Brass rolling mills hold a pivotal role in the manufacturing landscape, serving as the backbone for producing high-quality brass components used across diverse industries. Understanding the intricacies of brass rolling mills requires not only technical know-how but also a first-hand insight into the processes that ensure product excellence.
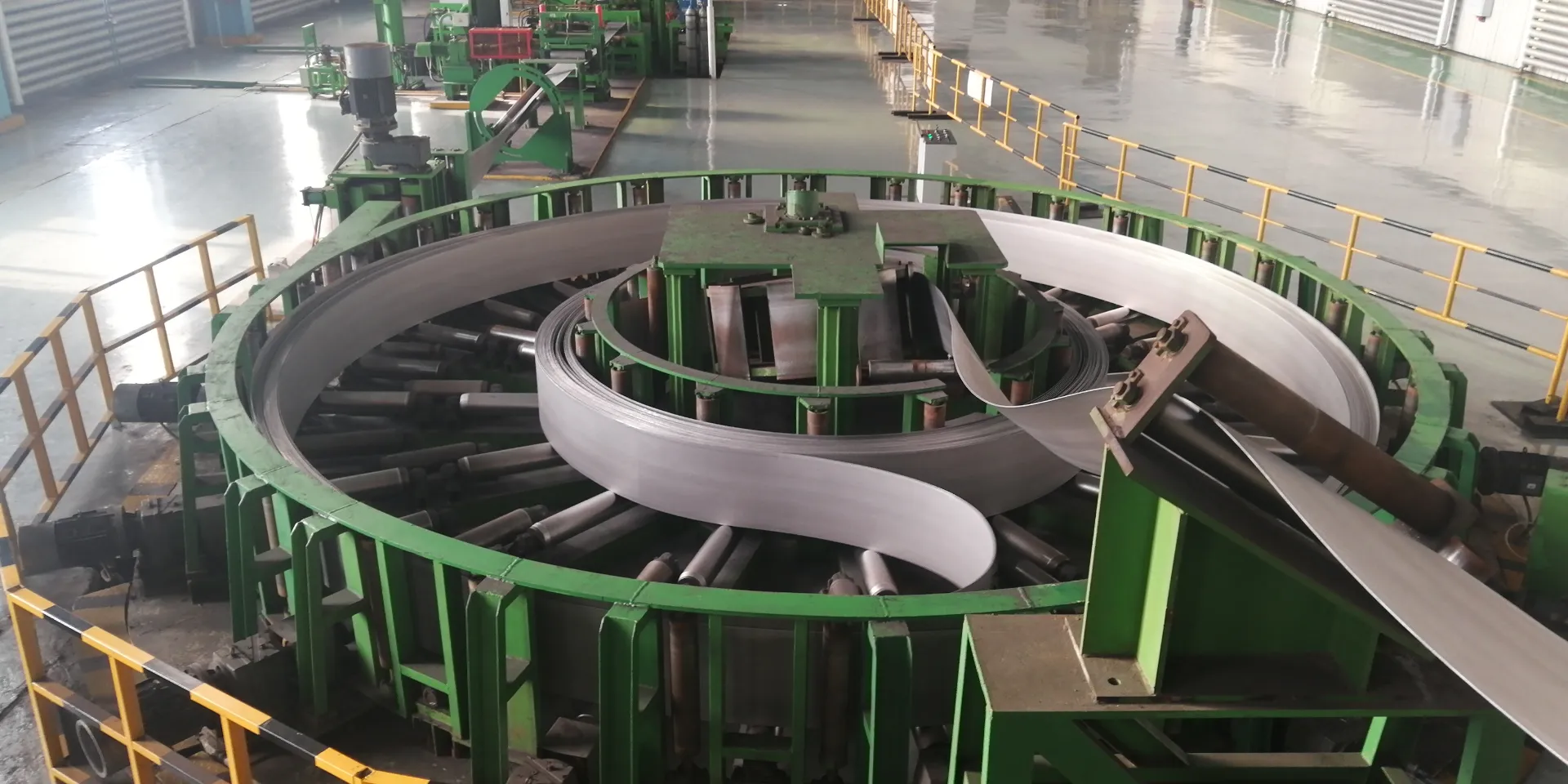
The essence of a brass rolling mill begins with its capability to transform raw brass into fine sheets or coils with precision. Expertise in this domain starts with comprehending the metallurgy of brass itself—a copper-zinc alloy known for its durability, malleability, and resistance to corrosion.
The success of a rolling mill depends on its ability to leverage these properties efficiently.
My experience with brass rolling mills has demonstrated their pivotal role in delivering a product that meets stringent industry standards. Notably, the rolling process is not merely about flattening brass into sheets. It involves a meticulous control of temperature and pressure to achieve desired thickness and mechanical properties. This attention to detail ensures that the final product is not only functional but also aesthetically pleasing, a critical factor in applications like architecture and musical instruments.
