The world of titanium rolling mills is a complex and crucial part of the manufacturing process involving titanium products. As a fundamental phase in the production of titanium sheets and coils, the rolling mills play a vital role in not only shaping these materials but also in enhancing their mechanical properties. Understanding this process is essential for industries that rely heavily on titanium's unique attributes. Herein lies the expertise drawn from a plethora of real-world experiences.
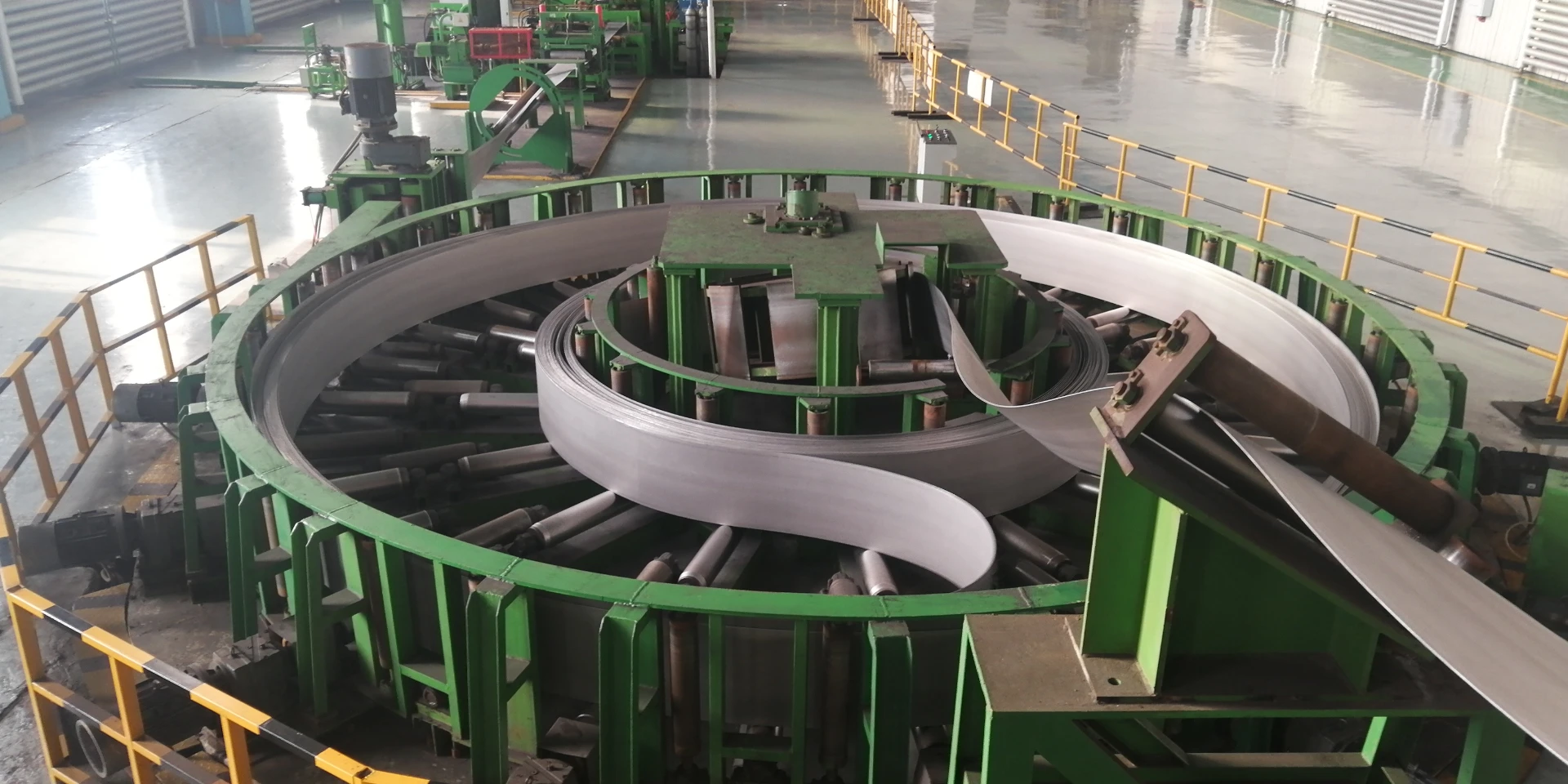
To begin with, the titanium rolling mill process is hinged on precision engineering. The astounding properties of titanium, including its high strength-to-weight ratio and exceptional corrosion resistance, make it an invaluable resource across industries ranging from aerospace to biomedical engineering. However,
these same properties present a unique challenge in its processing. Specifically, titanium’s poor thermal conductivity and high reactivity at elevated temperatures demand specific expertise in handling during rolling.
