The realm of TMT mills, crucial in the steel manufacturing industry, plays a pivotal role in determining the quality and durability of construction materials. Given their importance, understanding the nuances of TMT mill operations can greatly benefit companies aspiring to lead in this competitive market.
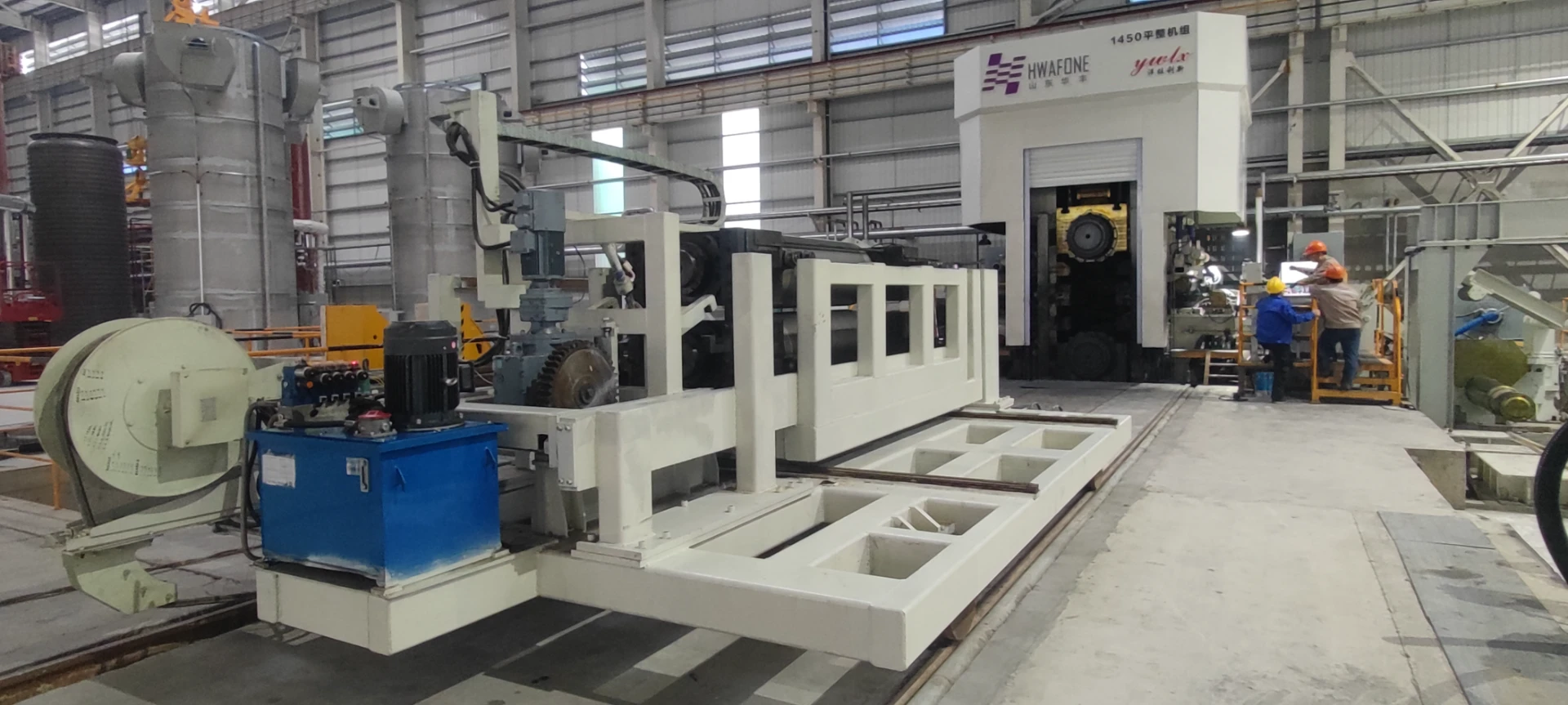
TMT, standing for Thermo-Mechanically Treated, refers to steel bars that undergo a unique manufacturing process. This process enhances their strength, flexibility, and corrosion resistance, making them ideal for construction purposes. The journey of raw steel into robust TMT bars involves heating the material above recrystallization temperature followed by vigorous quenching and subsequent tempering. It is this intricate procedure that equips TMT bars with their defining characteristics—high tensile strength paired with superior ductility.
A comprehensive immersion into TMT mill operations reveals several key components that underscore their efficiency and reliability.
Central to this are the induction furnaces and rolling mills, which play a decisive role in shaping the material. Specialists in the field recognize the significance of precision and synchronization in controlling the speed and temperature within these systems. Slight deviations can not only affect the quality but can also lead to considerable resource wastage.
