Rolling mills are a fundamental component in the manufacturing process of steel and other metals, providing the means to shape and form raw materials into finished products. Understanding the different types of rolling mills is crucial for industries to optimize their production processes and enhance product quality. This article delves into the various types of rolling mills, sharing insights from industry expertise and real-world experience to offer an authoritative perspective.
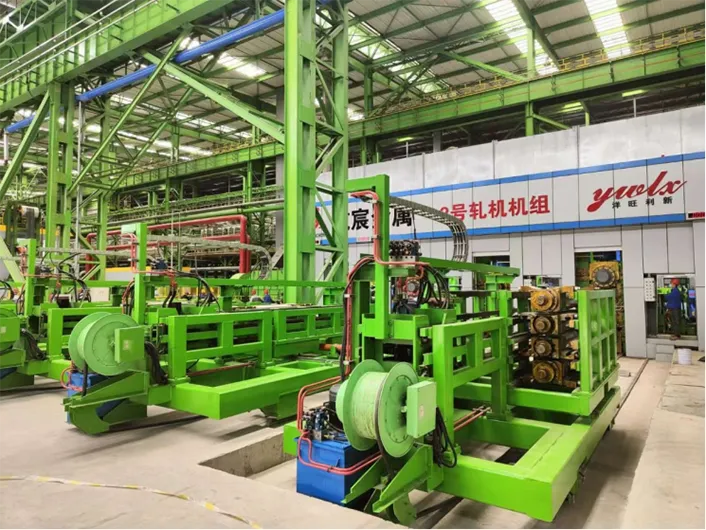
The first type of rolling mill to consider is the two-high rolling mill. This is the most basic form of a rolling mill, consisting of two opposing rolls that compress the material.
These are often used for initial breakdown passes on ingots or bars. The experience with two-high rolling mills suggests they are ideal for initial roughing passes due to their simplicity and ease of maintenance. However, their design limits the degree of control over the product dimensions and surface finish, a factor to bear in mind when precision is paramount.
For enhanced precision and control, the four-high rolling mills offer a better alternative. With two working rolls and two backup rolls, these mills provide the stability and precision necessary for thinner and more uniform output. Industry experts note their effectiveness in reducing variations in thickness and improving surface quality. When trust is a critical factor in manufacturing, four-high mills deliver the reliability required by high-specification industries, such as the automotive and aerospace sectors.
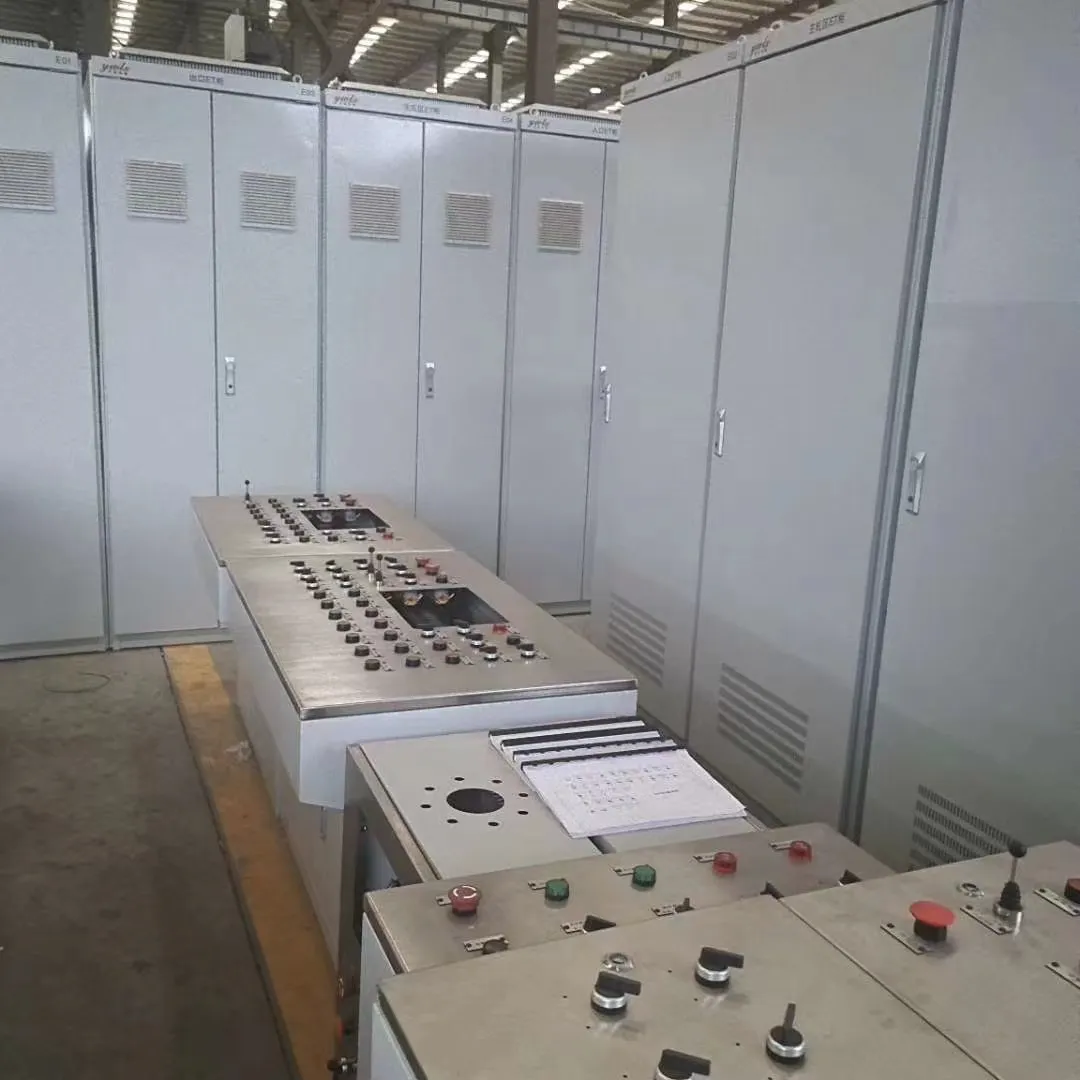
Moving to more advanced configurations, cluster rolling mills, often referred to as 12-high mills, leverage multiple smaller diameter rolls to achieve significant reductions in thickness. Expertise indicates that these mills are indispensable when producing very thin sheets of metal, where precision is critical, such as in the electronics industry. The numerous rolls allow for a more even distribution of pressure, diminishing the risk of deformation and ensuring uniformity. The authoritativeness of cluster mills is demonstrated in their widespread application for producing precision foils and delicate materials.
