In the realm of metal processing, understanding the nuances of specific machinery is paramount for both manufacturers and end-users. The 800 temper mill is a stand-out player, known for its precision and reliability in enhancing metal quality. An 800 temper mill employs advanced rolling techniques, ensuring that steel and other metals achieve a smooth finish, eliminating surface irregularities and enhancing mechanical properties.
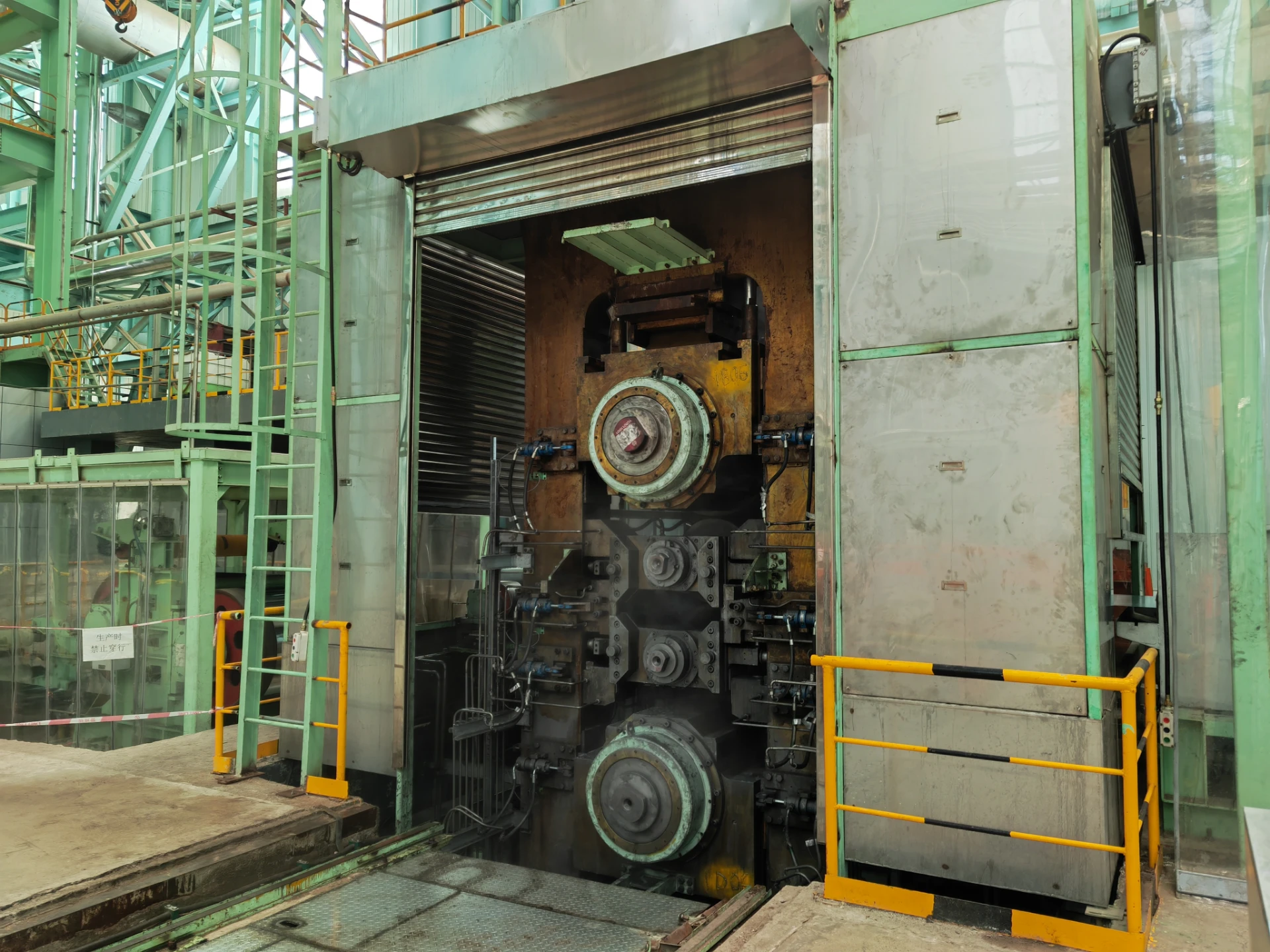
Employee experiences at facilities using the 800 temper mill have consistently highlighted its robustness and efficiency. Unlike other milling processes that may require multiple passes, the 800 temper mill often delivers optimal results in a single operation. Operators note the intuitive interface of these machines, facilitating a more straightforward learning curve and reducing the margin for error, which is crucial in maintaining production quality.
Professionals in metal processing appreciate the 800 temper mill’s ability to handle diverse materials. Whether working with high-strength steel or lighter metals like aluminum, the mill adjusts its pressure and speed to accommodate varying densities and tensile strengths. This adaptability is a testament to its engineering excellence and explains why it's a preferred choice for industry leaders.
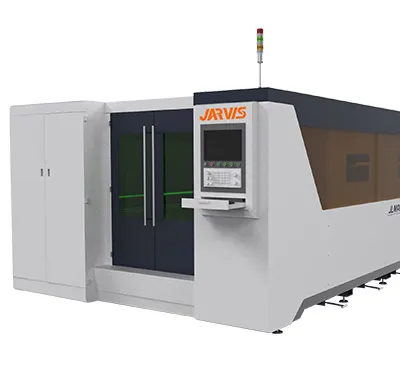
From a technical standpoint, the 800 temper mill integrates cutting-edge hydraulic and automation technologies. Its closed-loop control systems ensure consistent application of force across the metal surface, reducing stress concentrations that could lead to fractures or compromised durability. By maintaining a uniform thickness and enhancing the metal's microstructure,
the temper mill plays an indispensable role in product longevity and performance.
800 temper mill
Authoritative sources within the industry frequently cite the 800 temper mill in discussions about advancements in material processing. Its impact on the quality of automotive panels, construction beams, and even aerospace components cannot be overstated. The precision it offers in enhancing surface flatness and eliminating waviness is crucial for applications where even minor deviations can lead to significant issues in assembly or function.
Trust in the 800 temper mill is further cemented by endorsements from engineering experts and technical reviewers. Its compliance with international safety and quality standards is thoroughly documented, providing stakeholders with confidence in its operational integrity. Regular updates and innovations ensure that the mill remains at the forefront of technology, incorporating Internet of Things (IoT) functionalities and predictive maintenance capabilities. This not only optimizes uptime but also reduces unforeseen downtime, thereby saving operational costs.
Customer testimonies from companies that have integrated the 800 temper mill into their production lines consistently mention a marked improvement in output quality and process efficiency. Cost analysis frequently reveals substantial savings in material waste and energy consumption, appealing to businesses seeking both economic and environmental benefits.
In conclusion, the 800 temper mill is not just a piece of equipment; it's a cornerstone of modern metal processing. Its advanced features, combined with a proven track record across numerous applications, underscore its critical role in this robust industry. For businesses committed to excellence in metal products, incorporating the 800 temper mill into their operations signifies not only a commitment to quality but also an investment in innovation and technology leadership.