Navigating the complex world of steel manufacturing, especially within the confines of a steel rolling plant, requires a deep understanding of not only the industrial processes but also the intricate balance of materials science, production efficiency, and market demands. As a pivotal link in the metallurgical industry, a steel rolling plant transforms raw steel into sheets, bars, beams, and other essential forms, each demanding precision and expertise.
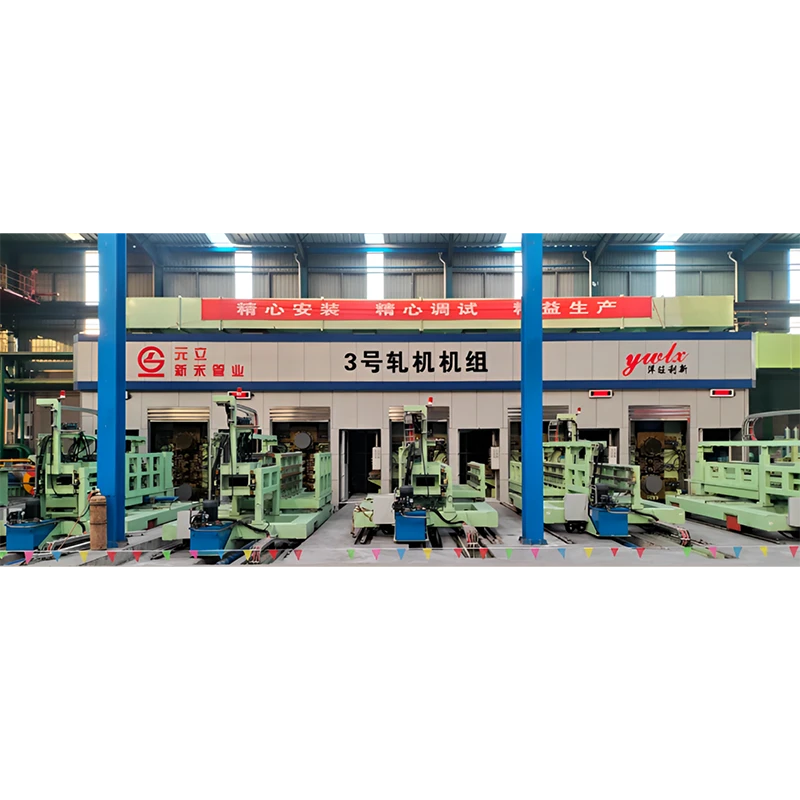
A typical steel rolling plant operates with meticulous attention to detail, utilizing advanced technology and skilled labor to maintain consistent quality. The rolling process involves passing steel slabs, billets, or blooms through a series of rolls to reduce thickness, enhance strength, and tailor the material's physical properties to meet specific requirements. Engineers play a key role, applying their expertise to adjust roll pressures, temperatures, and speeds to optimize outcomes.
The success of a steel rolling plant heavily relies on the condition and performance of its machinery. Regular maintenance and calibration of rolling mills are crucial. These intricate machines, often housing pairs of rolls that apply pressure to steel, must function flawlessly to avoid defects. Faults in the machinery can lead to uneven surfaces and compromise the structural integrity of the steel. Therefore, continuous training and qualification of plant operators ensure that they possess the necessary skills to foresee and mitigate potential disruptions.

Innovation in a steel rolling plant is a game-changer. Recent advancements have integrated Industry 4.0 technologies such as IoT devices and AI-driven analytics to enhance monitoring and predictive maintenance. These technologies facilitate real-time data collection, enabling more precise adjustments to the rolling process and predicting possible machinery failures before they occur, ultimately saving time and resources.
steel rolling plant
An essential aspect of steel rolling is its environmental impact. As demand for steel continues to grow, plants are under increasing pressure to minimize their carbon footprint. Modern plants now incorporate energy-efficient technologies, recycling waste heat, and adhering to stricter emissions guidelines. This pivot not only aligns with global sustainability initiatives but also reduces operational costs, a significant consideration for any competitive plant.
The materials entering a steel rolling plant are as important as the processes involved. High-quality raw materials lead to superior finished products. Suppliers are routinely vetted, and their materials tested to ensure consistency in chemistry and physical properties. This level of scrutiny establishes credibility and trustworthiness in the final product, making them suitable for critical applications in construction, automotive, and a myriad of other industries.
Understanding market dynamics is also crucial for a steel rolling plant's strategic planning. Global steel demand is subject to fluctuation based on economic cycles, trade policies, and technological advancements in alternative materials. A well-positioned plant agilely adapts to these changes by diversifying its product range and optimizing cost efficiencies.
In conclusion, a steel rolling plant is a testament to industrial prowess, requiring a blend of experience and technical expertise to operate effectively. The success of such facilities lies in their ability to innovate, maintain robust supply chains, and adapt to market demands while striving for sustainability. These elements together forge steel that is not only durable and reliable but also produced in an ethically and environmentally conscious manner.