Winding tension control is a critical aspect across various industries, from textiles to paper production, and even in electronics manufacturing. Ensuring optimal tension during the winding process prevents material damage, improves product quality, and enhances operational efficiency. In this comprehensive exploration, we delve into the intricate world of winding tension management, drawing on expert insights and proven methodologies, establishing an authoritative resource for industry professionals.
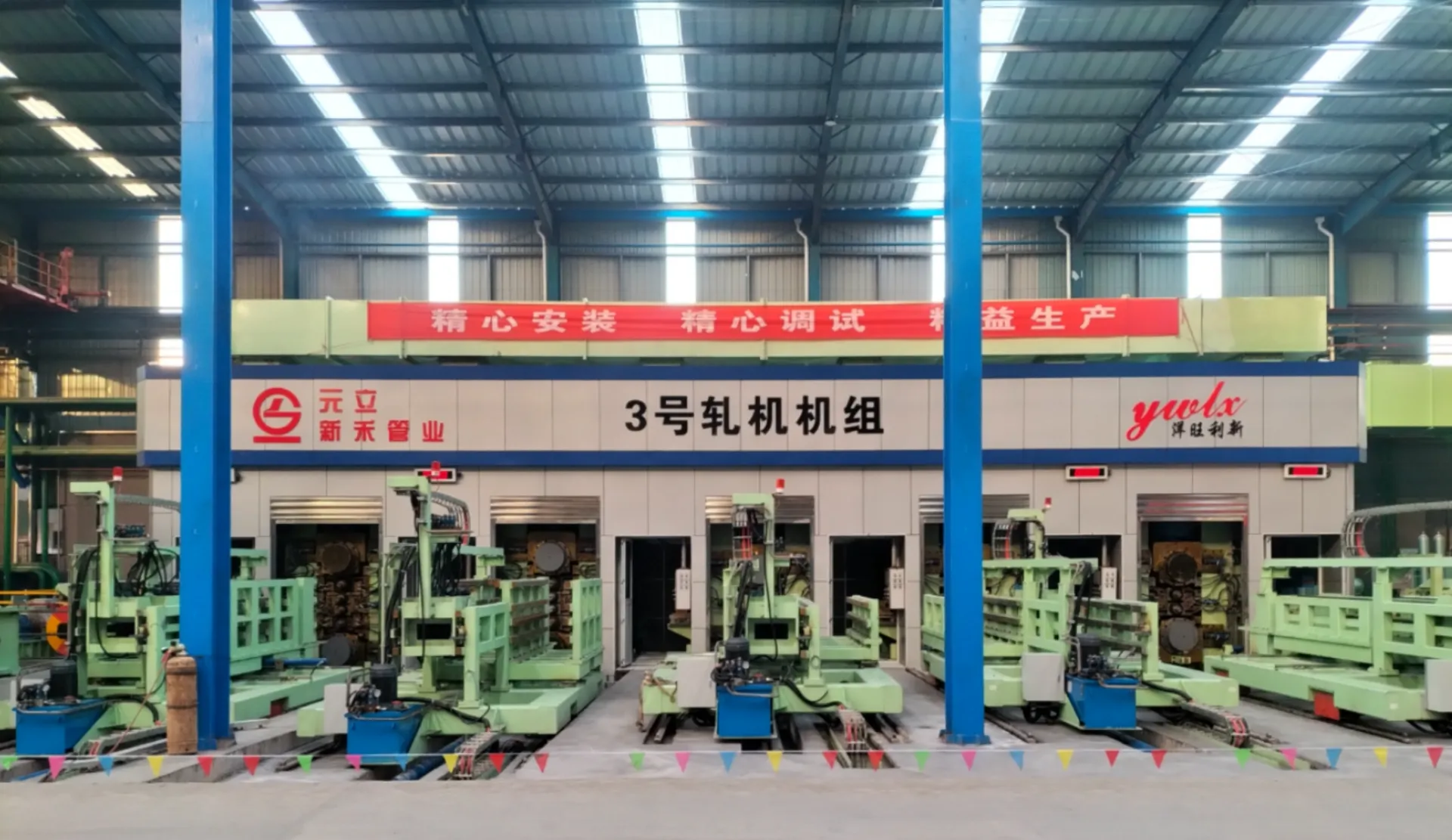
Understanding the Fundamentals of Winding Tension Control
Winding tension pertains to the force applied to a material as it is being wound onto a roll. Correct tension ensures that the material maintains its structural integrity and desired properties. When the tension is too high, materials may stretch or break, leading to costly waste and damaged inventory. Conversely, too little tension can result in loose, uneven winding, making the product unsuitable for further processing or use.
