In the ever-evolving field of metal processing, the 4 high skin pass mill stands as a paragon of technological advancement and operational efficiency. These mills are engineered to provide superior surface finish and higher material strength, aligning with the market's stringent quality requirements. The application of a 4 high skin pass mill in production lines not only enhances product quality but also optimizes operational workflows, reflecting the intricate balance between mechanical prowess and precision engineering.
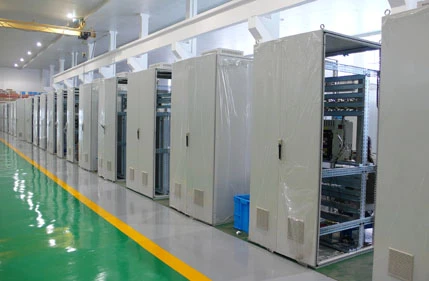
Experience in operating a 4 high skin pass mill reveals several key advantages that contribute to its increasing demand across various industrial sectors. The robustness of the four-roll design allows the system to exert controlled pressure during the skin passing process, substantially improving the flatness and surface texture of the metal sheet. Operators who have worked extensively with these mills often highlight the machine's ability to eliminate surface irregularities and minor metal defects, rendering the final product aesthetically appealing and structurally sound.
From an expertise standpoint, the setup and calibration of a 4 high skin pass mill require meticulous precision. Expertise in this domain involves understanding the dynamics of force distribution across the rolls and mastering the adjustment of roll gap settings to achieve desired material properties. Engineers emphasize the importance of synchronized roll movements, which can be monitored through advanced computerized systems. Such systems provide real-time feedback, enabling fine-tuning of the process parameters to compensate for material variations and maintain consistent output quality.
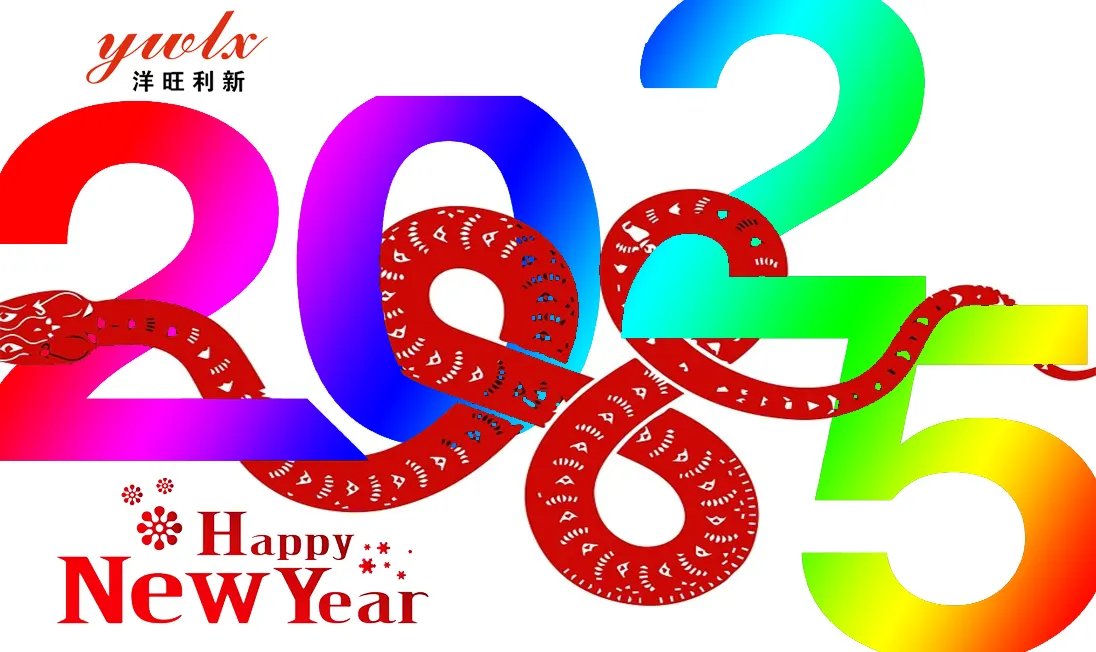
The authority of the 4 high skin pass mill within the industry is underscored by its widespread adoption across global manufacturing hubs.
Renowned manufacturers continually endorse this machinery's reliability in processing ferrous and non-ferrous metals. The mill's contribution to producing high-quality steel, aluminum, and other alloys, needed for automotive, aerospace, and construction applications, attests to its unparalleled capability. Industry certifications and endorsements further cement the authority of 4 high skin pass mills, validating their compliance with international quality and safety standards.
4 high skin pass mill
Trust in the operational efficacy of a 4 high skin pass mill is bolstered by its track record of performance and safety. Users trust these systems not only for their innovative technology but also for their robust safety mechanisms that protect both the operator and the machinery. Advanced safety features, such as emergency shut-off systems and automated monitoring, provide a secure operating environment, minimizing risks associated with high-capacity metal processing operations.
Moreover, the integration of modern technologies such as IoT-enabled sensors and AI-driven analytics into the 4 high skin pass mill has further advanced its capabilities. These innovations facilitate predictive maintenance, reducing downtime and extending the lifecycle of the machinery. By embracing such cutting-edge technologies, operators can predict wear and tear before it affects production, ensuring uninterrupted operations and fostering a trustworthy relationship with the equipment.
In summary, the 4 high skin pass mill emerges as an indispensable asset in the realm of metal processing. Its unparalleled ability to enhance product quality, coupled with its operational efficiency, sets it apart as a leading choice for manufacturers seeking excellence in metal finishing. The machine's sophisticated design and integration with modern technologies underscore its reputation for expertise, authority, and trustworthiness, making it a cornerstone in advanced manufacturing practices. Whether viewed from the perspective of an operator, engineer, or industry expert, the value of a 4 high skin pass mill is both profound and multi-dimensional, continuing to shape the future of metal processing with innovative precision.