Navigating the steel bar mill industry requires a nuanced understanding of the processes, technological advancements, and market dynamics that shape it. This experience-driven exploration delves into the core elements that define optimal operations in a steel bar mill, ensuring not only superior product quality but also enhancing efficiency and sustainability.
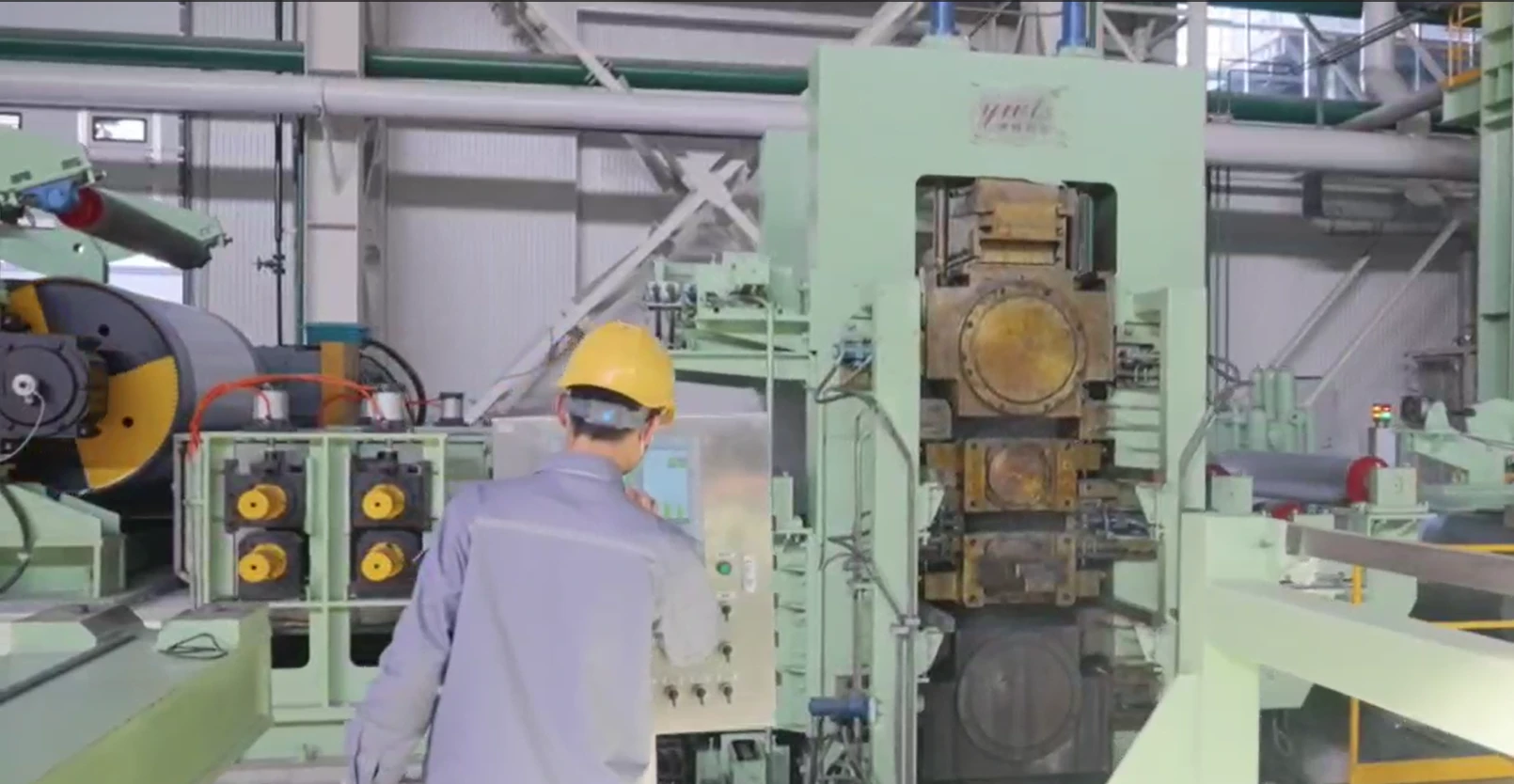
In the contemporary steel production landscape, the role of a steel bar mill is pivotal. These mills are engineered to produce long steel bars with precise dimensions and properties tailored for construction, infrastructure, and industrial applications. At the heart of any advanced steel bar mill is cutting-edge technology that ensures precision and consistency in every batch. Understanding the operational nuances, from steelmaking to pouring, rolling, and cooling, forms the bedrock of expertise in this field.
The journey through a steel bar mill begins with raw materials, predominantly iron ore or scrap, which undergo melting in an electric arc furnace or a basic oxygen furnace. This process, managed by seasoned metallurgists, requires careful monitoring to maintain the desired chemical composition of the steel. Expertise in controlling parameters like temperature, carbon content, and alloying elements is crucial here, directly impacting the mechanical properties and performance of the final steel bar.
