Automatic gauge control in cold rolling mills represents a transformational leap in manufacturing technology, setting new benchmarks for precision, efficiency, and quality in the metal rolling industry. With decades of advancements, this technology stands as a critical component in producing high-grade steel and aluminum products that meet the stringent standards of modern-day applications.
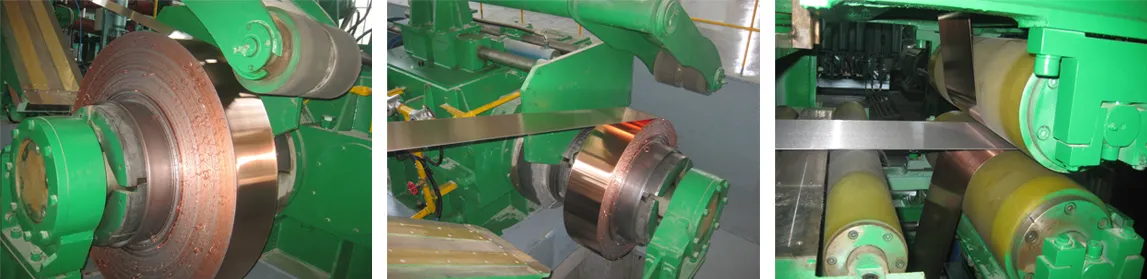
In the world of cold rolling, maintaining optimal thickness is crucial. Even minor deviations can lead to significant inconsistencies in the end product, impacting everything from structural integrity to aesthetic finishes.
Automatic gauge control, or AGC, addresses this challenge with unparalleled precision. By intelligently adjusting the rolls' positions in real-time, AGC ensures uniform thickness, enhancing both operational efficiency and product quality.
A firsthand experience with AGC showcases its transformative impact. Manufacturers who have integrated AGC into their cold rolling mills often report a significant reduction in material wastage. In traditional setups, operators manually adjust roll pressures, leading to potential delays and inaccuracies. AGC, however, utilizes sophisticated sensors and control systems, automating these adjustments far more accurately than human-operated processes. This automation results not only in increased throughput but also in decreased reliance on human intervention, reducing the likelihood of errors.
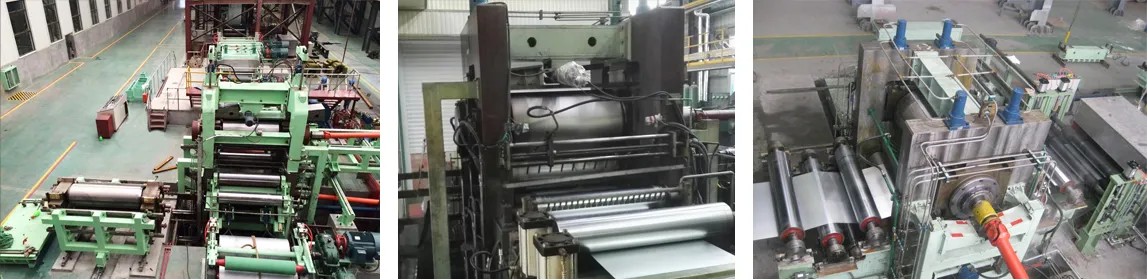
The expertise behind AGC systems can be dissected into several critical components sensor technology, control algorithms, and actuator precision. High-accuracy sensors measure the thickness of the material as it passes through the mill. These measurements are processed by advanced algorithms that determine the necessary roll adjustments to maintain optimal gauge. Actuators, driven by these algorithms, then fine-tune the roll positions with exceptional precision. This seamless integration of technologies underscores the specialist knowledge inherent in the design and implementation of AGC systems.
automatic gauge control cold rolling mill
Authoritativeness within the realm of automatic gauge control is often established by the pioneering companies that develop and refine this technology. Firms like ABB, Siemens, and Honeywell have spent decades not only perfecting the technology itself but also educating the industry about its benefits. Their extensive research and development efforts are backed by white papers, case studies, and peer-reviewed publications, lending significant credibility to the effectiveness of AGC.
Trustworthiness is perhaps the most tangible benefit that automatic gauge control brings to the table. When manufacturers switch to mills equipped with AGC, they can assure clients of product consistency, a promise backed by the reliability of precise manufacturing. This is particularly important in industries where even the smallest variance can lead to product failure, such as in automotive or aerospace applications. Customers in these sectors demand uncompromising quality, and AGC provides the assurance that only technologically advanced systems can deliver.
Cold rolling mills equipped with AGC are not just an investment in better machinery; they are a commitment to superior quality and efficiency. As manufacturers face increasing pressure to reduce costs while enhancing product quality, AGC offers a compelling solution. It exemplifies how modern technology can meet the traditional demands of manufacturing, leading to a new era of precision, reliability, and customer satisfaction. By embracing AGC, manufacturers position themselves at the forefront of their industry, ready to meet the challenges of a rapidly evolving market with confidence and expertise.