Effective tension control in winders is a crucial aspect of optimizing production efficiency and product quality across various industries, ranging from textiles and paper to film and foil manufacturing. Mastery in managing the tension of materials during winding processes not only enhances the longevity and performance of manufacturing equipment but also guarantees the consistency and reliability of the final product.
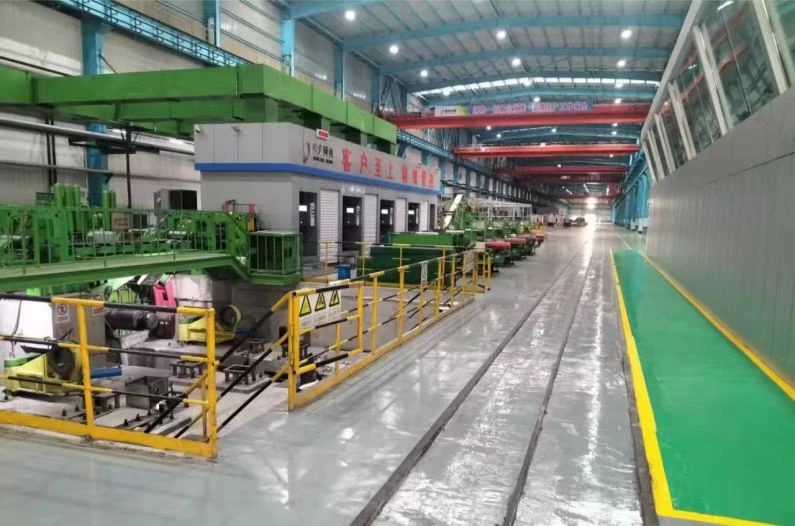
When discussing tension control, it is pivotal to understand the dynamics involved in a winding operation. The core objective is to maintain a constant tension, which is influenced by factors such as material elasticity, thickness, and speed of the winder. Any deviation from the set tension parameters can lead to defects such as wrinkles, telescoping, or breaks, which can adversely affect the end product.
Advanced tension management systems often employ a combination of load cells, tension sensors, and programmable logic controllers (PLCs) to monitor and adjust tension parameters in real-time. These systems provide critical feedback that is used to fine-tune the tension, ensuring optimal winding performance. By employing such cutting-edge technology, manufacturers can significantly reduce waste, lower operational costs, and improve output quality.
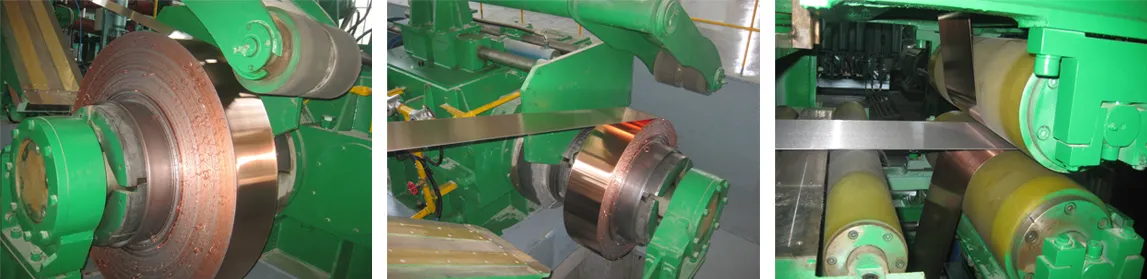
Experience in this field shows that regular maintenance and calibration of tension control equipment are paramount.
Operators must be trained to interpret data from tension sensors and implement adjustments promptly. This level of expertise is fundamental in preventing operational hiccups and maintaining the consistent quality of wound products.
winder tension management
Authoritative voices in the industry often recommend integrating closed-loop tension control systems. These systems automatically adjust the winder speed and torque to maintain consistent tension, thus offering a more streamlined and reliable solution compared to open-loop systems. The advantage of closed-loop systems is their ability to correct any aberration instantly, providing smooth and efficient winding processes that minimize material waste and downtime.
A trustworthy tension control system is predicated upon the reliability and precision of its components and the proficiency of its users. This is why selecting reputable manufacturers who offer robust after-sales support and training is critical. Investing in high-quality, durable equipment ensures long-term performance stability and minimizes the risk of unexpected failures.
Furthermore, adopting an integrated approach, wherein all components of the winding process harmonize seamlessly, can significantly boost operational efficiency. For instance, integrating web guiding technologies with tension control systems helps in maintaining alignment and reducing variations that could impact the winding quality.
In conclusion, effective tension management is not just about maintaining optimal operational conditions, but also about investing in advanced technologies, training personnel, and choosing reliable equipment. By focusing on these elements, companies can ensure superior product quality, enhance productivity, and establish their reputation as leaders in quality manufacturing. Through sustained dedication to excellence in tension control, businesses can forge a path to greater efficiency and competitive advantage in the global market.