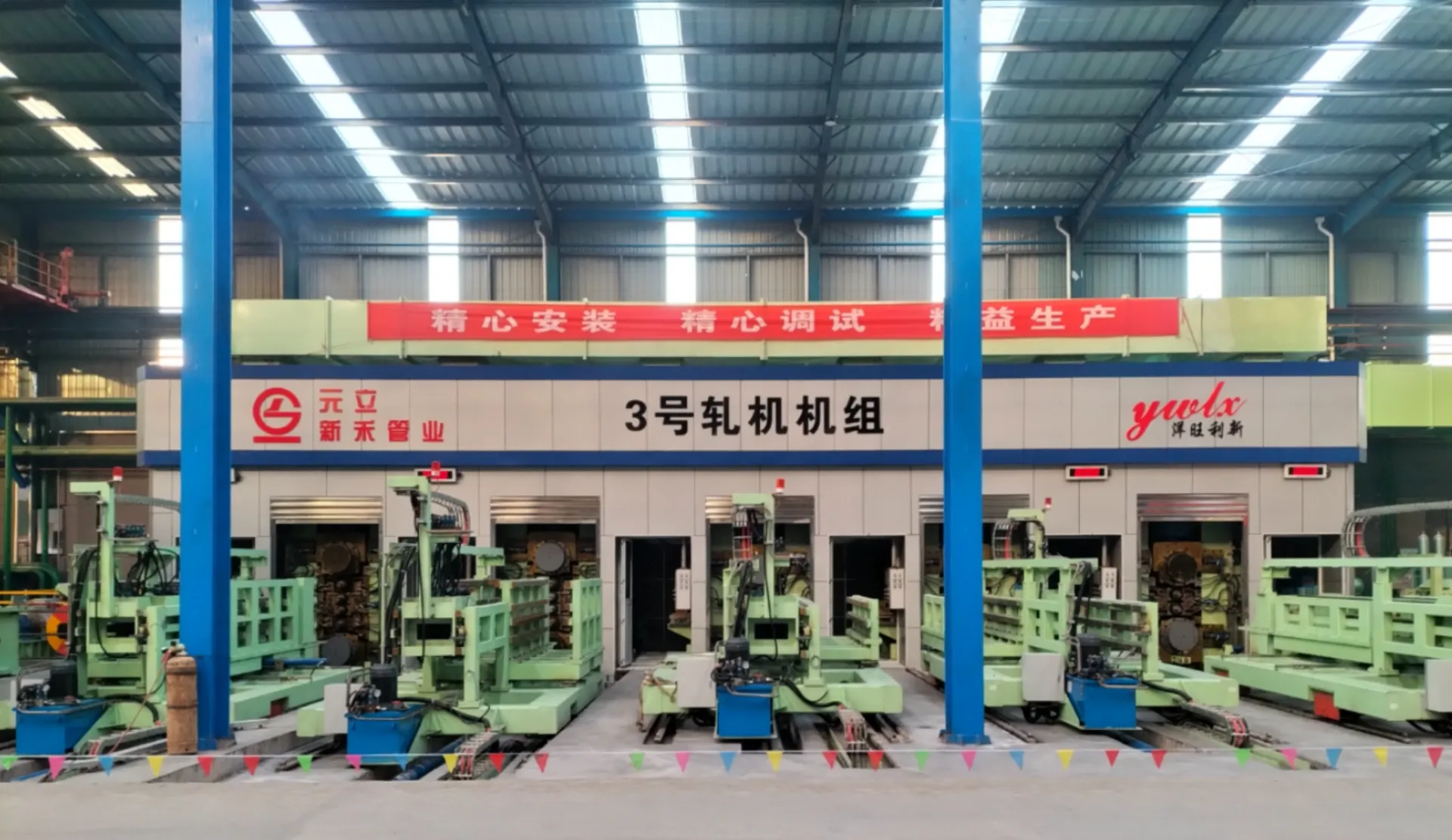
Rolling,
the stage where steel ingots are transformed into bars, involves a series of mechanical processes. The mastery lies in the precise calibration of rolling mills, where the temperature and speed are meticulously controlled to achieve the desired bar thickness and surface finish. Advanced automation and AI-driven controls have redefined this stage, minimizing human error and enhancing the reliability of operations.
Authoritativeness in the steel bar mill sector is further bolstered by adherence to stringent quality standards and certifications. Industry-leading mills are committed to ISO, ASTM, and EN standards, which govern everything from internal processes to external audits. This commitment assures clients that every steel bar produced meets rigorous international benchmarks for strength, ductility, and durability.
steel bar mill
Trust in steel bar mills is also rooted in sustainable practices. Forward-thinking mills are investing in eco-friendly technologies that reduce emissions and energy consumption. The integration of recycled materials, waste heat recovery systems, and water recycling technologies not only conserves resources but also positions these mills as responsible industry players keen on minimizing their environmental footprint.
For buyers and engineers, understanding the supply chain dynamics and logistical prowess of a steel bar mill is crucial. The reliability of delivery schedules, consistency in supply, and capacity to customize orders are decisive factors that influence purchasing decisions. Trustworthy mills maintain transparent operations, offering real-time tracking systems and customer service layers that facilitate seamless communication and support.
The steel bar mill landscape is continuously evolving, driven by innovations in material science, automation, and sustainability practices. Staying at the forefront of these developments requires a dynamic combination of experience, deep industry knowledge, and a commitment to continuous improvement.
In conclusion, the excellence of a steel bar mill is defined not only by its product output but also by its dedication to refining processes, embracing technology, and upholding quality and sustainability standards. Whether one is a seasoned industry professional or new entrant, understanding and leveraging these core dimensions will significantly enhance operational effectiveness and market competitiveness in the steel bar industry.