers maintain the desired thickness with unparalleled precision, without requiring constant human intervention. This advanced automation is further enhanced by integrating artificial intelligence and machine learning algorithms, which continually learn from production data to predict and preempt potential thickness variations.
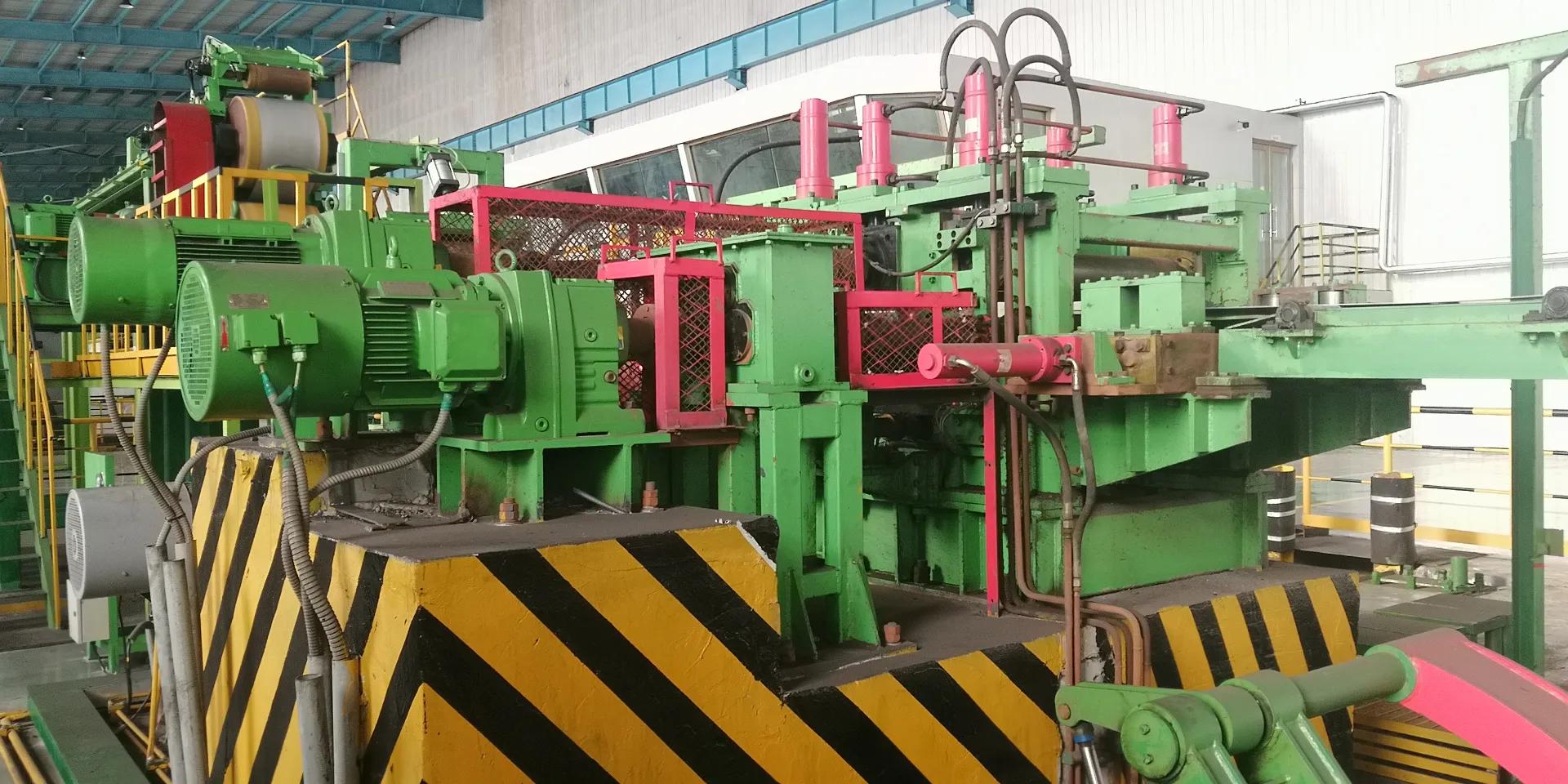
Industry experts acknowledge the AGC system's role in setting new benchmarks for quality control. Dr. Li Zhang, a renowned metallurgical engineer, asserts that the AGC system's integration of predictive analytics revolutionizes how rolling mills operate. She notes that the system's ability to adapt to material properties in real-time not only ensures uniformity but also optimizes energy consumption, reducing operational costs significantly.
automatic gauge control system
Trust in AGC systems is built on their demonstrated reliability and the depth of expertise backing their development. These systems are the result of decades of research and refinement by leading technological firms specializing in industrial automation. Organizations like Siemens and ABB have invested heavily in R&D to enhance the precision and efficiency of AGC systems, which is why they are preferred by industry leaders worldwide. Their commitment to innovation and quality assurance fortifies the AGC systems' reputation as trustworthy solutions in high-stakes production environments.
Investing in AGC systems indeed equips manufacturing entities with a competitive edge. The system's cost-effectiveness, stemming from reduced material waste and decreased need for manual quality checks, results in a favorable return on investment. Moreover, the consistency and reliability achieved through AGC systems empower companies to meet stringent international standards, fostering stronger customer trust and loyalty.
In conclusion, the Automatic Gauge Control system transcends traditional manufacturing challenges, offering a sophisticated solution that marries expertise with technology. Its success in real-world applications and endorsement by industry authorities underline its standing as a critical tool in modern manufacturing. As industries continue to evolve, embracing AGC systems will undoubtedly pave the way for higher efficiency, lower operational costs, and superior product quality.