In the realm of metal processing, the skin pass mill process stands as an indispensable step, bridging the initial rough production of steel and the requirements of various industries demanding precision and quality. Those acquainted with the process appreciate the nuanced improvements it imparts to metal products, elevating their applicability across diverse sectors.
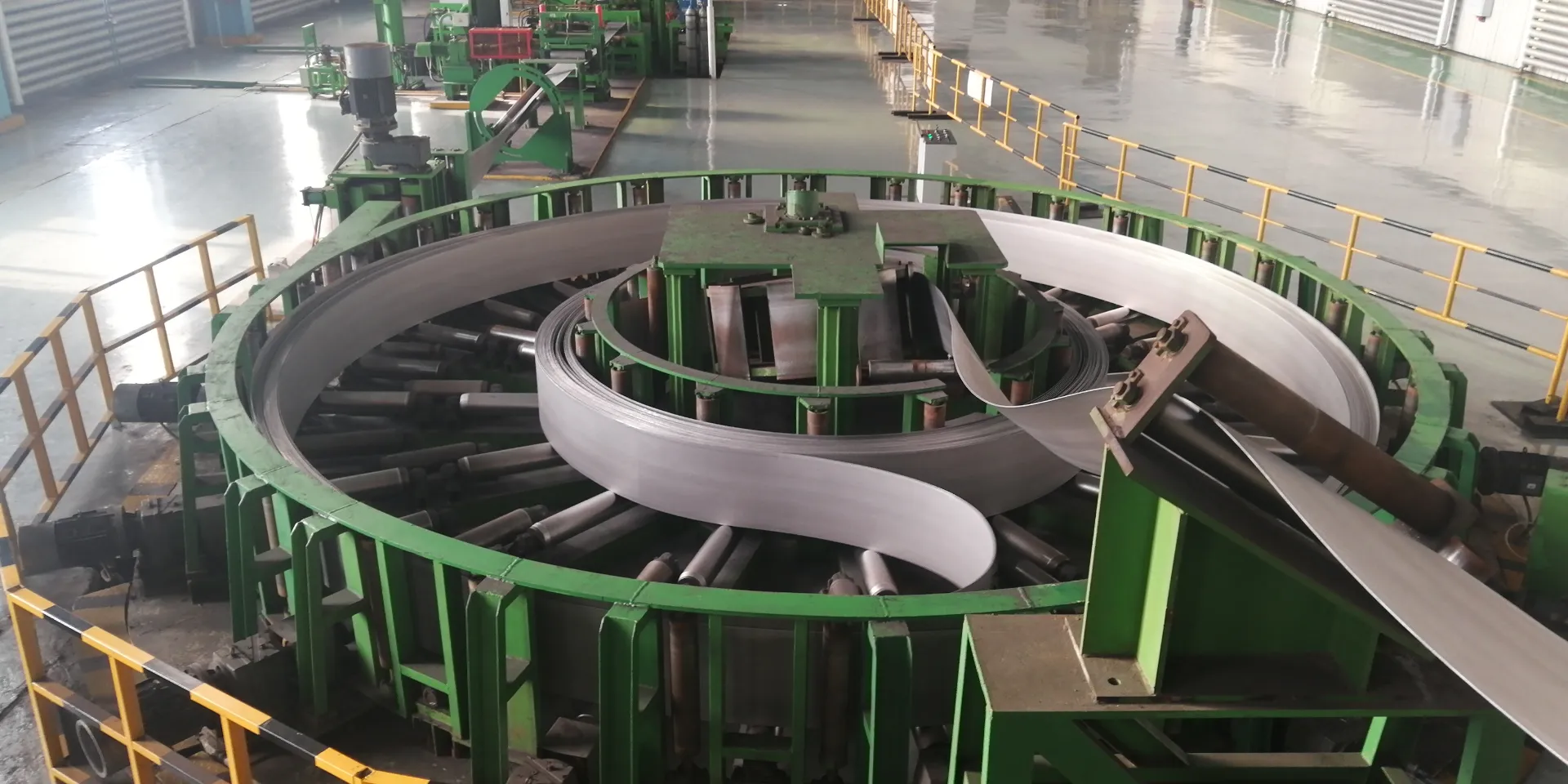
At its core, the skin pass mill process involves a light cold rolling operation applied to steel strips. This technique provides definitive enhancements such as improved surface finish, elongation adjustment, and increased yield strength—attributes crucial for products requiring superior surface quality and specific mechanical properties.