arten von walzwerken
In applications requiring even greater adaptability and production scale, continuous rolling mills offer significant advantages. These mills allow for an uninterrupted production line, where the material is fed in continuously. The inherent design fosters efficiency and scalability, making them indispensable in mass production settings. From an experiential standpoint, continuous mills require rigorous maintenance and constant monitoring to avoid interruptions and maintain trustworthiness in output quality. Their application is often seen in the production of long products like rails, beams, and rods.
For specialized rolling applications, planetary rolling mills and skew rolling mills provide unique benefits. Planetary rolling mills apply multiple rolls that orbit around a central roll, conducive to the production of large, high-strength materials like structural beams and plates. Skew rolling mills use rolls that are not parallel, often used for manufacturing ball bearings or other spherical products. These specialized mills, while not as commonly utilized as their counterparts, offer tailored solutions that demonstrate industry innovation and adaptability.
Finally, in the context of sustainability and modern industry demands, tandem rolling mills represent the intersection of efficiency and environmental accountability. By integrating multiple rolling operations into a single mill setup, these configurations reduce energy consumption and material waste. The expert consensus indicates that tandem mills are setting a new standard for eco-friendly production, aligning with the contemporary focus on reducing carbon footprints and enhancing operational sustainability.
The selection of the appropriate type of rolling mill depends on numerous factors including the desired material, product specification, production scale, and cost considerations. Mastery of rolling mill technology can provide companies with a competitive edge, ensuring product quality and operational efficiency while upholding industry standards. By understanding rolling mills' diverse applications and leveraging their distinct advantages, manufacturers can optimize their production processes and maintain trust in their products' performance.