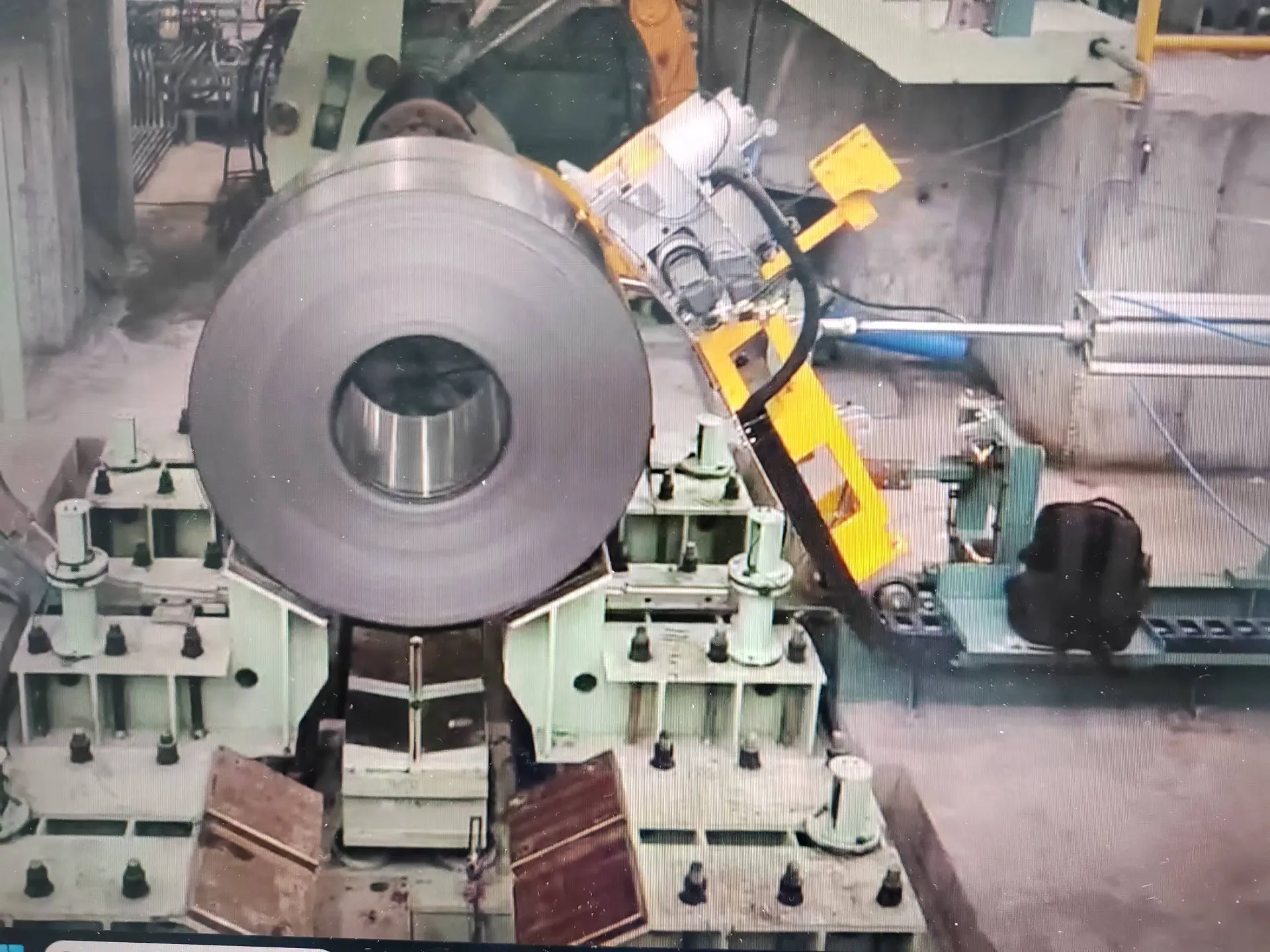
With a nuanced understanding, the operation of a brass rolling mill can be considered an art form, blending engineering with craftsmanship. Recent technological advancements have introduced automated and computerized controls into these mills, enhancing both precision and efficiency. These innovations are spearheaded by industry leaders known for their authoritative expertise and commitment to quality. Among them are companies that persistently push the envelope in developing sustainable and environmentally friendly solutions, ensuring their operations leave the smallest possible carbon footprint.
brass rolling mill
One of the hallmarks of trustworthy brass rolling mills is their ability to guarantee consistency and reliability. Industry leaders conduct extensive testing on their products, utilizing both in-house labs and third-party verifications to certify that every batch meets the rigorous compliance standards demanded by sectors such as automotive and electronics. The integrity of these products often hinges on the meticulous scrutiny applied during every stage of the rolling process—from initial casting to the final rolling.
Anecdotal evidence gathered from experts paints a picture of the versatility of products yielded by brass rolling mills. Architects praise brass sheets for their enduring beauty and strength in facades, while the electronics industry relies on their conductivity. It is no surprise, then, that the expertise behind a well-run brass rolling mill transitions beyond technical specs. It involves a profound understanding of client needs and ensuring that the brass's intrinsic qualities align perfectly with the intended application.
For any entity seeking to invest in brass rolling mills or incorporate their products, authentication of the manufacturer’s claims is paramount. A due diligence process that involves reviewing case studies, testimonials, and historical data of product performance is essential to verify the manufacturer's trustworthiness. Exemplary mills often come with a legacy of performance that is verifiable and recognized in industry circles for their authoritative capabilities.
In conclusion, the journey of a piece of brass from a rolling mill to its final application is one marked by a synthesis of experience, expertise, authoritativeness, and trustworthiness. These are not mere buzzwords but the very pillars that uphold the standard of excellence expected in the brass rolling industry today. With ongoing innovations and an unwavering commitment to quality, brass rolling mills remain indispensable to the industries they serve.