Skin pass steel, often regarded as the final phase in the steel production process, is renowned for its pivotal role in improving the surface texture and mechanical properties of steel products. This treatment, which involves the light cold rolling of steel, is crucial for achieving a high-quality finish essential for various industrial applications. With skin passing, the steel surface becomes smoother, more uniform, and more aesthetically appealing, enhancing its applicability in diverse sectors such as automotive, construction, and household appliances.
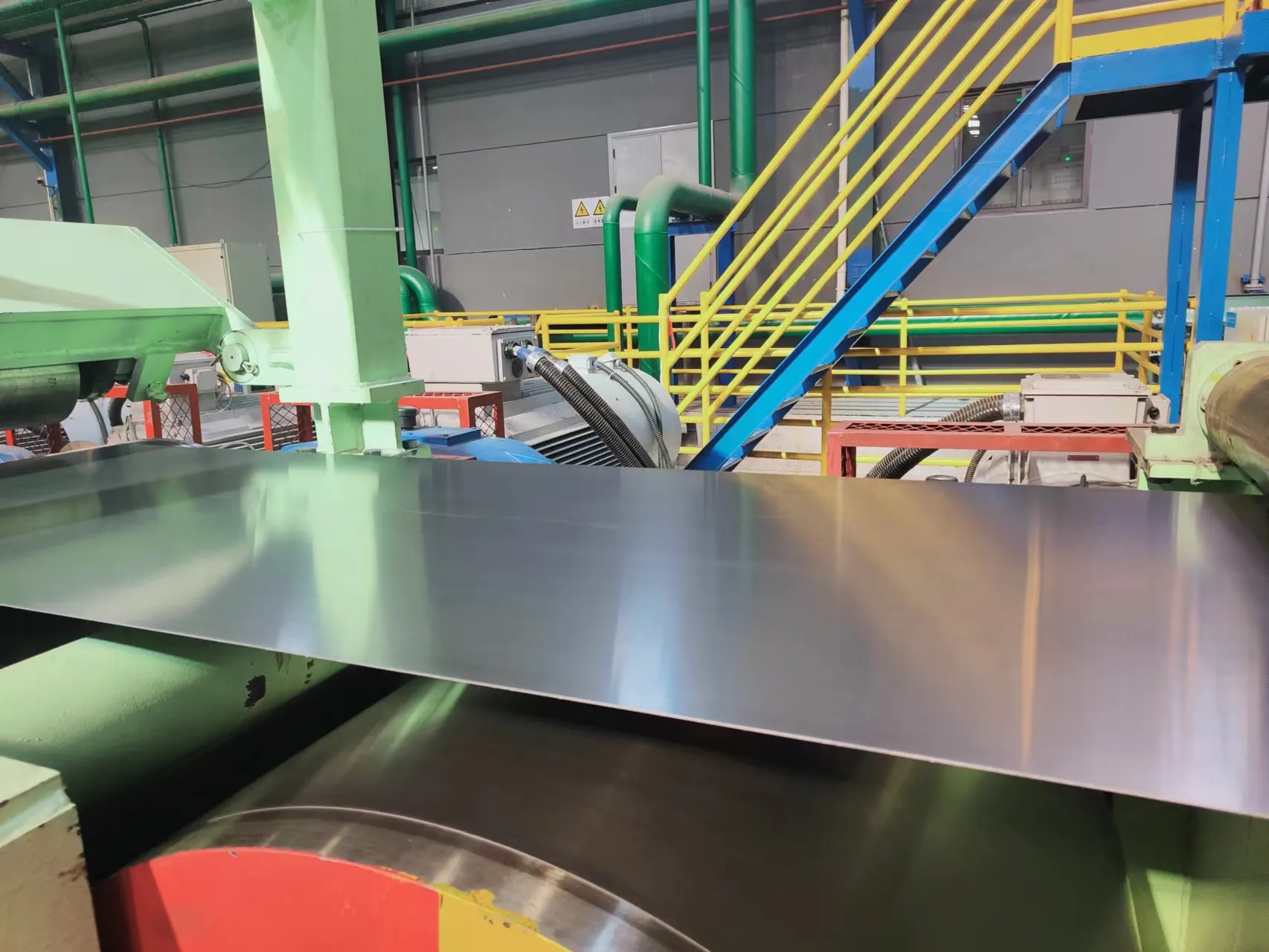
In the realm of experience, it's evident that the optimal application of skin pass steel depends heavily on the intended use of the final product. Manufacturers with years of expertise in handling steel understand that the surface quality achieved through skin pass can significantly affect the product's performance and appearance. For instance, in the automotive industry, where visual and structural integrity is paramount, skin-passed steel ensures superior paint adhesion and a defect-free finish, leading to better corrosion resistance and elongating the lifespan of vehicle components.
