The world of industrial production is a dynamic landscape where precision, efficiency, and innovation intersect. One of the key instruments driving this synergy is the wire rolling machine, known in German as the Drahtwalzmaschine. This sophisticated equipment is not just machinery but an embodiment of engineering prowess and industrial excellence. The following exploration delves into the intricate functionalities, advantages, and experiential insights surrounding wire rolling machines, providing an authoritative perspective designed to enhance search visibility and drive engagement.
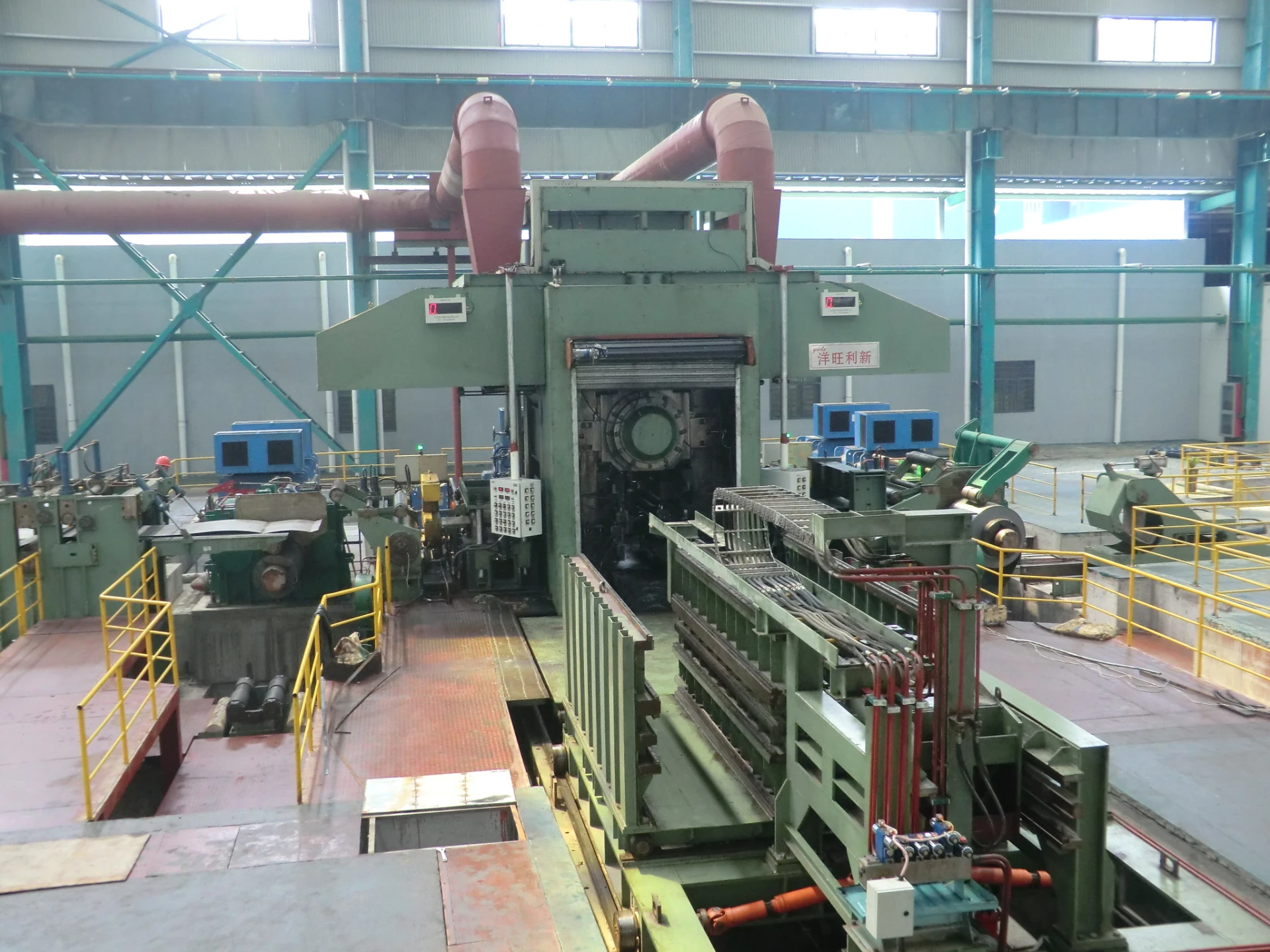
At its core, the wire rolling machine serves to reduce the diameter of metal wires by passing them through a series of rolling stands. The process is meticulous, leveraged by its ability to handle various metal types, including copper, aluminum, and alloyed steel, thus ensuring its applicability across diverse industrial sectors. The expertise embedded within this equipment lies in its advanced design, which integrates high-precision rollers and automated control systems. These elements work harmoniously to ensure uniformity in wire dimensions, enhancing the quality and durability of the final product.
Numerous industries rely heavily on the capabilities of wire rolling machines. In the realm of electrical engineering, for instance, these machines are critical in producing conductive wires with precise dimensions necessary for efficient electrical transmission. Similarly, in the automotive industry, wire rolling machines contribute to manufacturing processes demanding lightweight yet resilient wires for various components. Such versatility and reliability underlie the expertise that this machinery brings to industrial applications.
