In the realm of steel manufacturing, hot-rolled strips, known in German as warmgewalztes band, have carved their niche, widely acclaimed for their robust quality and versatile applications. The process of hot rolling involves heating steel above its recrystallization temperature and then rolling it into a strip form, which imparts unique mechanical properties ideal for numerous industrial applications. This article aims to provide a detailed exploration of hot-rolled strips, drawing on both technical expertise and practical experience to deliver an authoritative examination for industry professionals.
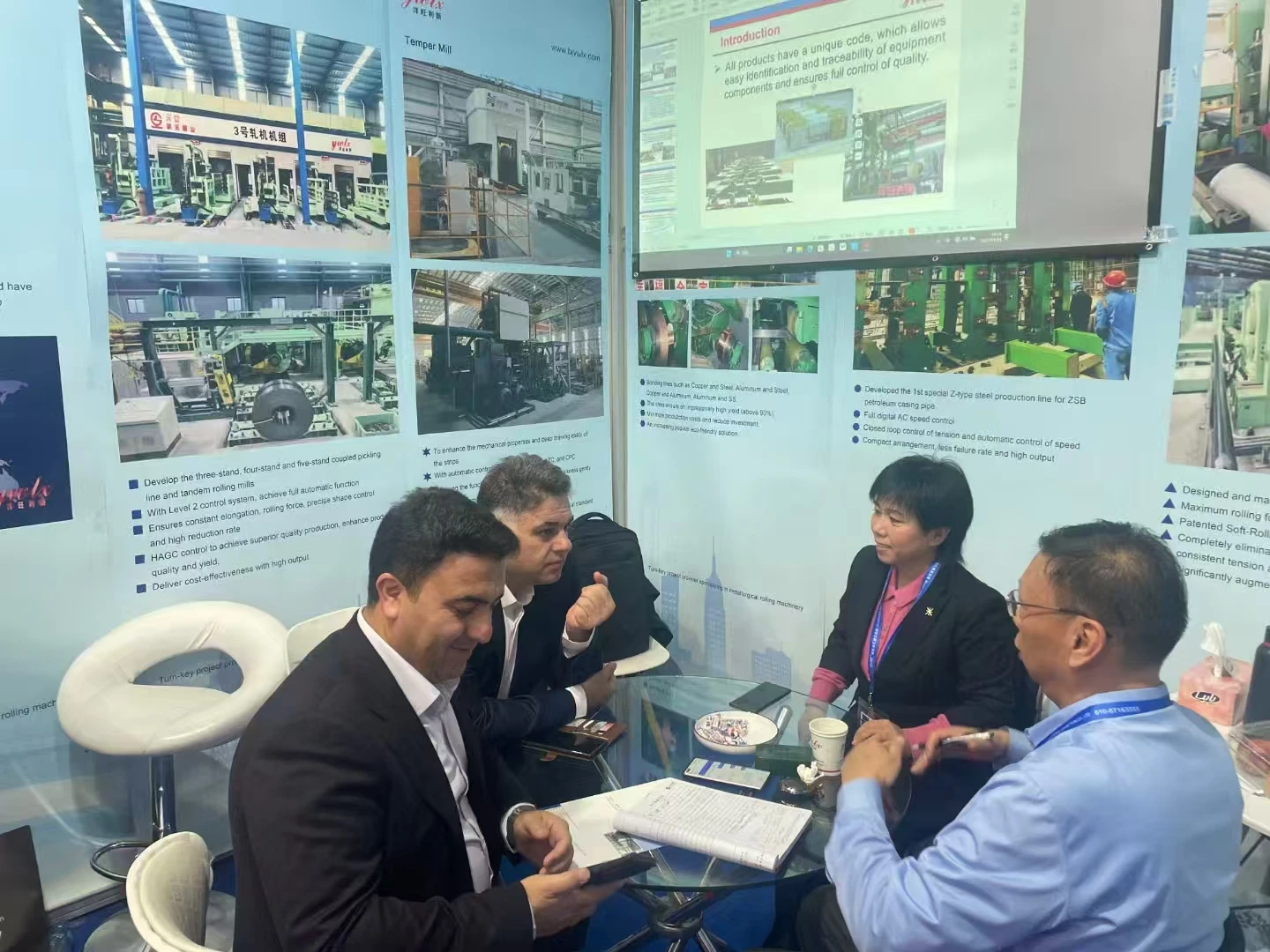
Hot-rolled strips are characterized by their distinctive finish and structural integrity. The rolling process, conducted at elevated temperatures, refines the grain structure of the metal, enhancing its ductility and toughness. This makes them especially suitable for applications that demand high strength and resilience, such as construction beams, automotive frames, and large machinery components. The surface finish of hot-rolled strips is typically scaly and slightly rough, a result of the cooling process which is performed in ambient air.