During the rolling process, titanium ingots are first heated to a specific temperature that ensures malleability without compromising the material’s integrity. Expert mill operators maintain stringent control over this temperature to avoid drawbacks such as excessive grain growth, which can detrimentally affect the mechanical properties of the final product. Precision instruments and advanced software systems are employed to monitor and adjust the temperatures and speeds automatically, ensuring a high degree of accuracy.
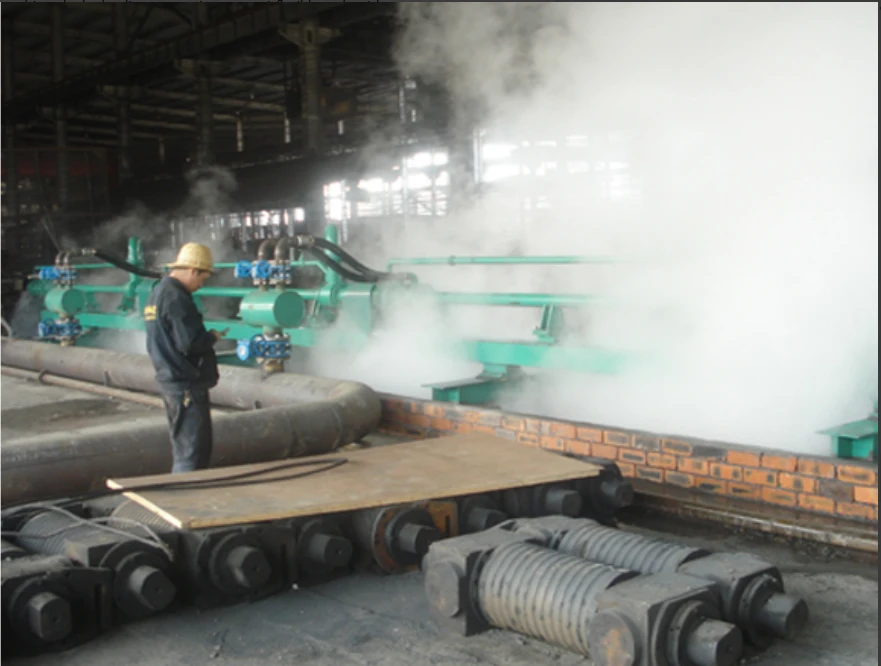
Authoritativeness in titanium rolling mills is characterized by understanding the nuances of rolling schedules, which are meticulously planned sequences that determine the thickness and flatness of the produced titanium sheets. Conducting real-time inspections of sheet dimensions allows for the adjustments that ensure the end products meet the specific requirements of each client. Such measures are indispensable given that the applications of titanium often involve critical environments where failure is not an option.
titanium rolling mill
Trustworthiness in this industry comes from continuous innovation and adherence to international standards. Quality control protocols are non-negotiable and involve comprehensive testing for material defects, including non-destructive and destructive testing methods. Companies operating within this domain often boast certifications such as ISO 9001, ensuring that their products consistently meet customer and regulatory requirements.
Experience shared from industry insiders underscores the benefits of investing in state-of-the-art rolling equipment. Not only do these machines improve efficiency and reduce waste, but they also provide enhanced control over the final product's quality. The precision afforded by modern rolling mills reduces the variability in product dimensions and surface qualities, which is paramount for maintaining competitiveness in high-stakes markets.
Furthermore, integrating a sustainable approach in titanium rolling mill operations is becoming increasingly significant. Leveraging technology to minimize energy consumption and reduce carbon emissions is not just environmentally responsible; it enhances the company's image as a forward-thinking, trustworthy entity. Recycling titanium scraps and optimizing resource allocation within the rolling mill can further bolster economic and environmental sustainability.
In summation, the expertise entrenched within titanium rolling mills reflects a blend of advanced technological prowess and meticulous attention to detail. By capitalizing on real-world experience, manufacturers not only assert their authority within the market but also ensure the production of titanium products that uphold the highest standards of reliability and performance. As industries continue to evolve, the emphasis on expertise, authority, and trust in titanium rolling processes remains more critical than ever.