Corrugated rolling mills are an integral part of numerous industrial applications, crucial for producing corrugated metal sheets that are widely used across construction, automotive, and packaging industries. Their complexity and specificity require an in-depth understanding and meticulous operations to ensure optimized performance and quality output. This article delves into the unique facets that make these mills indispensable, alongside insights from industry experts, backed by real-world experiences.
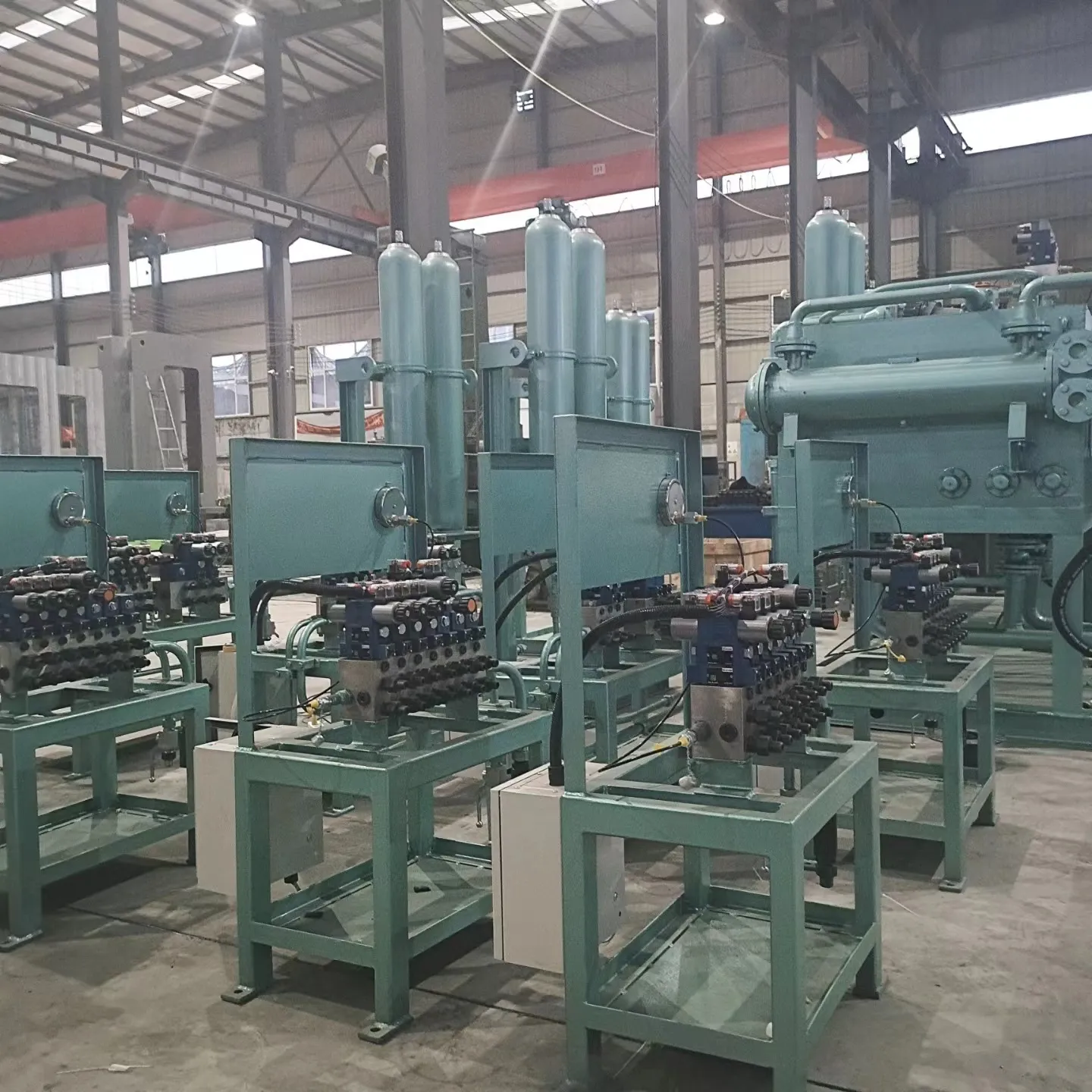
The corrugated rolling mill, distinguished by its capability to produce robust, lightweight corrugated metal sheets, operates through a series of specifically shaped rolls. These rolls craft a distinctive pattern onto flat metal strips, significantly enhancing their structural integrity without adding extra weight. The process not only amplifies the load-bearing capacity but also bolsters resistance against environmental factors, making it ideal for roofing and siding applications.
Over the years, advancements in technology have revolutionized corrugated rolling mills, integrating automated systems that enhance precision and efficiency. Industry experts attest to the transformative impact of digital control systems, which monitor parameters such as pressure, temperature, and speed during the rolling process. These technological strides ensure uniformity in product specifications and reduce the likelihood of defects, establishing a new standard of excellence.
