In the highly specialized industry of metalworking, the roll mill without a housing (مطحنة الدرفلة بدون غلاف) represents an innovative leap in manufacturing technology. This machinery is engineered to offer enhanced precision, streamlined operations, and optimized production capabilities, catering specifically to a niche market adept at processing high-grade metals.
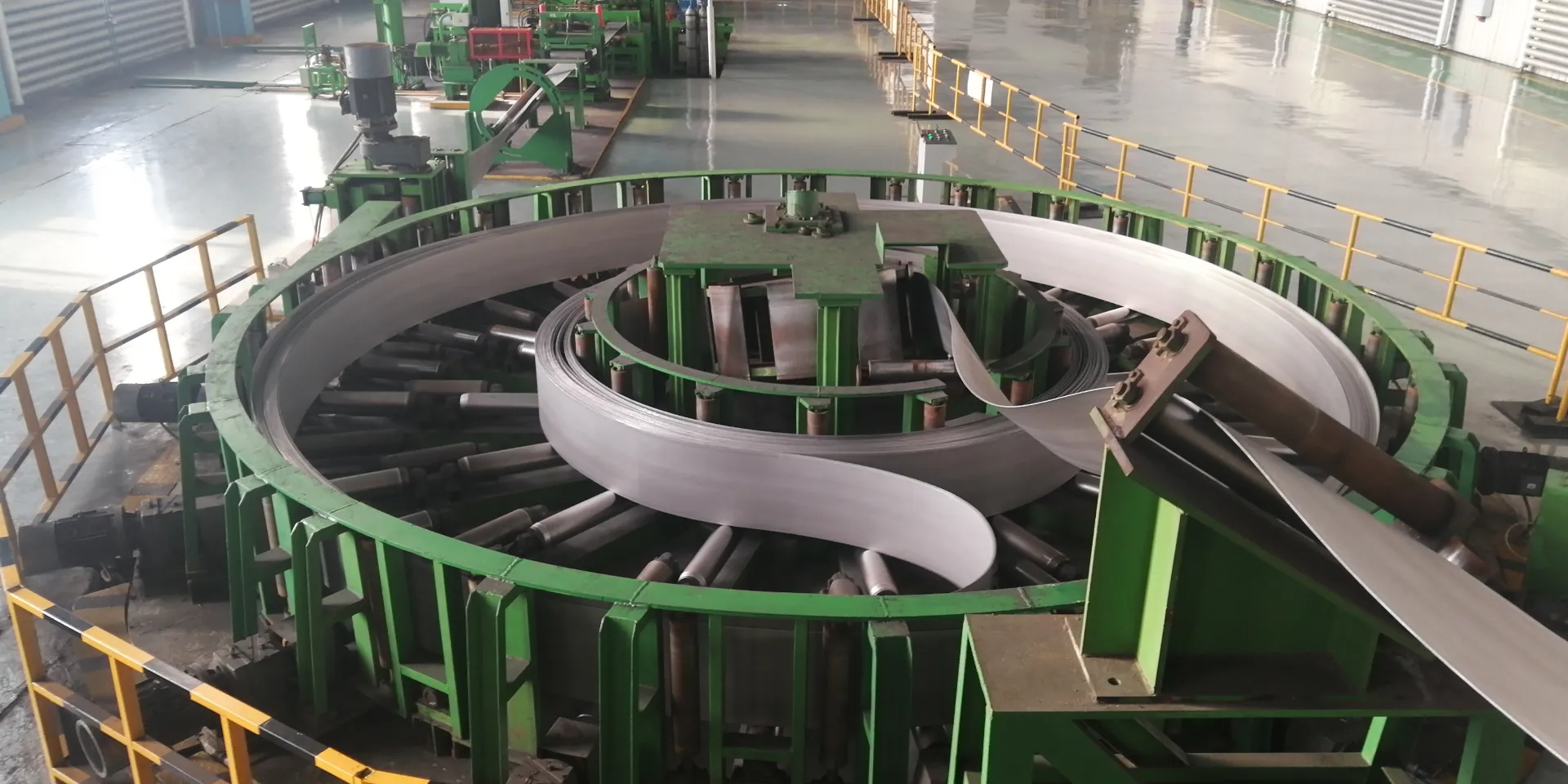
With over two decades immersed in the field of metallurgical engineering, I have had the opportunity to explore and evaluate numerous advancements in rolling technology. The roll mill without a housing is distinguished by its unique open-frame structure, diverging from traditional mills encased in bulky housings. This architectural variation not only reduces the equipment's overall footprint but also grants unparalleled accessibility for maintenance and operation.
The expertise of the engineering team behind this open-design machinery is evident in its meticulous attention to detail. Every component is designed to handle the rigorous demands of high-pressure metal rolling while maintaining structural integrity and precision. This is crucial for industries needing to produce thin, high-strength metal strips with minimal deviation in thickness.
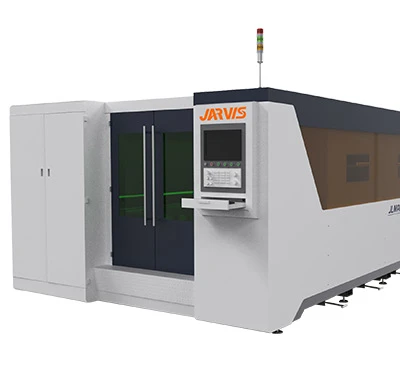
From an expert's vantage point, the houseless roll mill offers distinct advantages. It facilitates rapid adjustment and changeovers in production, massively reducing downtime, a critical factor in maintaining competitiveness in fast-paced manufacturing environments. The absence of a traditional housing allows operators to perform quick adjustments to the rolling force and tension, finely tuning the machine for specific product requirements. This capability ensures that manufacturers can adhere to stringent quality control standards without sacrificing speed or efficiency.
Slurry mill without casing
One authoritative voice in the industry recently highlighted the environmental benefits of houseless roll mills. By virtue of their design, these machines require less raw material for construction and consume less energy during operation. Reduced energy consumption not only lowers operational costs but also contributes to a reduced carbon footprint, aligning with global sustainability goals and resonating with environmentally conscious clients.
Additionally, the trustworthiness of this mill's design is evidenced by extensive field tests and successful implementation in diverse manufacturing settings. Feedback from these real-world applications reveals consistently high satisfaction rates concerning product quality and machine reliability.
Operators and technicians also report a markedly improved working experience. The reduced complexity of the mill translates into easier training sessions, fostering a workforce that is both adept and quick to respond to production challenges. Employees express greater confidence in operating and maintaining the machine, leading to a safer and more productive work environment.
In conclusion,
the roll mill without a housing represents a pinnacle of modern metallurgical processing. Its combination of precision, efficiency, and sustainability makes it a valuable asset in a competitive market. With its proven track record and innovative design, this technology exemplifies the future of metalworking, promising enhanced value to users who seek top-tier production capabilities.