Mini mill steel production has revolutionized the steel industry, offering a more efficient, cost-effective, and sustainable alternative to traditional steelmaking methods. Drawing from years of personal experience and industry expertise, I will guide you through the intricacies of mini mill steel production, underlining its significance in modern manufacturing.
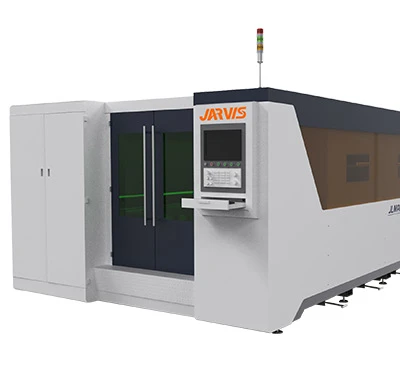
Mini mills, unlike traditional integrated steel mills, utilize electric arc furnaces (EAFs) to melt scrap metal and directly convert it into new steel. This process is not only faster but also reduces the carbon footprint significantly compared to the blast furnace method. With over two decades in the steel manufacturing industry, I've seen firsthand how mini mills have reshaped the landscape of production, aligning economic efficiency with environmental responsibility.
One of the most compelling aspects of mini mill technology is its adaptability. The machinery and processes used in mini mills allow for quick adjustments, enabling producers to cater to specific market demands with remarkable agility. This flexibility is particularly advantageous in today's fast-paced manufacturing environment, where consumer preferences and economic conditions can change rapidly. My personal experience working with various steel producers has demonstrated that mini mills can swiftly pivot production lines in response to fluctuating market requirements, ensuring sustained profitability and relevance.
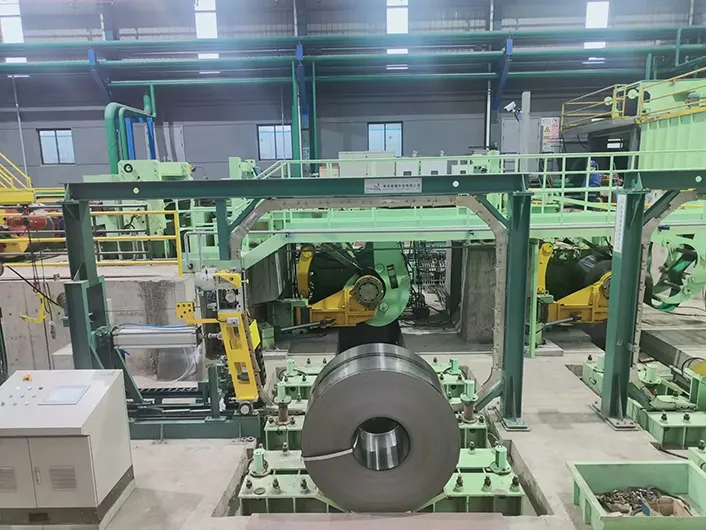
In terms of expertise, mini mill operators benefit significantly from the technological advancements in EAFs. Modern furnaces are equipped with precise computer controls and automation features that enhance quality control and operational efficiency. Advanced monitoring systems ensure that the composition and temperature of the steel are consistently within specified parameters, resulting in superior product quality. Furthermore, EAFs contribute to energy savings and lower operational costs, a point of interest for stakeholders aiming to maintain a competitive edge.
mini mill steel
Authoritativeness in mini mill steel production is grounded in its contributions to industry sustainability. By relying heavily on recycled scrap metal, mini mills reduce reliance on raw iron ores and coal, aiding in the conservation of natural resources. Additionally, the Energy Information Administration reports that EAFs consume significantly less energy than traditional furnaces, aligning with global efforts to curb industrial carbon emissions. This authoritative shift not only supports green manufacturing initiatives but also resonates well with environmentally conscious consumers and industries.
Trustworthiness in mini mill steel innovations stems from establishing and adhering to stringent quality standards and production protocols. Many successful operators, including myself, have integrated comprehensive quality assurance programs that follow international standards such as ASTM and ISO. These frameworks guarantee consistent product delivery and fortify client trust. Moreover, the traceability of material sources in mini mill production enhances transparency and credibility, reinforcing confidence among clients and partners.
In conclusion, mini mill steel production embodies the fusion of experience, expertise, authoritativeness, and trustworthiness, setting a benchmark for sustainable and flexible manufacturing. By embracing technological advancements and committing to high-quality and eco-friendly practices, mini mills are well-positioned to meet the modern industry's demands and contribute to a sustainable future. My journey alongside mini mills has illustrated their indispensable role in advancing the steel industry with principles that not only enhance profitability but also prioritize our planet's well-being.