Ultrasonic welding rollers have revolutionized the manufacturing industry by providing a highly efficient, precise, and clean method for bonding materials. These components play a crucial role in ultrasonic welding machines, which are used widely across industries such as automotive, medical, textiles, and electronics. By understanding the intricacies of ultrasonic welding rollers, manufacturers can improve production processes, ensure product reliability, and achieve a competitive edge.
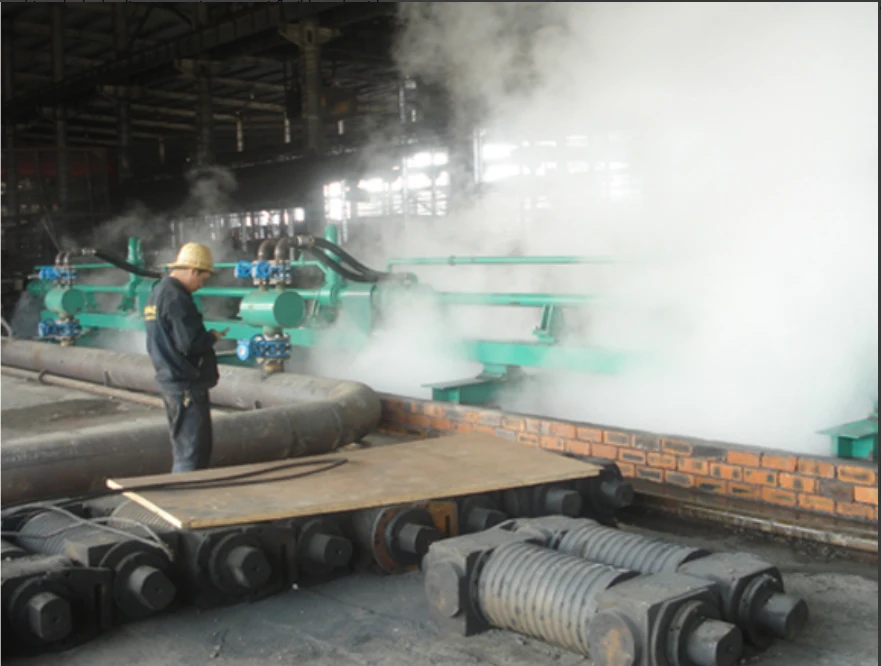
In essence, ultrasonic welding relies on high-frequency sound waves to generate frictional heat that melts and joins parts. The ultrasonic welding roller, commonly referred to as the anvil, plays a pivotal role in this process. It's typically made from hardened steel or titanium, tailored to meet specific welding requirements. This roller supports the materials being welded and helps in transmitting the ultrasonic energy efficiently.
From the perspective of expertise, the design and manufacturing of ultrasonic welding rollers demand a deep understanding of material science and acoustics. Engineers must consider factors such as material hardness, acoustic impedance, and surface finish to optimize the roller's performance. The roller's surface often features intricate patterns or knurls to enhance grip and energy transfer, ensuring uniform welds. Temperature resistance is another critical consideration, as the roller must withstand elevated temperatures without degrading.
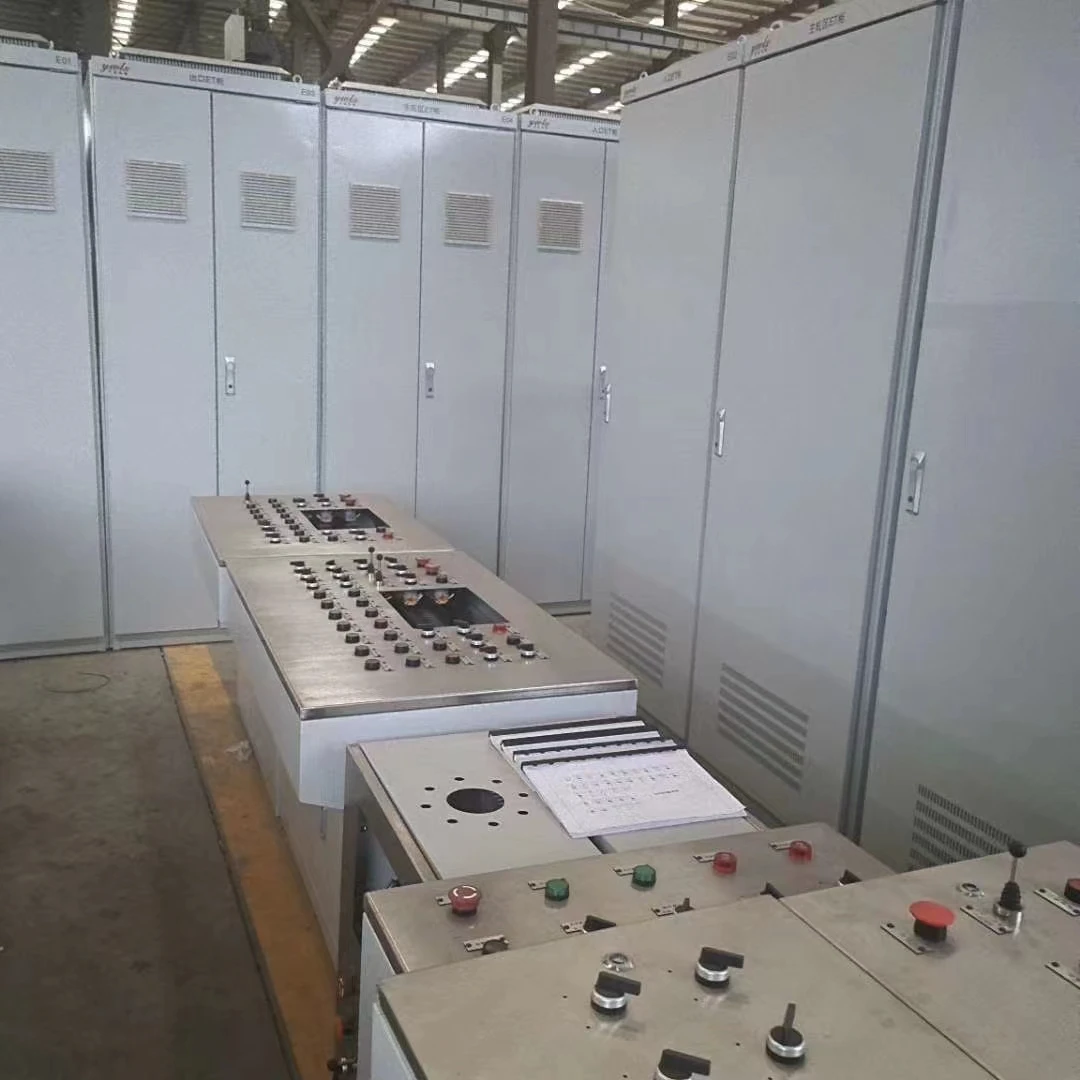
Authoritativeness is established through the rigorous testing and compliance standards that ultrasonic welding rollers must meet. Manufacturers of these rollers adhere to industry standards like ISO 19095-1 and AWS G1.6M/G1.62012, ensuring that their products perform consistently in diverse applications. Many suppliers also provide detailed documentation and lab testing results, showcasing their commitment to quality assurance.
A testament to their trustworthiness is the reliance of leading global manufacturers on ultrasonic welding rollers. Brands known for their stringent quality requirements, such as those in the medical field, where weld integrity can be life-critical, choose ultrasonic welding processes enhanced by high-quality rollers. The precision and consistency offered by these components contribute significantly to the credibility of ultrasonic welding solutions.
