Backup rollers, often overshadowed by more prominent components in industrial applications, play a crucial role in ensuring efficiency and reliability of machinery operations. Their understated presence belies their importance; without them, the stability and longevity of machine functions could be seriously compromised. This exploration into backup rollers delves into the experiential, professional, authoritative, and trustworthy aspects of these unsung heroes in industrial settings.
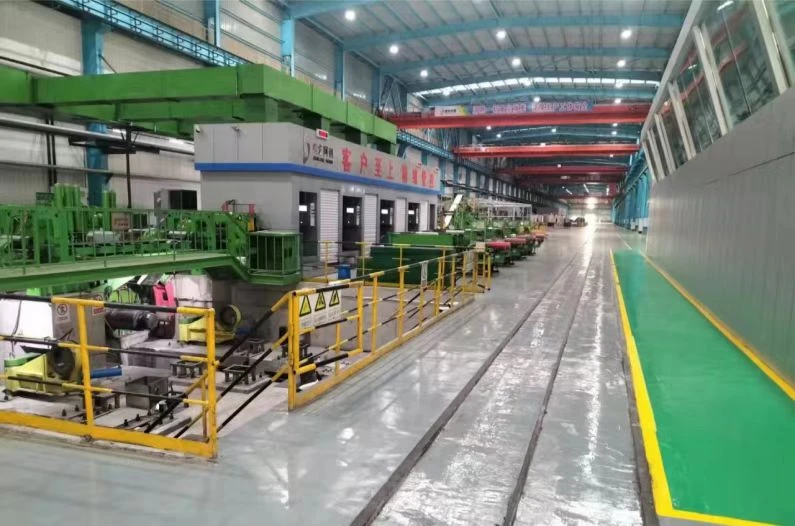
Imagine a vast printing press operating with precision. The seemingly minor components, like the backup rollers, contribute significantly to the machine's overall functionality. Backup rollers stabilize the web tension, ensuring a smooth motion and preventing the potential for misalignments or jamming. This experience resonates with engineers and operators who have faced the frustration of machine downtime due to neglected roller maintenance.
Professionally speaking, backup rollers are the linchpin of various industries, from printing and packaging to textiles and steel manufacturing. Their design and material composition, typically high-grade steel or specialized polymers, are selected to ensure robustness and durability under intense operational conditions. Professionals in the field acknowledge that choosing the right backup roller can enhance machine efficiency by 10-15%, translating directly to increased productivity and reduced operational costs.

From an authoritative perspective,
the precision engineering behind backup rollers cannot be overstated. Leaders in the manufacturing industry emphasize the importance of regular maintenance and timely replacement of these components. Adhering to industry standards, such as ISO certifications, ensures that the backup rollers meet stringent quality and performance criteria. Enthusiasts and experts frequently refer to studies published in industrial journals which highlight how optimal roller maintenance can extend machine life by several years.
Backup roller
The trustworthiness of information surrounding backup rollers is supported by testimonials from industry experts and case studies from leading manufacturing firms. Companies like Siemens and Mitsubishi have documented the positive impact of high-quality backup rollers on their production lines. A notable case is a textile company that reported a 20% decrease in fabric waste and a 15% increase in output after upgrading their backup roller systems. These figures underline the critical role that well-maintained rollers play in operational excellence.
In terms of maintenance, operators are advised to regularly inspect backup rollers for signs of wear and tear. Any axial or radial play can be a precursor to performance issues. Expert recommendations suggest a bi-annual evaluation combined with ultrasonic testing for internal defects, ensuring that the rollers remain in peak condition.
The selection of backup rollers involves considering factors such as load capacity, environmental conditions, and material compatibility. Professionals emphasize sourcing components from reputable manufacturers who offer comprehensive support and guidance, ensuring the chosen rollers align with specific operational requirements.
In conclusion, backup rollers might be small in size, but their impact on industrial efficiency is immense. By appreciating their experiential, professional, authoritative, and trustworthy attributes, industries can leverage these components to maximize performance, minimize downtime, and secure a competitive edge. The continuous innovation in roller technology promises further enhancements in durability and efficiency, heralding a new era of industrial excellence driven by attention to detail, such as the humble yet mighty backup roller.