Setting up a compact steel plant dedicated to strip production demands a strategic approach integrating advanced technology and operational efficiency. This article delves into the nuances of establishing a proficient and environmentally sustainable steel manufacturing unit, focusing on producing high-quality steel strips. Our insights are derived from years of experience in the field, coupled with industry expertise and an unyielding commitment to innovation.
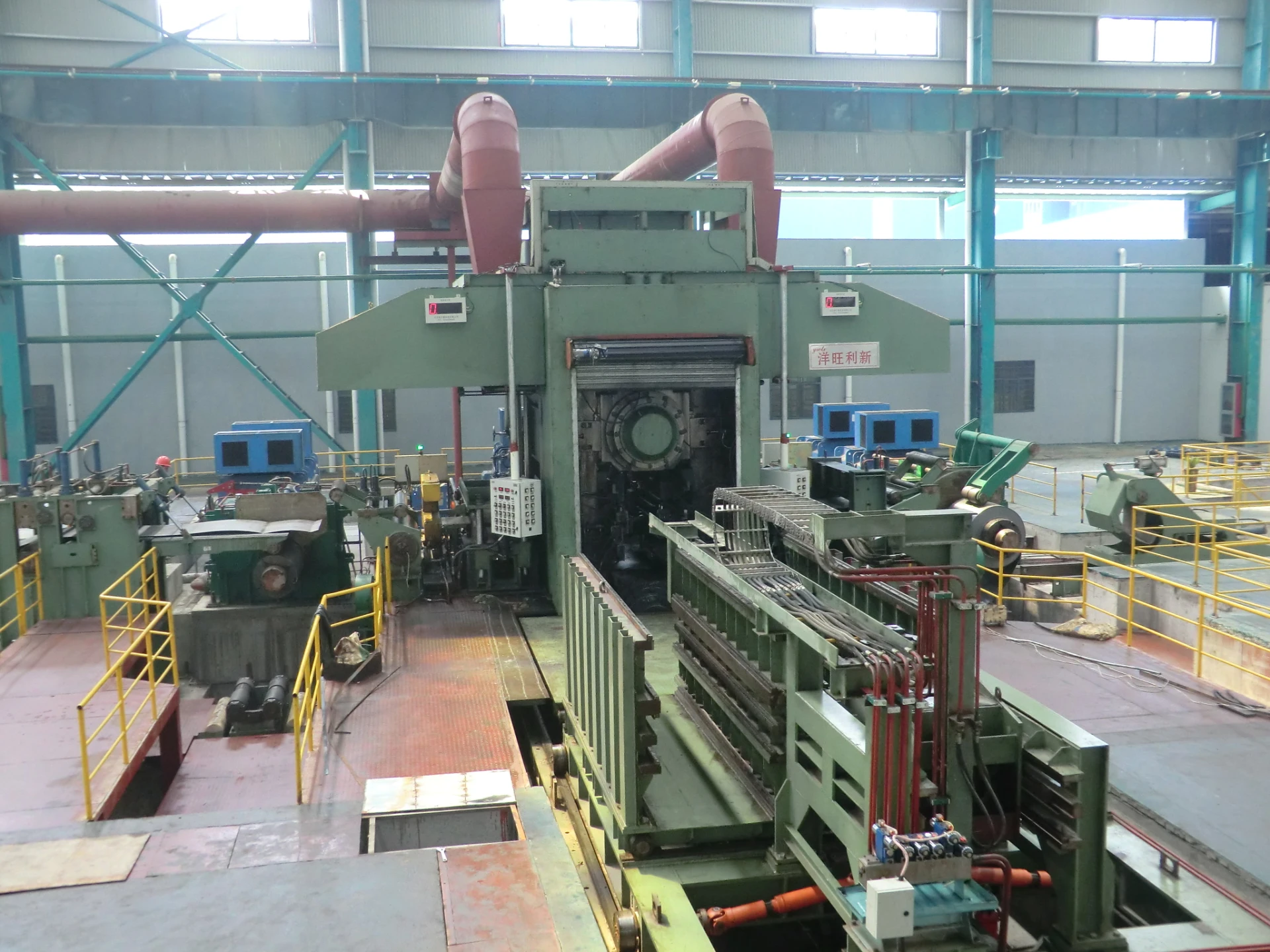
The inception of a compact steel plant starts with meticulous planning and design. Emphasizing compactness does not imply a compromise on capability or quality. Instead, it points to a streamlined, efficient layout that minimizes waste and maximizes output. Such plants incorporate cutting-edge machinery tailored for strip production, including continuous casting equipment and hot rolling mills. The integration of automation technologies further enhances precision and reduces manpower costs.