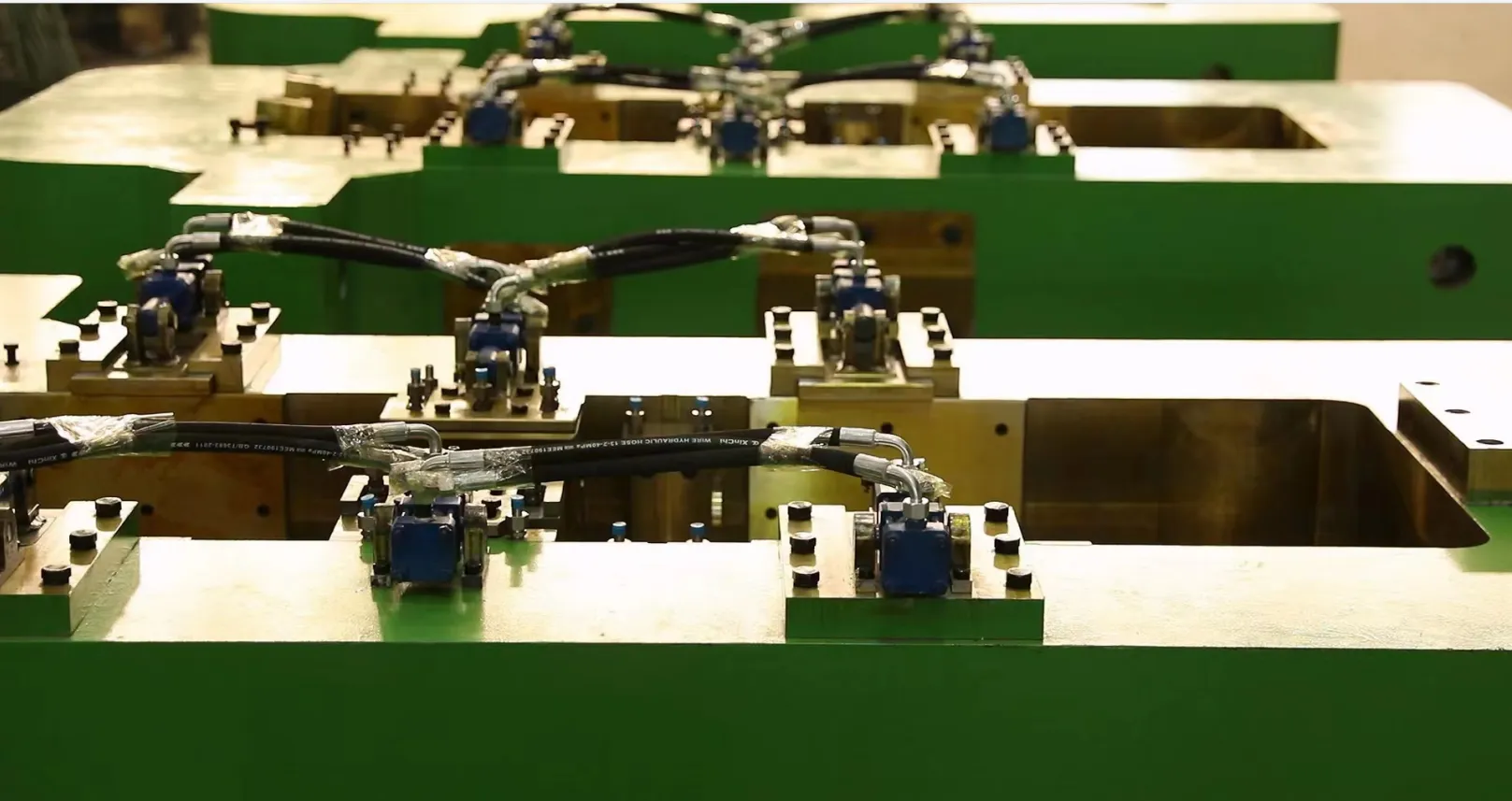
The expertise required to operate a corrugated rolling mill extends beyond basic mechanical knowledge. Operators must be proficient in handling advanced machinery, understanding metallurgical properties, and optimizing the rolling process for different material grades. Expertise is built through rigorous training and experience, as mill operators must swiftly adapt to anomalies and troubleshoot effectively to minimize downtime and maintain throughput.
corrugated rolling mill
Authoritativeness in the realm of corrugated rolling mills is reinforced by contributions from engineers and metallurgists who continuously refine rolling techniques and machinery design. Peer-reviewed studies and collaborative industry forums often highlight innovation in roll design, contributing to reduced energy consumption and enhanced sheet surface qualities. These developments underscore the authoritative nature of industry leaders who drive progress through research and practical implementations.
An essential aspect of corrugated rolling mills is their trustworthiness, particularly when related to product quality and safety standards. Manufacturers adhere to stringent quality assurance protocols, ensuring that the sheets produced are reliable and meet international standards. Materials utilized in the process undergo rigorous testing, and operational procedures are drafted to minimize risks and enhance overall safety, both for the workforce and the end-users of the fabricated sheets.
Real-world testimonials from companies utilizing these mills reveal the strategic advantages they provide. For instance, a leading construction firm reported a significant reduction in material costs after switching to corrugated sheets produced in-house using an advanced rolling mill. The company noted improved project turnaround times and enhanced durability of their constructions,
validating the mill's value proposition.
In conclusion, corrugated rolling mills embody a fusion of expertise, innovation, and reliability. Their pivotal role in manufacturing ensures that industries reliant on durable, lightweight materials can thrive. As technology continues to evolve, these mills are poised to become even more efficient, offering enhanced capabilities and setting new benchmarks in manufacturing. The ongoing dedication to quality, innovation, and safety cements their place as indispensable assets in modern production landscapes.