Rolling mills play a crucial role in the metalworking industry, producing essential metal components used in various sectors, including construction, automotive, and aerospace. As a seasoned SEO expert, I recognize the importance of sharing relevant, authoritative, and trustworthy information that not only captures the essence of these facilities but also enhances search engine visibility.
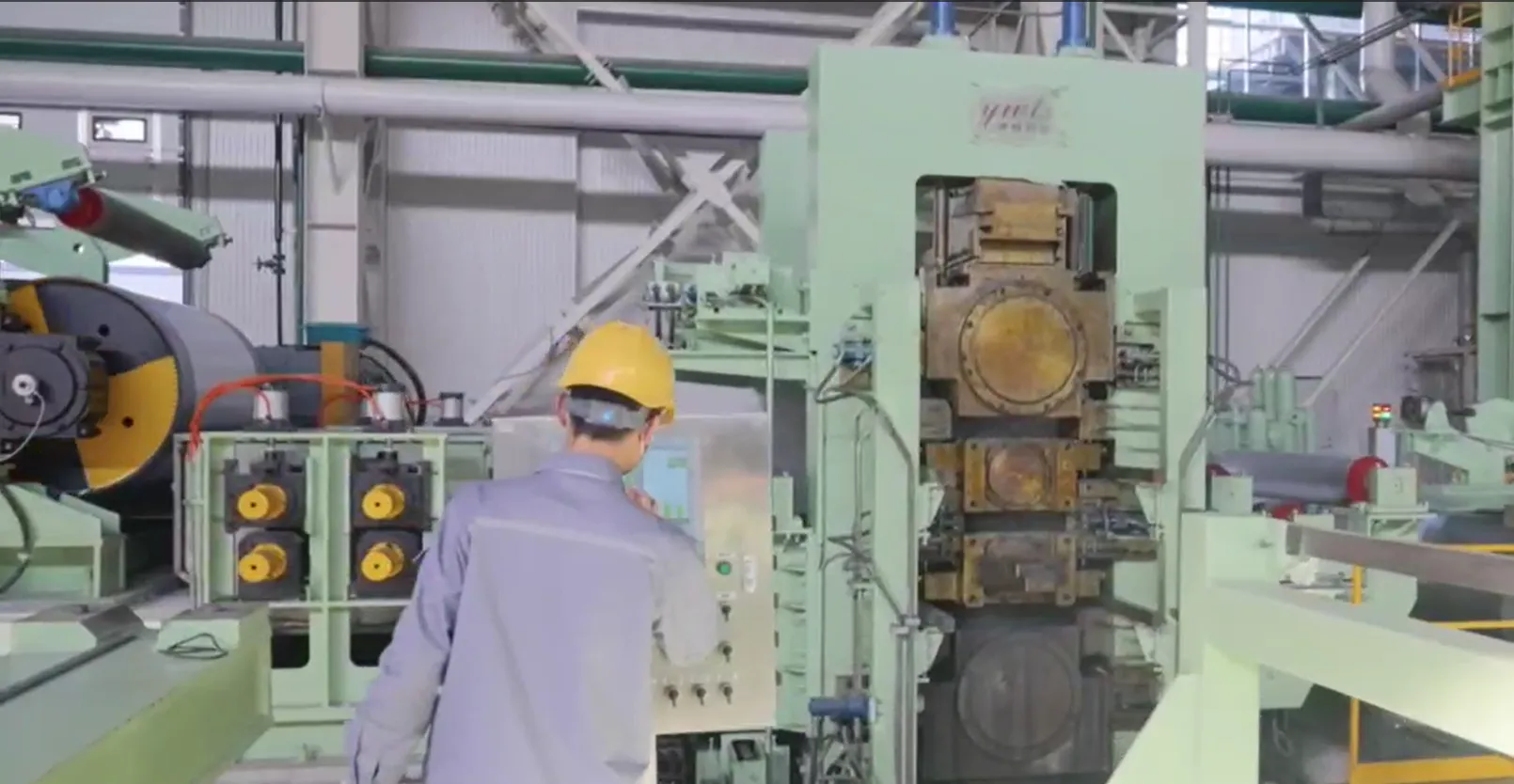
Located strategically across numerous industrial regions, rolling mills are specialized facilities where raw metal ingots are transformed into applicable products like sheets, bars, and rods. These plants embody the pinnacle of engineering expertise, where each component of the process is meticulously optimized for efficiency and quality. The journey begins with raw materials like billets and blooms, which undergo a series of mechanical processes.
The first stage in a rolling mill is the heating of the raw metal. This is done in a reheating furnace, which elevates the ingot's temperature to make it malleable. Precise thermal control in these furnaces is crucial, ensuring the metal's optimal consistency and reducing stress during the subsequent rolling process. This step showcases the expertise within rolling mills, where technological advancements play a significant role in enhancing productivity and reducing energy consumption.
