Hot rolled coils, known in Arabic as شرائط مدرفلة على الساخن, represent a fundamental component in the industrial production landscape, recognized for their versatility and reliability. These steel products are fabricated by rolling steel at high temperatures, typically over 900°C, above the recrystallization temperature of the steel. This process gives the coils an unparalleled combination of strength and ductility, making them indispensable in multiple industrial sectors.
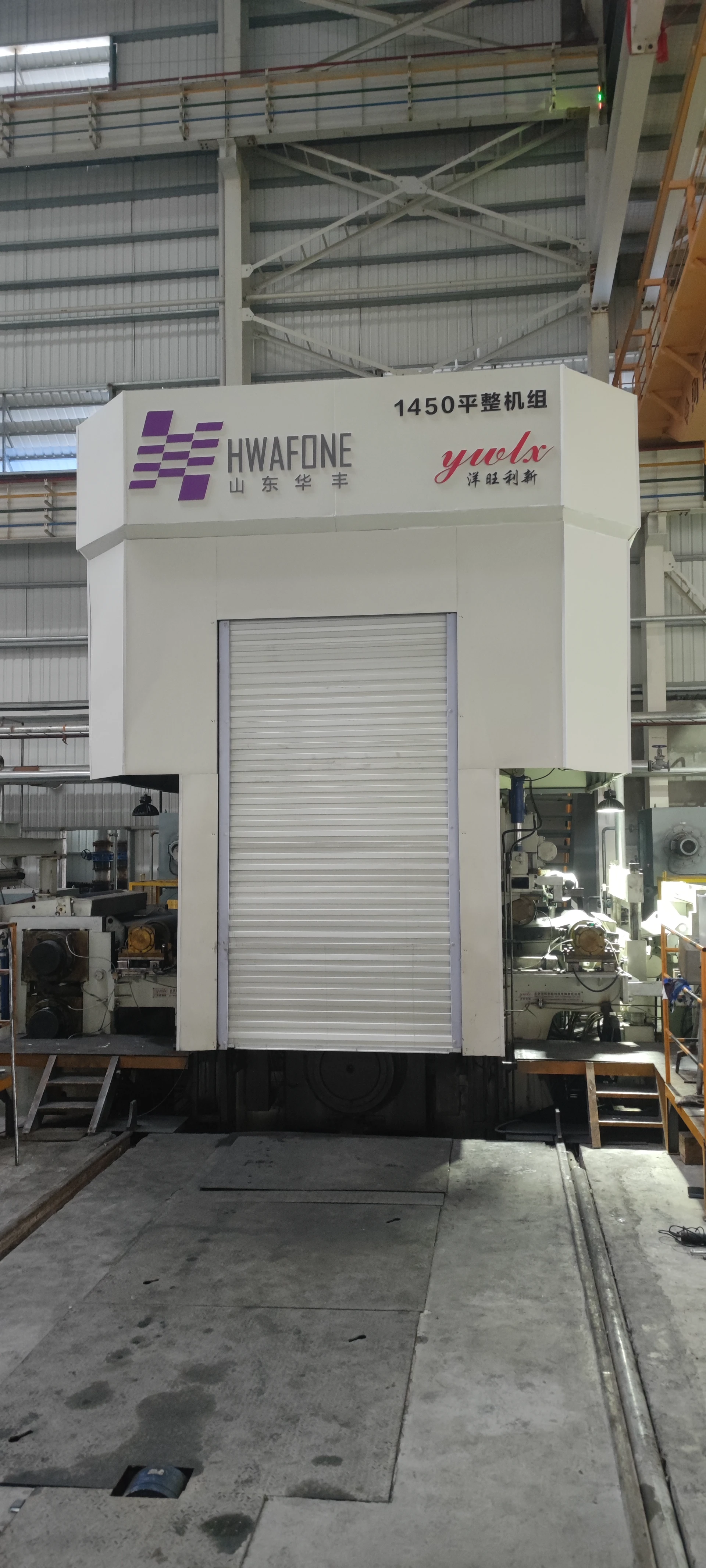
An insider’s view into the manufacturing process highlights that hot rolling not only reshapes the metal but also refines its mechanical properties, resulting in a product with enhanced formability that is indispensable for applications requiring medium to high strength. These characteristics make hot rolled coils the material of choice in construction, automotive, and heavy machinery manufacturing.
In construction, for instance, hot rolled coils provide the backbone for structural components due to their robust mechanical properties. Engineers rely on these coils for the fabrication of beams, columns, and infrastructure frameworks. The ability to withstand high stress and load makes them ideal for skyscrapers, bridges, and industrial facilities.
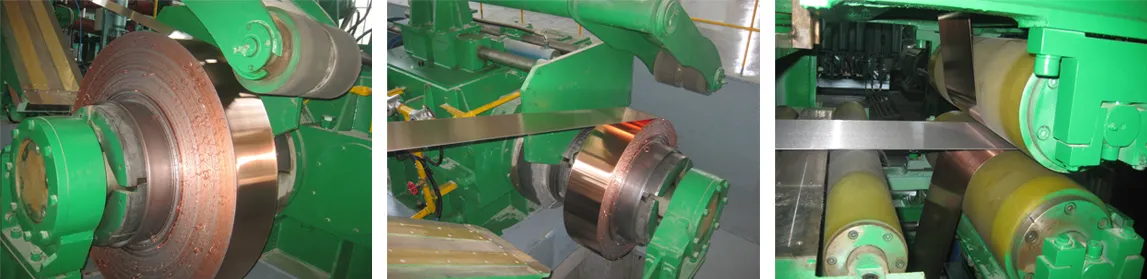
Automotive manufacturers utilize hot rolled coils to create body frames and support structures that require both strength and flexibility. By using hot rolled steel as a foundational material, car manufacturers ensure enhanced crash resistance, durability, and overall safety in their vehicles.
When discussing the advantages of hot rolled coils, it's essential to delve into their cost-effectiveness and processing efficiency. The production technique involves fewer steps compared to cold rolling, which significantly reduces manufacturing costs. This economic efficiency, combined with substantial time savings in production, enables manufacturers to meet high demand quickly - a competitive advantage in fast-paced markets.
Hot rolled adhesive tape
In terms of expertise,
leveraging hot rolled coil technology requires a comprehensive understanding of metallurgical principles. The high-temperature process not only affects the steel's physical state but also modifies its microstructure on a granular level. Specialists in materials science collaborate with engineers to optimize the properties of these coils—such as tensile strength, surface finish, and dimensional precision—to suit specific project requirements.
Authoritative sources in the industry often cite the adaptability of hot rolled coils to different treatments as a key aspect of their continued prominence. For instance, applying various surface treatments can enhance corrosion resistance or add a protective layer, extending the service life of the final product. Furthermore, advancements in hot rolling technology, such as the development of high-strength alloys and improved rolling techniques, speak to the innovative potential within the sector.
For businesses utilizing these products, the trustworthiness factor hinges on choosing suppliers who adhere to stringent quality standards. Verified certifications and compliance with international standards are crucial in ensuring product reliability and meeting safety benchmarks. Trust is built through rigorous testing and quality assurance processes that guarantee each coil's performance aligns with specified engineering criteria.
In summary, hot rolled coils are more than just raw materials; they are cornerstones of modern manufacturing, underpinning the infrastructure and technology that drive economic growth. Companies looking to integrate these products into their processes must rely on a blend of experience, expertise, authority, and trust to harness their full potential, ensuring success across a myriad of demanding applications.