In the dynamic world of metallurgy and manufacturing, the role of rolling mills, or tipi di laminatoi, is crucial. These machines not only form the backbone of metal processing industries but also serve as a cornerstone for product development, quality assurance, and cost efficiency. Different types of rolling mills are used throughout various industry sectors, each designed to meet specific product requirements and operational demands.
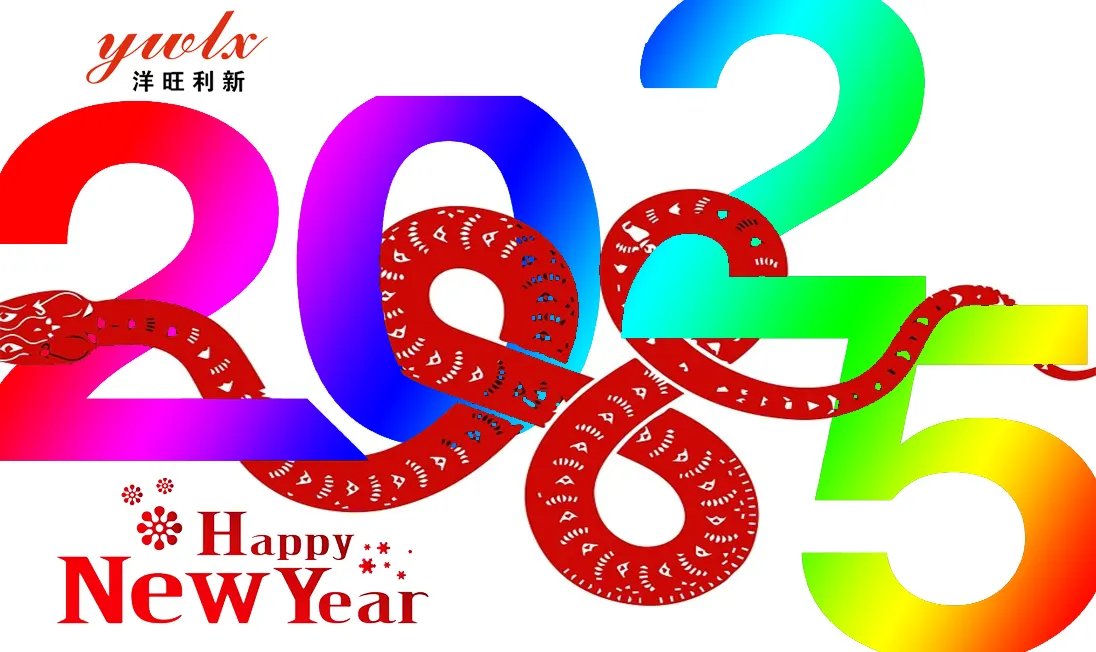
Understanding the nuances of these different rolling mills can significantly impact product quality and operational efficiency. The primary types include two-high rolling mills, three-high rolling mills, four-high rolling mills, cluster mills, and tandem rolling mills. Each type has distinct characteristics, advantages, and applications, making the selection process a critical decision for manufacturers aiming for precision and reliability.
Two-high rolling mills are among the simplest and most widely used types due to their affordability and adaptability in various scenarios.
They consist of two rolls rotating in opposite directions, which is ideal for basic material processing tasks. These machines are perfect for small-scale production or for materials that do not require intricate processing, providing an optimal balance between cost-effectiveness and performance.
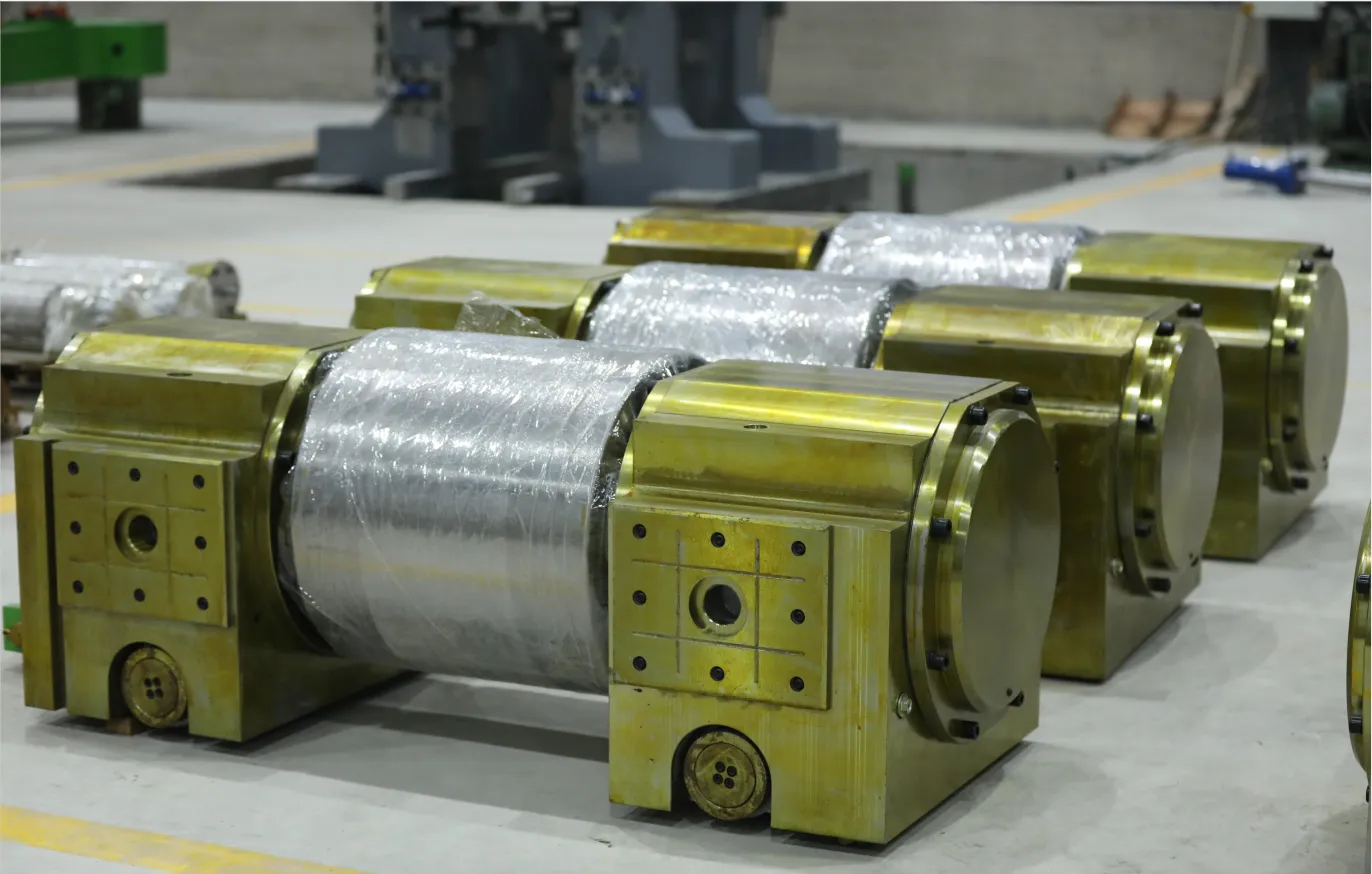
Three-high rolling mills introduce an additional level of control and flexibility by incorporating a third roll. This configuration allows for a single-pass rolling mechanism that doesn't require the reversal of direction, streamlining the process and improving production speed. These mills are essential in medium to large-scale production environments where time efficiency is crucial, without compromising on the quality of the output.
Four-high rolling mills take the concept of precision a step further. By using two smaller rolls supported by two larger backup rolls, these machines provide increased strength and minimize flexing. This results in superior surface finishes and tighter dimensional tolerances, making them ideal for high-grade materials required in industries like aviation and automotive manufacturing. The four-high setup is preferred when dealing with with very thin sheets or when superior surface finishes are necessary, substantiating its importance in precision-dependent sectors.
tipi di laminatoi