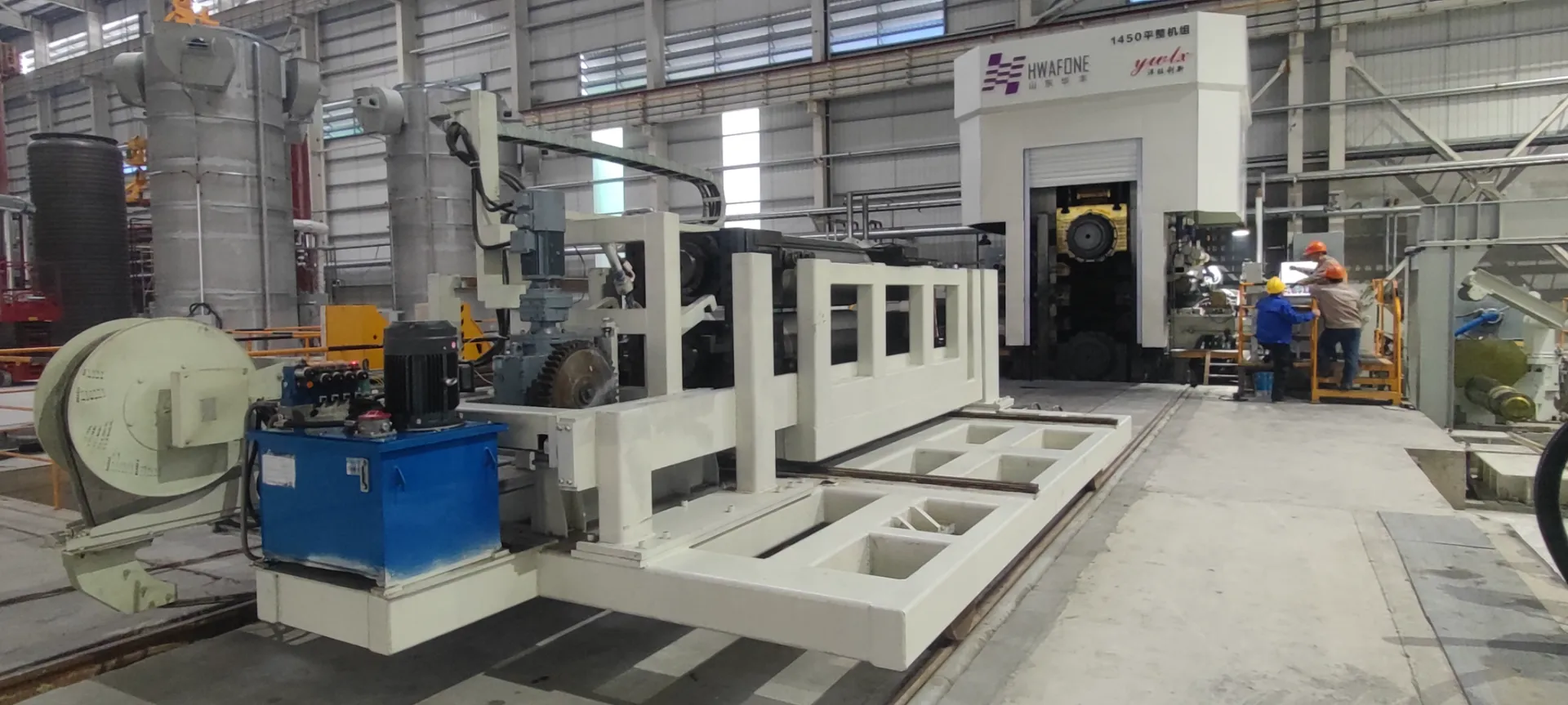
Optimizing tension involves a variety of equipment and technologies designed to measure and regulate the force exerted on the material during the winding process. Tension control systems are integral in maintaining the balance between speed and force, ensuring the end product meets quality specifications without material wastage.
The Role of Technology in Winding Tension Control
Advancements in technology have revolutionized the way tension is managed during winding operations. Innovative solutions like closed-loop control systems and load cells have brought precision and reliability into the equation. These systems continuously monitor the tension in real-time and adjust the winding parameters instantaneously to maintain the desired levels.
Load cells play a pivotal role, serving as sensors that provide feedback about the material tension. The data collected is processed by the control system, which makes automatic adjustments to the torque applied by the winding motors. Such precision minimizes human error and enhances efficiency, leading to improved product quality and reduced wastage.
Implementing Winding Tension Control A Step-by-Step Guide
For businesses aiming to implement effective winding tension control systems, understanding the material's properties is crucial. Different materials respond differently to tension; what may work for a fabric roll might be detrimental for an electric cable. Therefore, conducting material analysis is the first step in any implementation.
1. Material Analysis Evaluate the tensile strength and elasticity of the material.
Determine the optimal tension range where the material maintains its integrity.
2. System Selection Choose a tension control system suited to your operational needs. Consider factors such as the production speed, roll diameter, and material type.
3. Calibration Regularly calibrate your tension control machinery to ensure high accuracy. Calibration reduces errors and maintains system reliability over time.
winding tension management
4. Continuous Monitoring Implement systems that provide continuous feedback and automatic adjustments. Real-time monitoring systems can identify and rectify tension variations immediately, preventing defects and wastage.
5. Staff Training Skilled operators are essential for the successful implementation of tension control systems. Continuous training ensures that the staff understands system functionality and can troubleshoot basic issues effectively.
Industry Applications and Real-World Examples
The application of winding tension control is widespread and can be seen in industries like the following
- Textile Manufacturing Ensuring consistent thread tension results in high-quality fabric with uniform texture and strength.
- Metal Foil Production Accurate tension control is crucial in metal rolling processes to prevent tearing or deformation in thin foils.
- Paper and Pulp In paper manufacturing, proper tension controls help avoid tearing and uneven winding, making subsequent processing easier and more reliable.
- Film and Tape Production Films and adhesive tapes require precise tension to ensure that they can be applied evenly without air bubbles or wrinkles.
Consider a leading textile company that implemented an advanced tension control system, integrating real-time monitoring and predictive analytics. By doing so, the company noticed a significant reduction in defective rolls, a marked improvement in product quality, and substantial cost savings due to reduced wastage.
Conclusion The Future of Winding Tension Control
As industries evolve, the demand for precision and quality continues to grow. Emerging technologies like IoT and machine learning are poised to advance winding tension control systems further, making them smarter and more efficient. Machines capable of learning from past operations and predicting optimal tension settings can transform production lines, leading to even greater resource efficiency and quality assurance.
In pursuing excellence and quality through improved tension control, industries can not only enhance their product offerings but also play a role in sustainable and efficient manufacturing practices. Industry professionals, equipped with the knowledge and tools for effective tension management, are better positioned to meet today's challenges and tomorrow's opportunities.