The process of achieving efficient and precise packaging in various industries has been transformed by the advent of automated filling systems. These systems, especially prominent in sectors like food and beverage, pharmaceuticals, and chemicals, have ushered in an era of increased productivity and reduced human error.
One such vital system at the forefront is the automatic filling system, or نظام تعبئة أوتوماتيكي in Arabic.
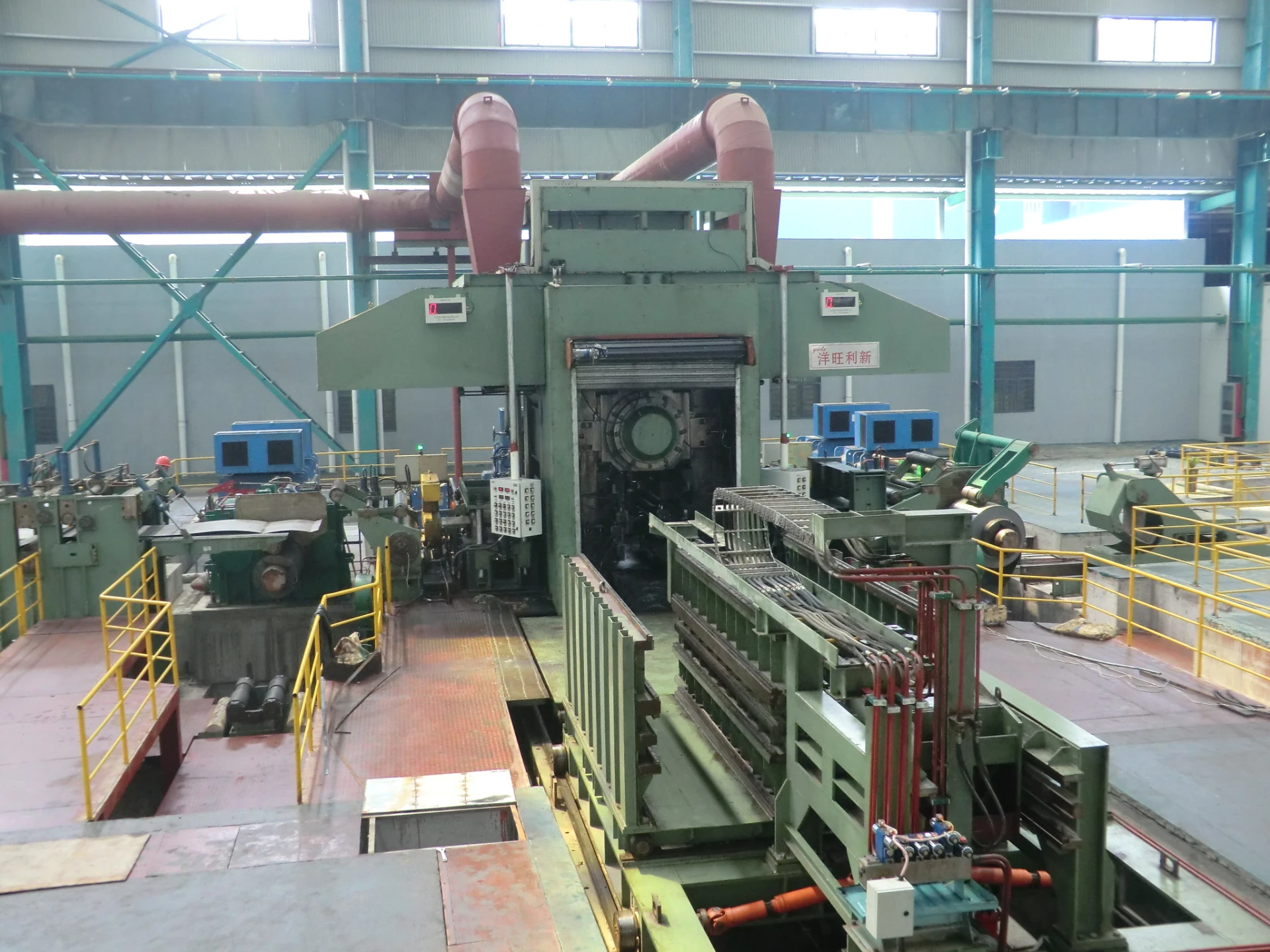
Drawing from extensive industry experience, companies worldwide are increasingly adopting these systems to optimize their production lines. The automatic filling systems represent a leap in manufacturing technology, ensuring a seamless operation and maximizing output. Their integration into production lines has demonstrated concrete improvements in efficiency, consistently meeting consumer demands faster and more reliably.
