Wire rolling machines are an essential component in the manufacturing industry, playing a pivotal role in shaping and refining metal wires for various applications. Understanding the intricacies of these machines not only enhances operational efficiency but also ensures product quality and compliance with industry standards. Leveraging years of expertise in the field, this article delves into the core aspects of wire rolling machines, offering insights that stem from real-world experience and authoritative knowledge.
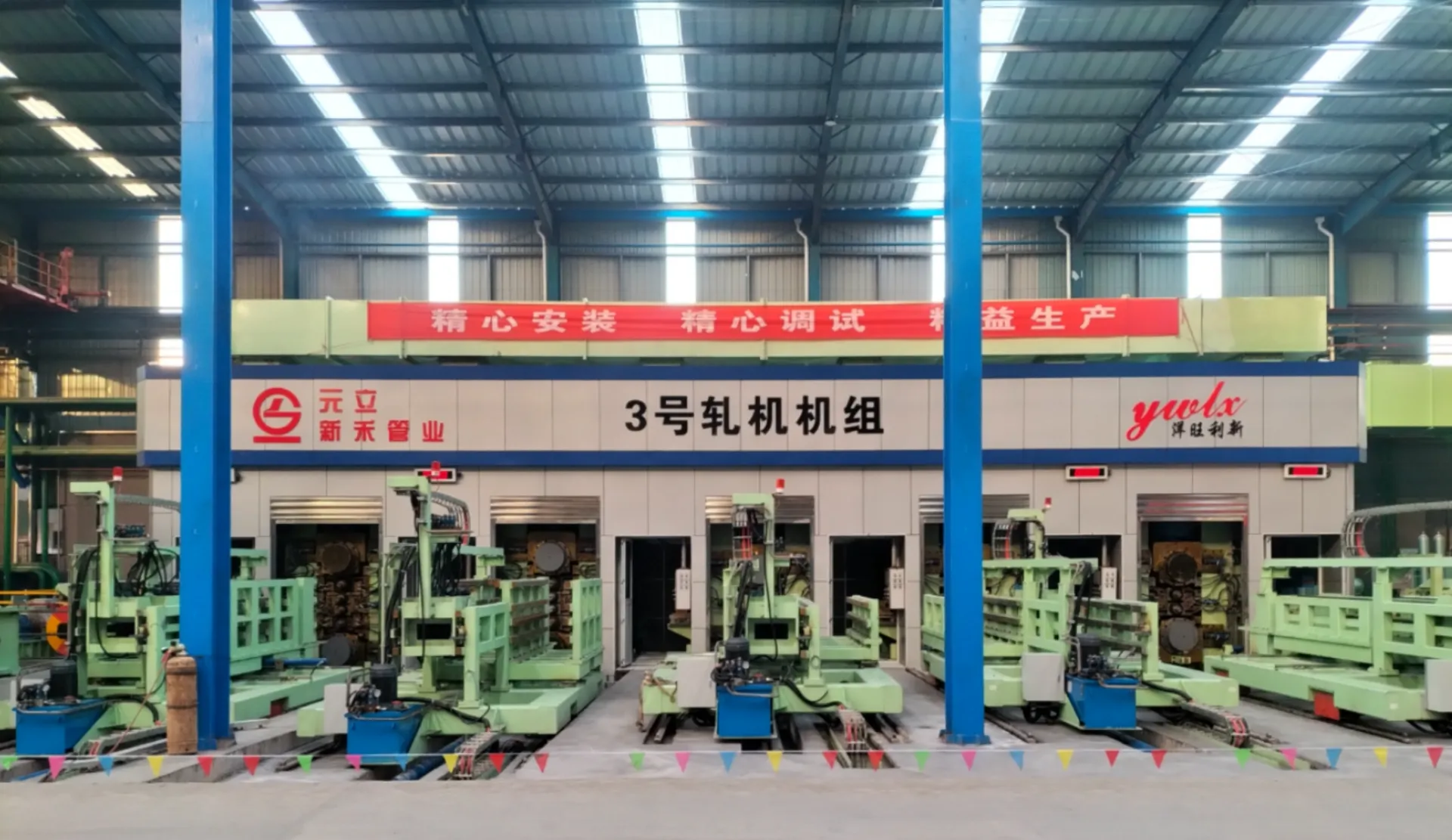
Wire rolling machines are designed to transform raw metal into precisely shaped wires, suitable for a wide range of industrial applications. These machines function by passing metal stock through multiple rollers, which refine the diameter and shape of the wire incrementally. The process involves a careful balance of pressure, speed, and temperature, factors that demand a deep understanding and precise control to achieve optimal results.
Experience in operating wire rolling machines reveals that the choice of materials significantly impacts the final output. For instance, copper and aluminum require different roller configurations compared to harder metals like stainless steel. The tensile strength, ductility, and thermal expansion properties of the material dictate the specific adjustments needed. Seasoned operators often rely on a meticulous approach that involves regular calibration of machines and adjustments based on material properties, ensuring consistency and high-quality output.
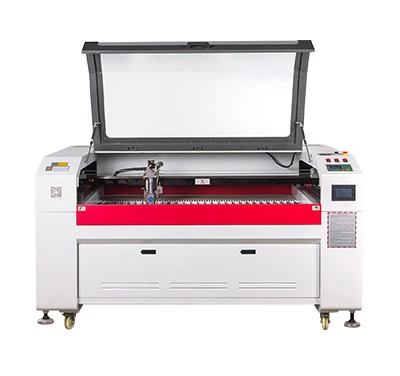
The expertise drawn from prolonged engagement with wire rolling machines highlights the importance of maintenance and timely upgrades. Wear and tear of rollers and other mechanical components can lead to deviations in wire dimensions, impacting product integrity. Scheduling regular maintenance checks, replacing worn-out parts, and updating software for computerized machines are crucial steps in maintaining operational efficiency. Moreover, advanced models equipped with digital interfaces and sensors provide real-time data, allowing operators to make informed adjustments and predict potential issues before they arise.
wire rolling machine
Authoritativeness in the domain of wire rolling is often demonstrated through a commitment to adhering to industry regulations and standards. Compliance with ISO certifications and other relevant standards not only guarantees the safety and quality of the wire produced but also enhances the credibility of the manufacturer. It reflects an understanding of regulatory requirements and a proactive approach to ensuring that the manufacturing process aligns with these guidelines.
Trustworthiness in managing wire rolling operations is built through transparency and continuous improvement. This includes offering comprehensive training programs for operators, fostering an environment of knowledge sharing and skill enhancement. Manufacturers who invest in the latest technologies and foster a culture of innovation position themselves as leaders in the industry, trusted by clients and partners alike.
In conclusion, wire rolling machines are instrumental in the efficient production of metal wires, with their operation resting on a foundation of experience, expertise, authoritativeness, and trustworthiness. A keen focus on material properties, maintenance, regulatory compliance, and technological advancement ensures that these machines deliver optimal performance, quality, and reliability. For businesses seeking to excel in the production of metal wires, investing in high-quality wire rolling machines and nurturing a skilled workforce are essential strategies for achieving sustained success and trust in the marketplace.