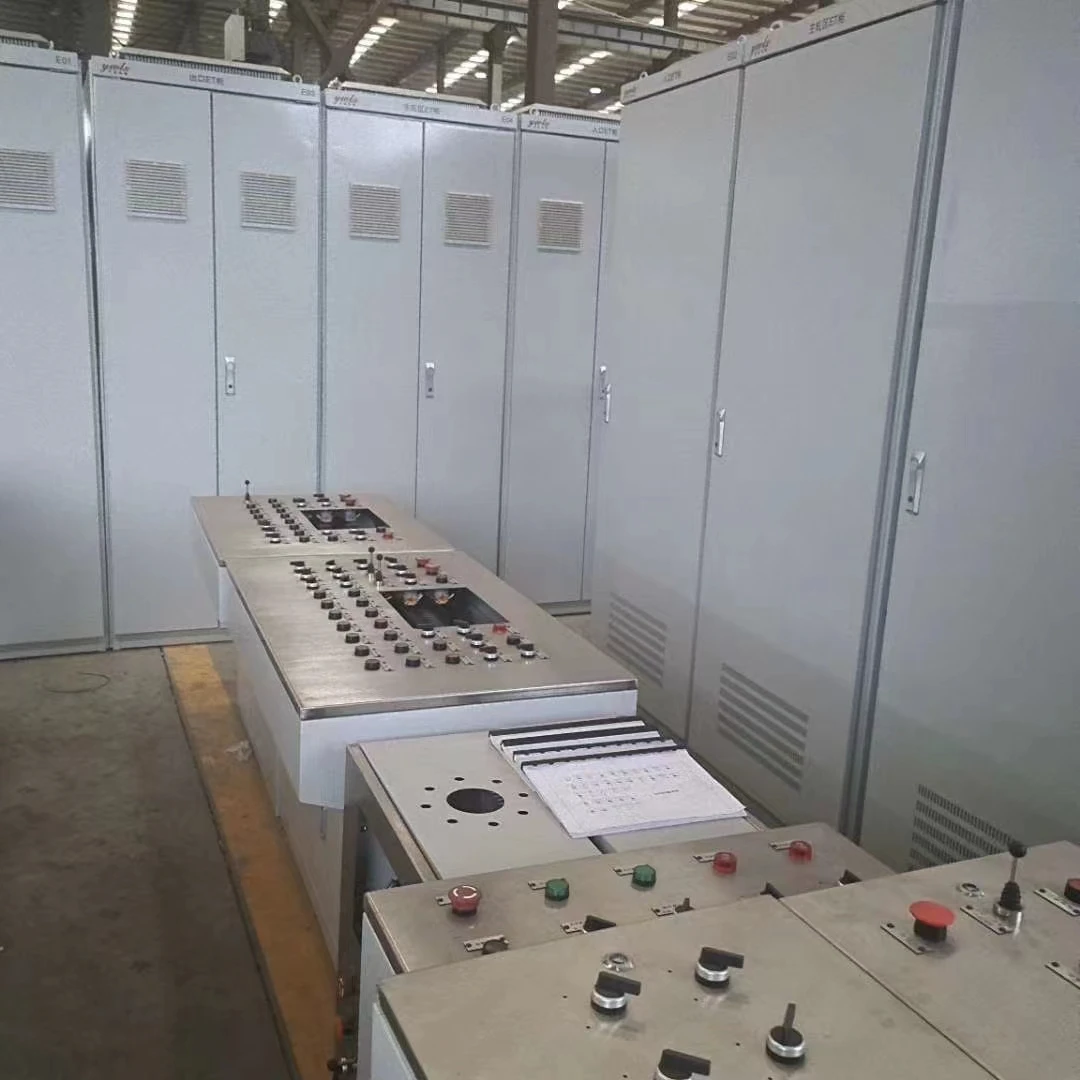
Incorporating advanced technologies like automation and artificial intelligence into TMT mills can significantly optimize production workflows. Automated systems enhance precision while reducing human error, thereby elevating product quality and consistency. Moreover, AI-driven predictive maintenance has gained traction in recent years, allowing for real-time monitoring and early detection of anomalies, thus minimizing downtime and extending equipment lifespan.
tmt mill
Expertise in managing a TMT mill also involves a profound understanding of the metallurgical principles that govern the treatment process. A balanced approach to combining temperature control with mechanical stress application results in a microstructure that endows TMT bars with their necessary mechanical properties. Professionals in this sector must keep abreast of technological advancements and evolving industry standards to sustain a competitive edge. Continuous professional development through workshops and certifications is pivotal in honing such expertise.
Authoritativeness within the TMT mill sector can be achieved by maintaining strict adherence to international quality standards such as ISO 9001. Companies that prioritize rigorous quality checks at every stage—from raw material inspection to final product testing—are more likely to earn the trust of stakeholders and consumers alike. Establishing alliances with recognized certifying bodies further reinforces a company's position as a market leader.
For any individual or organization venturing into the realm of TMT mill production, trustworthiness is the pillar that can support sustained success. Transparency in operations, ethically sourced materials, and an unwavering commitment to safety protocols cultivate a dependable brand image. Engaging with clients and stakeholders through regular updates on processes, innovations, and best practices can fortify trust and foster long-term relationships.
In summary, a deep dive into the intricacies of TMT mill operations reveals a sophisticated interplay of technology, expertise, and quality assurance practices. By embracing technological advancements, continually developing professional expertise, adhering to authoritative standards, and building trust through transparent operations, entities can excel in the dynamic and demanding field of TMT mill production.