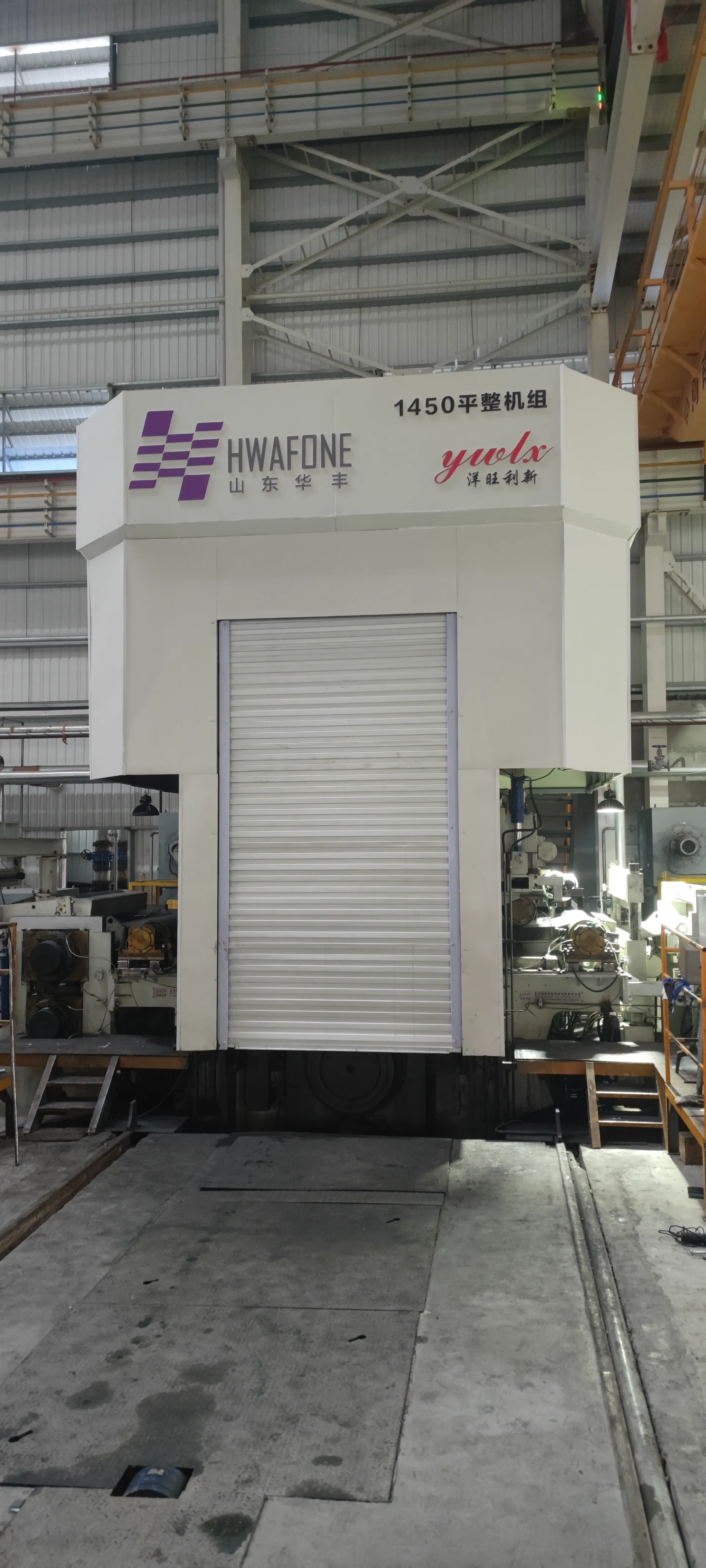
Experience reveals that one of the most compelling benefits of wire rolling machines is their ability to enhance production efficiency. Through automation and precise control, these machines significantly reduce the need for manual intervention, allowing for continuous operation and higher production outputs. The result is not only enhanced productivity but also lower operational costs, as the efficiency of the machinery translates into reduced energy consumption and minimal material waste.
The innovation embedded in wire rolling machines extends to customization capabilities. Advanced models are designed with flexible programming systems that allow manufacturers to tailor the rolling process according to specific project needs. This adaptability is a crucial factor contributing to the authority of these machines in the domain of industrial manufacturing, as it provides businesses with the competitive edge needed to meet ever-evolving market demands.
drahtwalzmaschine
Trust in wire rolling machines is further reinforced by their robust construction and adherence to stringent safety standards. Manufacturers often leverage cutting-edge technology and premium materials to build machines that can withstand the rigors of high-capacity production environments. Moreover, safety features such as emergency stop functions, protective enclosures, and automated monitoring systems ensure safe operation, thus fostering trust among operators and stakeholders.
In addition to the technical advantages, the use of wire rolling machines also supports sustainable practices in manufacturing. By optimizing resource utilization and minimizing waste, these machines contribute to eco-friendly production processes, aligning with global sustainability goals and enhancing the social responsibility profile of companies.
For businesses seeking to invest in wire rolling machines, expert recommendations emphasize conducting thorough needs assessments to align equipment capabilities with production goals. Collaborating with reputable manufacturers who offer comprehensive support services, including installation, maintenance, and training, further enhances the investment returns, ensuring long-term operational success.
In sum, the wire rolling machine represents a pinnacle of industrial machinery where expertise, innovation, and reliability converge. Its adoption not only signifies an upgrade in manufacturing capabilities but also reflects a commitment to quality, efficiency, and sustainable practices. As industries continue to evolve and demands grow, this powerful tool remains indispensable, driving progress and setting the standard for excellence in wire production.