From an expert perspective, one of the significant advantages of hot-rolled strips is their cost-effectiveness. The production process is less time-consuming compared to cold rolling, without the need for reheating the steel. It allows for the manufacturing of larger sections and thicker materials, which are often required in heavy-duty applications. This contributes to reducing production costs, making hot-rolled strips a financially viable choice for projects of various scales.
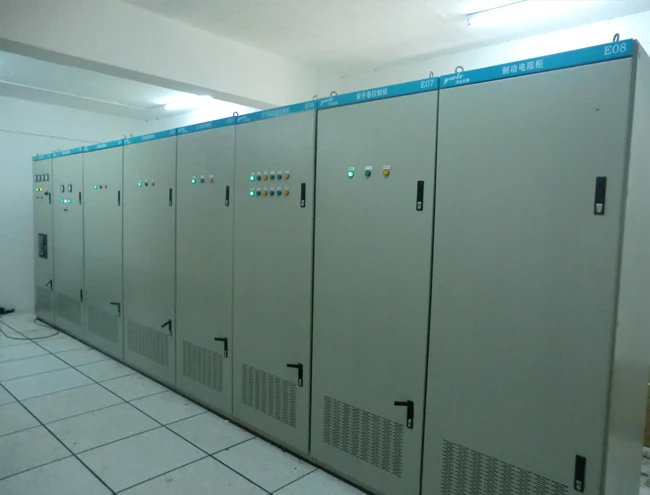
The authority of hot-rolled strips in the material science domain is reinforced by their widespread acceptance in standards developed by global regulatory bodies such as ASTM and ISO. These standards ensure that the materials meet stringent quality and safety requirements, making them reliable for long-term use in critical structures. This validation from regulatory entities enhances the trustworthiness of hot-rolled strips within the industry, ensuring that manufacturers and engineers can depend on their performance.
warmgewalztes band
Real-world experiences with hot-rolled strips also reveal a tale of versatility and adaptation. Take for instance the construction industry, where such strips are used not only for structural purposes but also in the fabrication of reinforcing bars and welded steel frames. Their ability to withstand heavy loads and resist deformation under stress is crucial in maintaining the integrity of a building over time. Similarly, in the automotive sector, the resilience of hot-rolled strips complements the dynamic forces experienced by vehicles, contributing to the overall safety and durability of cars and trucks.
In recent years, technological advancements have further cemented the position of hot-rolled strips in the market. Innovative rolling techniques have refined the grain structures even more finely, resulting in products with superior surface finishes and reduced instances of warping. This evolution has expanded the application range of hot-rolled strips, allowing them to be used in more precision-demanding environments.
In conclusion, hot-rolled strips, or warmgewalztes band, represent a key component in the steel manufacturing industry, famed for their strength, versatility, and cost-efficiency. Their production is steeped in a legacy of standardization and acceptance across various sectors, providing strong evidence of their authority and trustworthiness. The combination of theoretical expertise and empirical experience underlines the critical role that hot-rolled strips continue to play in modern industrial applications. As new technologies emerge and demand continues to evolve, further opportunities are set to arise, offering yet more avenues for this tried-and-true material to demonstrate its broad array of applications.