The expertise behind this process begins with understanding its primary purpose improving surface flatness and minimizing deviations, also known as defects. By applying a light reduction on the strip, typically between 0.5% and 3%, the skin pass mill generates a more uniform surface structure, greatly enhancing the steel’s aesthetic and practical appeal. This is especially vital for industries such as automotive and appliance manufacturing, where surface appearance is as important as functionality.
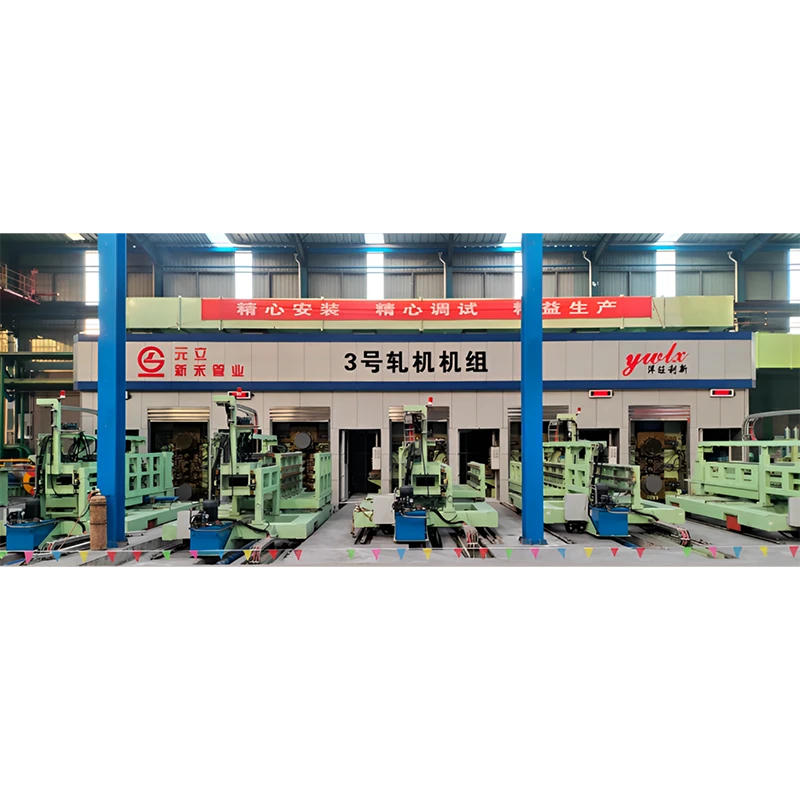
Another notable outcome of the skin pass mill process is its effect on steel’s mechanical properties, notably, the enhancement of yield and tensile strength. These strengthened characteristics are crucial for ensuring that the steel withstands further forming or end-use without failure. The controlled elongation achieved during this process also assists in maintaining consistent dimensional accuracy, a parameter highly valued in roll-forming operations and complex assemblies.
Authoritative voices in the metallurgical sector emphasize the importance of tailored mill settings. Advanced skin pass mills are equipped with sophisticated control systems that adjust roll gap, tension, and speed to match specific production demands. Operators with comprehensive expertise in metallurgy are indispensable, as they balance the interplay between roll force and strip tension to achieve the exact outcomes required by clients.
skin pass mill process
One cannot overlook the influence of reliable machinery in this process. High-quality roll materials and precision engineering play a pivotal role in executing effective skin pass operations. Manufacturers invest in state-of-the-art mills with closed-loop control systems that ensure reproducibility and high throughput. This technical investment is a testament to the industry's commitment to delivering unparalleled steel quality.
Trustworthiness in the skin pass mill process is reflected through adherence to stringent quality control standards. Facilities implementing ISO certifications and continuous monitoring systems exemplify the industry's dedication to maintaining product consistency and meeting customer specifications. Furthermore, traceability protocols ensure that each steel coil processed can be linked back to its raw material source, providing customers with confidence in the integrity of their supply chain.
From a commercial standpoint, the skin pass mill process presents a compelling value proposition. It extends the lifespan of downstream processing tools by reducing surface defects, thereby minimizing equipment wear and maintenance costs. By delivering metals that meet precise industrial demands, the process also reduces material wastage and optimizes resource efficiency.
In conclusion, the skin pass mill process is an art form in the steel processing industry that combines experience, expertise, authoritativeness, and trustworthiness. As industries continue to demand higher standards for steel quality, the refinement capabilities provided by skin pass milling are more critical than ever. This process not only ensures adherence to stringent quality standards but also enhances the longevity, reliability, and aesthetic appeal of metal products, paving the way for innovative applications across the global market.