Cluster mills, also known as Sendzimir mills or Z-mills, use multiple smaller rolls for complex precision tasks. This design provides increased control over the rolling process, allowing for the production of ultra-thin materials like foils and specialty metals. These mills excel in highly specialized fields where intricate detail and unyielding consistency are demanded. Cluster mills often find their place in niche applications, such as electronics and microfabrication, where even the smallest imperfections can have significant consequences.
Tandem rolling mills, on the other hand, emphasize volume and productivity. They consist of a sequence of rolling stands, where metal is rolled in a continuous process without the need for repetitive re-feeding. This setup enables mass production of metal sheets with consistent quality, crucial for industries such as construction and infrastructure development. The efficiency and large-scale capabilities of tandem mills cater directly to industries with high demand for rolled metal products, such as steel packaging and automobile manufacturing.
Investing in the correct type of rolling mill extends beyond immediate operational benefits to influence market competitiveness and long-term profitability. Reliable manufacturers and suppliers build their expert reputation on the quality of metal products, which are fundamentally shaped during the rolling process. Selecting the appropriate machinery not only ensures production meets required standards but also enhances a manufacturer's ability to innovate and meet evolving customer demands.
Moreover, acquiring a rolling mill involves considering factors like installation space, energy consumption, maintenance needs, and integration with existing systems. Manufacturers must weigh these variables alongside the mechanical capabilities of each mill type. Collaborating with experts and consulting industry-specific trends can provide valuable insights into which rolling mill will best align with intended production goals and operational circumstances.
In conclusion, the strategic selection and utilization of different types of rolling mills are instrumental in achieving operational excellence and maintaining a competitive edge in the metallurgical and manufacturing industries. Understanding each type’s unique features and capabilities allows manufacturers to tailor their production processes, thereby ensuring quality, boosting productivity, and driving innovation in metalworking. Prioritizing the right rolling mill is pivotal not only for meeting current production demands but also for positioning for future growth and technological advancement.