From an expertise standpoint, the intricacies involved in the skin pass process demand a comprehensive understanding of metallurgical principles. The degree of reduction in thickness during the skin pass process is a critical parameter, typically limited to about 1-3% of the product's original thickness. This precise reduction is expertly calibrated to enhance the steel's yield strength and eliminate yield point elongation, while avoiding any compromise on ductility. Such strategic processing ensures the balance between toughness and formability, crucial for products that require intricate shaping or bending.
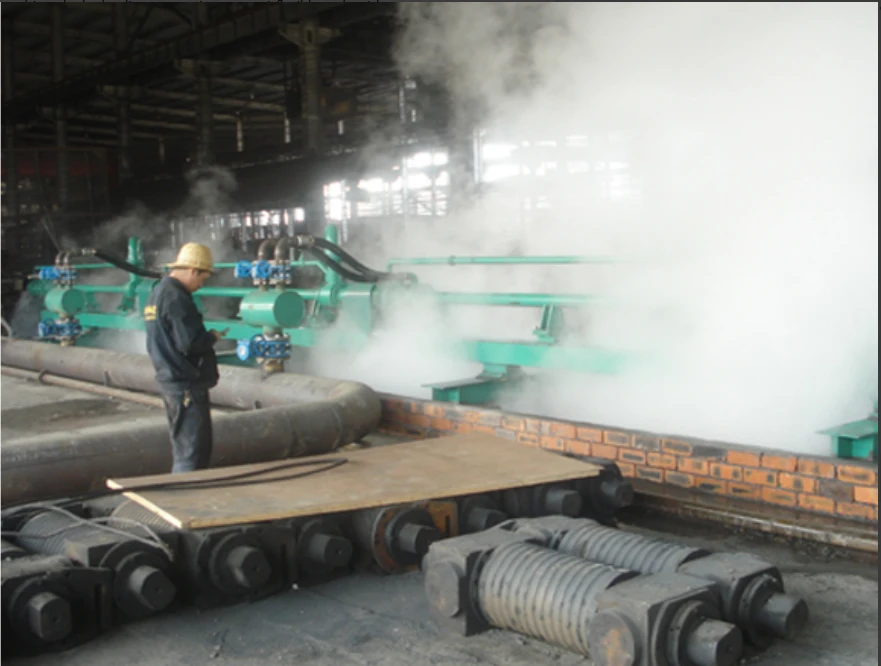
Authoritativeness in the context of skin pass steel production cannot be overstated. The process is not merely about achieving a smooth surface; it's about the precise application of pressure, temperature control, and synchronizing with other steel treatment phases to realize the desired mechanical properties. Recognized authorities in steel manufacturing emphasize the importance of high-quality rolling mills and sophisticated control systems in the skin pass process. The application of these advanced technologies translates to more uniform coil properties, minimized risk of surface defects, and enhanced product consistency across large batches.
skin pass steel
Trustworthiness is deeply embedded in the skin pass steel domain, particularly concerning quality control. Leading manufacturers adhere to stringent quality management protocols to ensure that each coil meets the precise specifications and standards required by their clients. Reliable certifications, such as ISO standards, underscore a manufacturer's commitment to quality and safety, assuring customers that their steel products are of unparalleled quality and reliability. Trust in a manufacturer's capability to deliver skin-passed steel that meets, if not exceeds, industry standards is paramount for customer satisfaction and long-term business relationships.
In the modern steel industry, the imperative for environmentally sustainable practices is ever-present.
Skin pass steel processes are continually evolving to meet these demands, adopting energy-efficient technologies and minimizing waste production. Forward-thinking manufacturers invest in research and development to explore greener alternatives, such as more efficient lubricants and reduced carbon footprints during production. By prioritizing environmental responsibility alongside technical excellence, these manufacturers not only meet market expectations but also contribute positively to sustainable development goals worldwide.
In summary, skin pass steel is more than just a finishing technique; it is an essential process that combines experiential insights, expert knowledge, authoritative methodologies, and trustworthiness in quality and sustainability. Embracing these attributes, manufacturers are better equipped to deliver advanced steel solutions that meet the intricate demands of modern industry, all while ensuring that their processes are aligned with the latest advancements and environmental considerations.