Rod mills have revolutionized the mining and materials processing industries, positioning them as an indispensable asset for professionals seeking uniform grain size reduction. These efficient machines are primarily employed in mineral processing facilities, where they grind ores and other materials into smaller, even particles. This characteristic differentiates rod mills from other milling solutions, underlining their critical role in ensuring smooth downstream processing. The robustness and versatility inherent in rod mills make them appealing not only in mining but also in cement production, coal processing, and even the recycling industry.
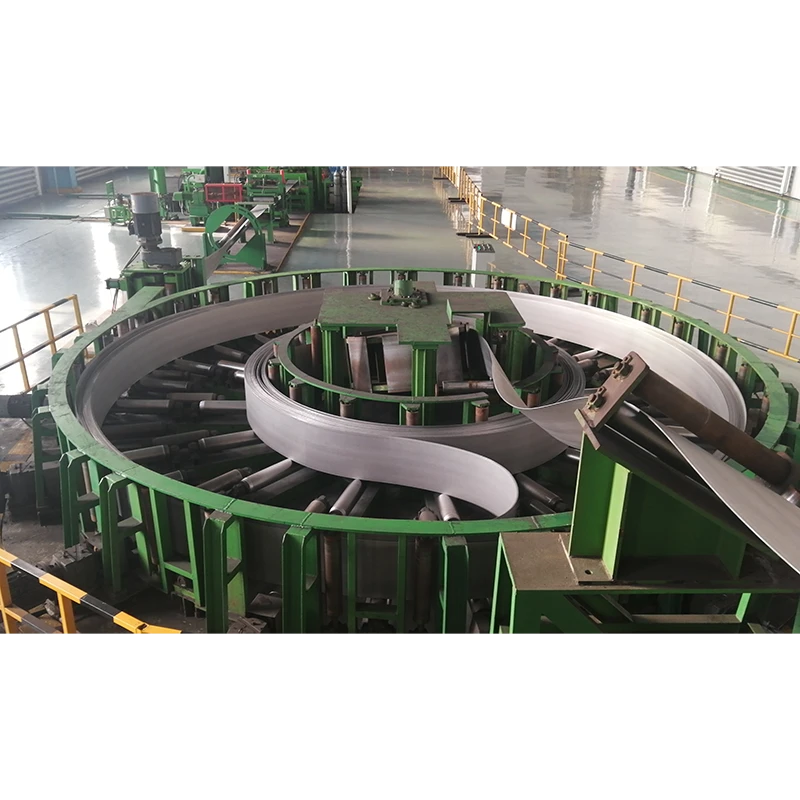
Operating a rod mill requires a nuanced understanding of its mechanism to maximize its potential truly. Typically, these mills consist of long cylindrical tubes filled with rods that function as the grinding media. As the drum rotates, centrifugal force is generated, causing the materials to grind against each other within the mill. This unique process is known as cascading action, which results in a product that boasts consistent granularity and higher surface area; it ensures uniformity in size, an aspect highly valued in mineral processing.
A notable advantage of rod mills is their ability to minimize over-grinding. This aspect becomes crucial when processing minerals for subsequent separation processes such as flotation. By reducing the formation of slimes, rod mills contribute positively to the recovery rate and purity of the end product. This translates to tangible benefits in operations, making these mills an economically sound choice for many facilities. Furthermore, their design inherently reduces the need for complex machinery and high energy consumption, providing both cost-effectiveness and environmental sustainability.
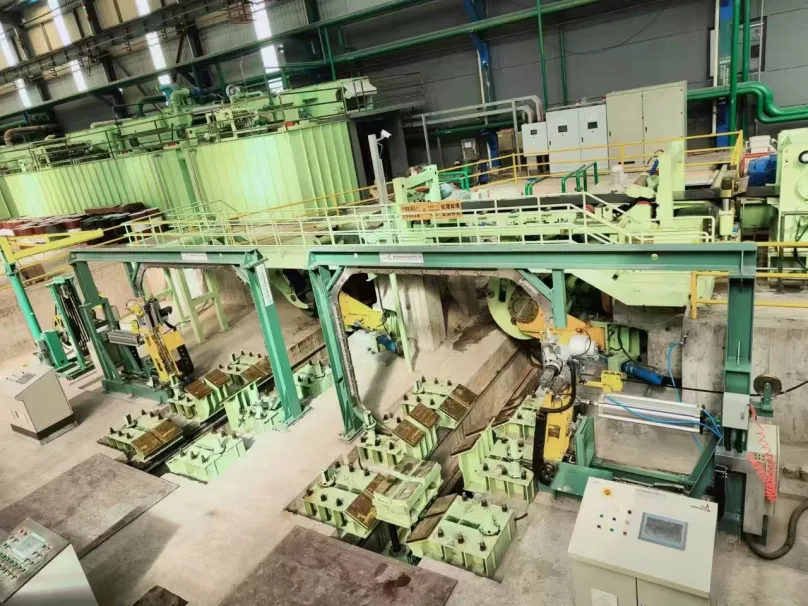
The choice of material for the rods within the mill is another significant consideration demanding expertise. Rod mills typically utilize steel rods for their grinding needs, chosen based on hardness, composition, and wear life. Selecting the appropriate rods can enhance energy efficiency and produce a finer product. Expert operators often adjust the rod load, mill speed, and ore characteristics to optimize performance, requiring a blend of skills and practical knowledge to navigate these parameters effectively.
Rod mills
Trust in the performance of rod mills stems from their historical reliability and contributions to productivity improvements across various industries. Continuous technological advancements have further elevated their performance capabilities. For instance, automation and process control technology have significantly improved operational efficiency, providing real-time monitoring and adjustments. Such innovations enhance the mill’s authoritativeness, earning industry trust through consistent output quality.
Industry experience depicts that maintenance plays a pivotal part in preserving the milestones achieved by rod mills. Scheduled inspections and proactive component replacements are crucial to ward off potential downtime. A meticulously maintained rod mill not only avoids unexpected failures but also ensures that all operations remain aligned with intended production goals. Documentation and adherence to operational guidelines bolster trustworthiness, ensuring that these machines deliver as promised regardless of the conditions under which they operate.
Conclusively, the role of rod mills extends beyond mere material reduction; they embody a synthesis of technology and operational expertise. Regular professional training and updates become essential in maintaining the relevance and efficiency of these processors in an ever-evolving industry landscape. As environmental regulations tighten and demand for energy-efficient processing methods grows, rod mills continue to demonstrate their indispensability with remarkable efficiency and reliability, substantiating their position at the heart of modern mineral processing facilities.