ultrasonic welding roller
Real-world experience speaks volumes about the efficacy of ultrasonic welding rollers. Consider the technological advancements in the automotive industry. Here, ultrasonic welding is employed in creating wire harnesses, assembling interior trim components, and producing lithium-ion battery packs. The reliability of welding in these applications is critical, as failures could lead to costly recalls or jeopardize passenger safety. Ultrasonic welding rollers ensure that each weld is consistent, robust, and meets the highest standards of durability.
In the textile industry, the demand for seamless finishes and non-invasive bonding techniques make ultrasonic welding rollers indispensable. These rollers enable the joining of synthetic fabrics without needles or threads, minimizing perforation and maintaining fabric integrity—an essential requirement in sportswear and smart textiles.
For electronic assemblies, where precision is paramount, ultrasonic welding rollers offer the capability to establish secure connections without introducing contaminants like solder or adhesives. Given the miniaturization trend in electronics, achieving reliable connections using traditional methods is challenging.
Ultrasonic welding provides a clean, repeatable, and efficient alternative.
In terms of product innovation, recent advancements have led to the development of custom ultrasonic welding rollers that cater to specialized needs. For instance, rollers with interchangeable anvils or those designed for specific patterns can tailor weld attributes to unique applications. This level of customization is instrumental for industries with specific welding challenges and enhances overall equipment flexibility.
In conclusion, the role of ultrasonic welding rollers cannot be understated. They are foundational to the ultrasonic welding process, transforming it into an indispensable manufacturing technique. By combining knowledge, authority, and innovation, manufacturers of ultrasonic welding rollers provide reliable solutions that meet and often exceed industry expectations. Their continued evolution underscores a commitment to enhancing productivity, ensuring product quality, and ultimately advancing industrial capabilities across multiple sectors.