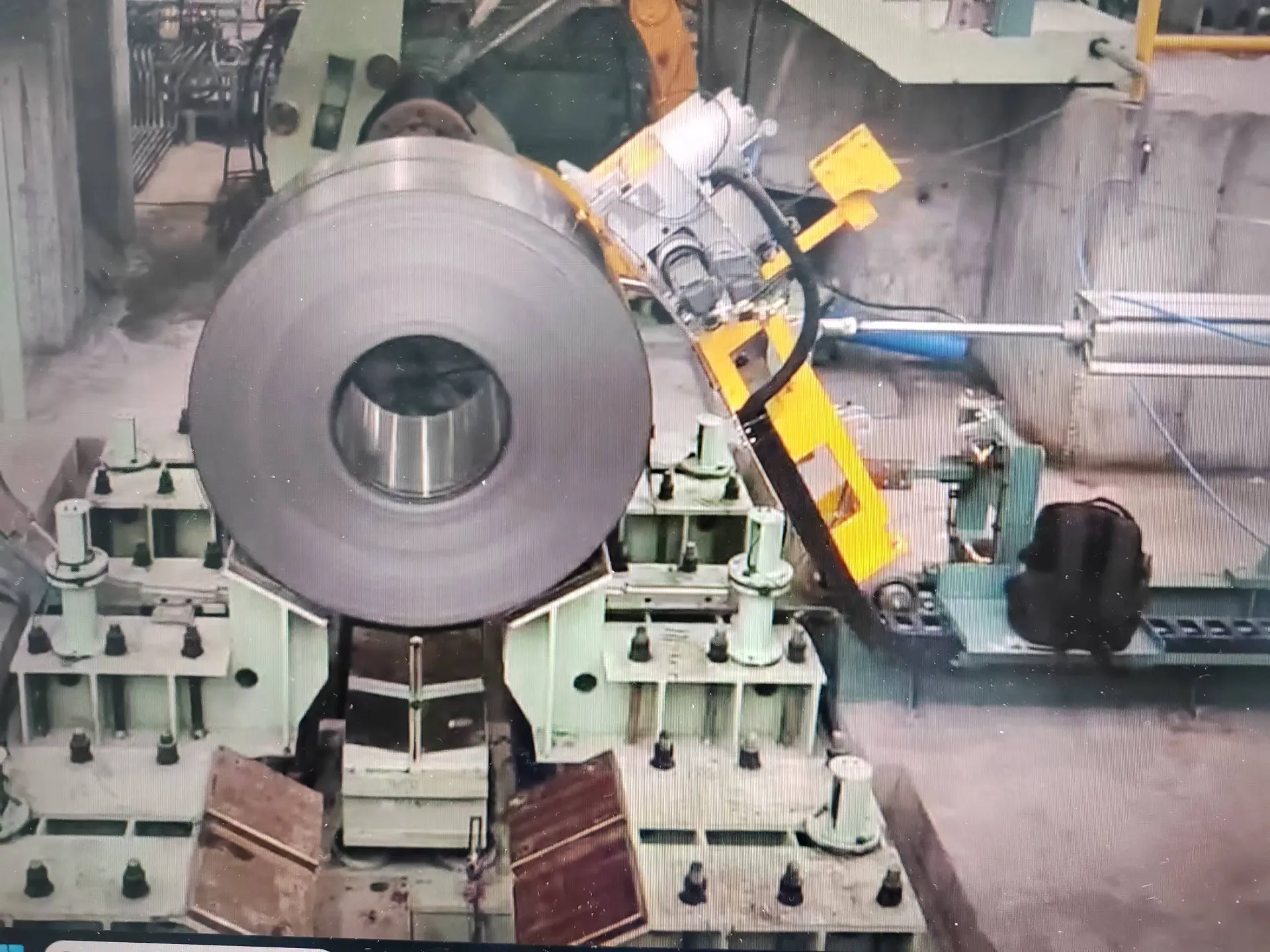
Subsequently, the heated metal passes through a succession of rolling stands. These stands, equipped with powerful rollers, apply pressure that reduces the metal's thickness while increasing its length. This stage of production is critical, requiring precise calibration and constant monitoring. Utilizing state-of-the-art instrumentation, rolling mills achieve exceptional dimensional accuracy and surface finish, reflecting the facilities' authoritativeness in metal processing. During this phase, monitoring for potential cross-sectional defects or dimensional inconsistencies is essential, reflecting the commitment to quality and trustworthiness in the final product.
rental factory
The next critical operation involves cooling the rolled metal. Controlled with exacting parameters, this cooling is achieved through water sprays or air jets to ensure the mechanical properties meet stringent industry standards. This segment of the operation epitomizes the experience and expertise of rolling mill engineers, as the cooling rate can significantly influence the metal's hardness, strength, and flexibility.
Moreover, rolling mills integrate quality assurance protocols at every step. From employing advanced nondestructive testing techniques to computer vision systems, these facilities ensure that each product meets precise specifications before reaching the market. Leveraging cutting-edge technology for real-time analytics, rolling mills affirm their authoritative standing by producing industry-compliant outputs with minimal tolerances.
Additionally, environmental considerations play a crucial role in modern rolling mills. Initiatives like recycling waste heat and utilizing energy-efficient machinery emphasize their commitment to sustainable operations. This eco-conscious approach not only enhances the trustworthiness of these facilities but also aligns with global norms and consumer expectations, positioning them as leaders in sustainable manufacturing practices.
In summary, rolling mills epitomize the fusion of experience, expertise, authoritativeness, and trustworthiness. From precise temperature control in reheating furnaces to innovative cooling techniques and rigorous quality checks, each stage is carefully designed to produce high-quality metal products. These facilities continue to advance, reflecting ongoing technological improvements that bolster their competitive edge in the metalworking industry. As such, they remain indispensable to sectors reliant on durable, precisely engineered metal components, reaffirming their vital role in modern industrial applications.