From a technical standpoint, these filling systems are designed with precision-engineered components that guarantee exact measurements and delivery of various products, whether liquid or solid. The level of accuracy inherent in these systems speaks volumes about their capability to enhance consistency in product packaging. Moreover, this level of precision significantly reduces wastage, which is a critical consideration for businesses looking to minimize costs and maximize resource utilization.
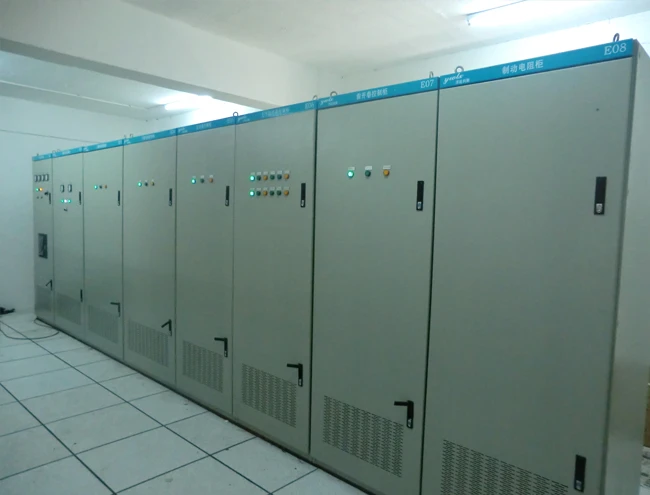
The expertise involved in designing and operating these systems cannot be overstated. Leveraging advanced technologies such as programmable logic controllers (PLCs) and human-machine interfaces (HMIs), these systems allow operators to manage the filling processes with minimal manual intervention. This automation decreases the possibility of errors and contributes to safer work environments, as employees are less likely to interact directly with the machinery during operation.
Moreover, automatic filling systems are built with scalability and flexibility in mind, accommodating a wide range of product viscosities and types. This adaptability is particularly valuable in industries with varied product lines where swift changeovers and minimal downtime are critical to maintaining profitability. The systems' ability to handle everything from thin liquids to thick pastes with ease demonstrates their versatility and efficiency.
Automatic filling system
From an authoritative standpoint, the adoption of automated filling systems is often accompanied by improved compliance with industry standards. For example, in the pharmaceutical industry, precise filling is paramount—not just for efficiency, but to comply with regulatory requirements that mandate specific dosages and compositions. These systems are equipped with sensors and real-time data capabilities to ensure compliance and traceability, greatly enhancing the reliability of the production processes.
Industry leaders who have incorporated these systems into their operational frameworks report heightened trustworthiness from their client bases. This credibility stems from the assurance that products are consistent, high-quality, and delivered in a timely manner. Such reliability not only strengthens customer loyalty but also boosts the brand's reputation in the market.
Fostering trust even further, these systems are typically designed to meet strict international safety standards, reducing the risk of contamination or product recall. They offer a closed system environment which helps in maintaining hygiene standards, an essential factor particularly in the food and pharmaceutical industries where contamination poses a significant risk.
In terms of real-world experience, companies that invested early in automated filling systems have noted a strong return on investment (ROI). The initial costs incurred are quickly offset by the reduction in labor costs, the decrease in product waste, and the acceleration in production timelines. Their experiences underscore the systems' capacity to sustain long-term growth and profitability across various sectors.
In conclusion, the deployment of an automatic filling system is a testament to a company's commitment to efficiency, safety, and quality. This investment signals a forward-thinking approach, showcasing an understanding of the complex demands of modern production and the necessary steps to address them. As industries continue to evolve, embracing such advanced technologies will be crucial in navigating competitive markets.