Expertise in metallurgy plays a critical role in achieving desired product characteristics. Compact steel plants capitalizing on expertise ensure that the manufacturing process aligns with the best practices in metallurgical engineering. This includes a thorough understanding of steel composition and the thermal treatments required to achieve specific strip qualities, such as tensile strength and flexibility, which are crucial for various industrial applications.
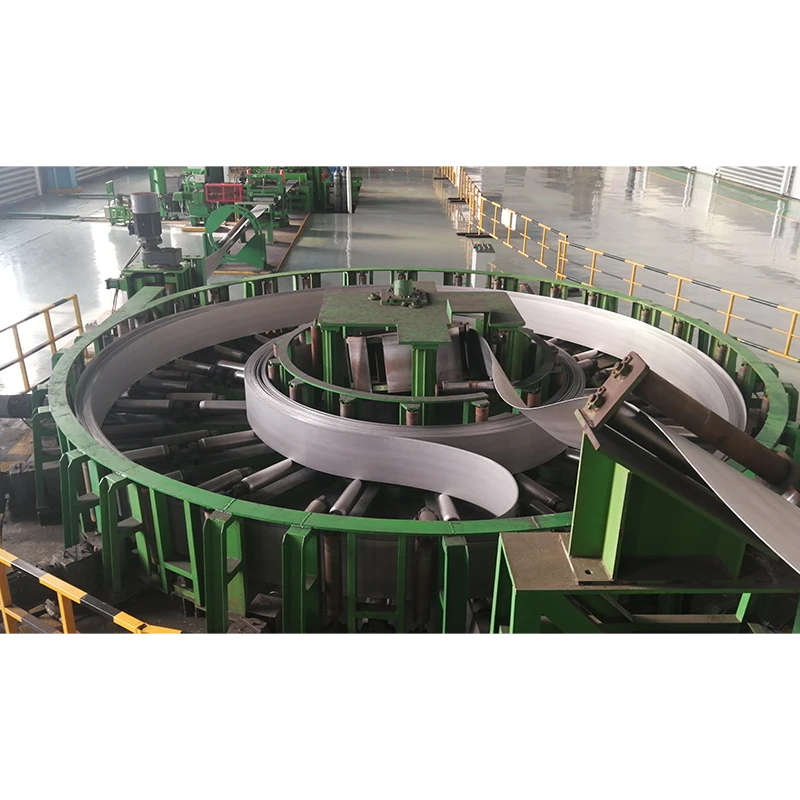
Authoritativeness in the steel manufacturing sphere is bolstered by compliance with international quality standards. A credible steel plant operates under stringent quality control measures, instituting rigorous testing at each production phase. This assures that the steel strips meet or exceed the expectations of customers across industries like automotive, construction, and appliances. Certification by reputable organizations not only attests to a plant’s operational excellence but also builds trust with clientele.
compact steel strip factory
Sustainability is another cornerstone of a modern compact steel plant. The industry is progressively moving towards reducing carbon footprints, and compact strip production facilities are at the forefront of this movement. By utilizing energy-efficient technologies, such as induction melting furnaces and recuperative burners, these plants significantly lower energy consumption. Moreover, implementing waste recycling systems, such as those that recover and reuse slag, positions a plant as environmentally responsible.
Trustworthiness is cultivated through transparent business practices and ongoing customer engagement. Establishing reliable supply chains and maintaining open communication channels with suppliers and clients underpins credibility. Regularly updating stakeholders on technological upgrades and process improvements conveys a plant’s commitment to maintaining high standards.
In conclusion, launching a compact steel plant specializing in strip production requires a foundation of solid experience and expert knowledge. By adhering to best practices in production and prioritizing quality assurance, environmental responsibility, and customer satisfaction, steel manufacturers can secure a dominant position in the market. These components collectively contribute to a plant's reputation as an authoritative and trustworthy player within the steel industry. The future of compact steel strip production is bright, paved with opportunities for those willing to innovate and lead with integrity.