The skinpass rolling mill process stands as a crucial refinement stage in the production of flat-rolled steel and metal sheets. This intricate process significantly enhances the surface quality, mechanical properties, and overall aesthetics of the metal products. Here's an in-depth look into the skinpass process, enriched with real experience and authoritative insights.
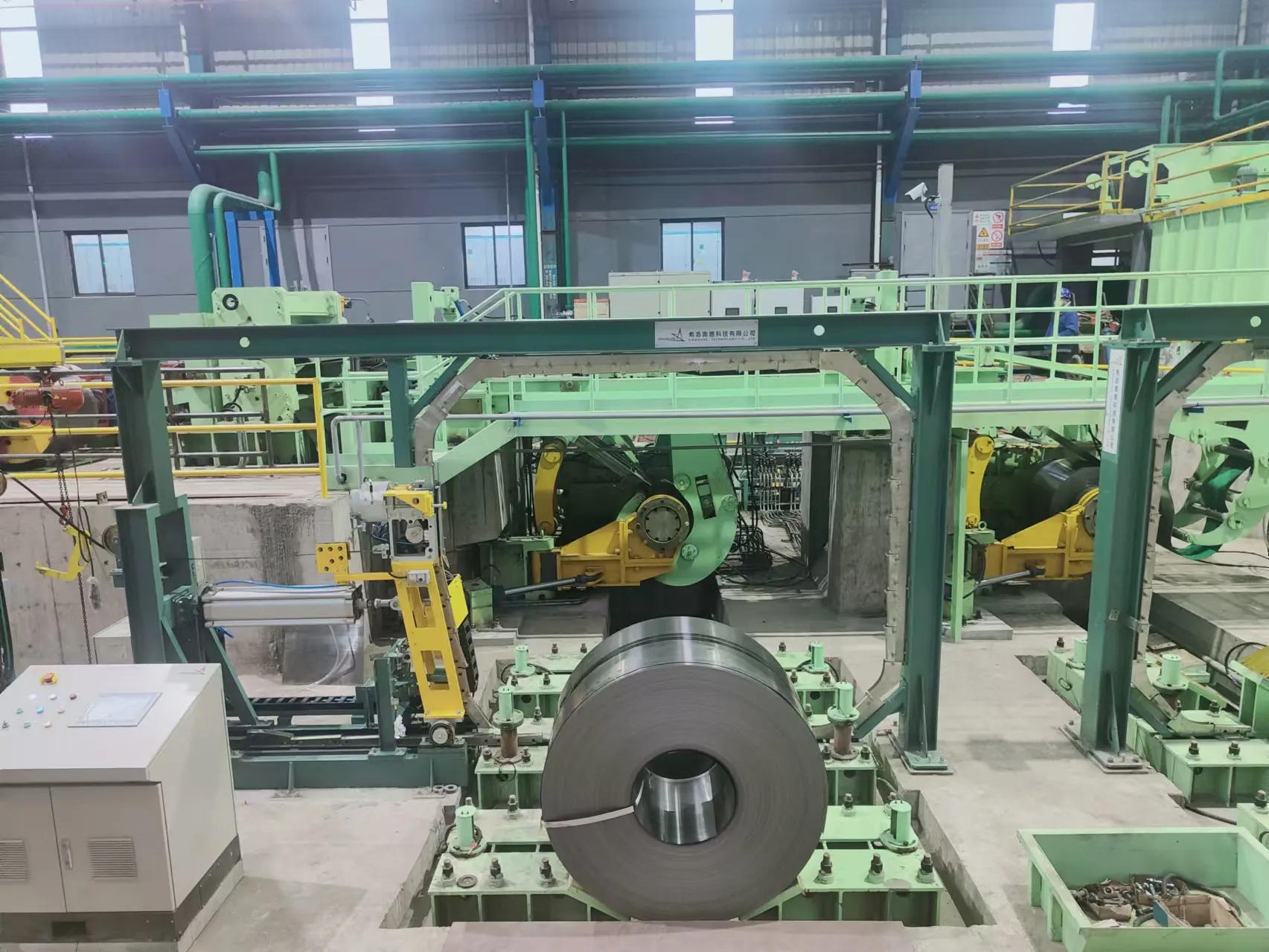
In the steel manufacturing industry, achieving the perfect surface finish and strength in final products often necessitates more than just the initial rolling and forming. Enter the skinpass rolling mill—an essential finishing step that imparts the desired texture, gloss,
and mechanical properties to metals. Drawing from real-world experience, companies like ArcelorMittal and Nippon Steel have long recognized the value skinpassing adds, reinforcing its importance through their continued innovations and investment in state-of-the-art technology.
Expertise in the skinpass process reveals that it involves passing metal sheets through a rolling mill with a relatively small reduction ratio. Unlike other rolling mills that primarily focus on thinning the metal, the skinpass process, typically carried out at the final stages of production, serves to perfect and seal the surface. The process is applied to cold-rolled, galvanized, and some hot-rolled sheets.
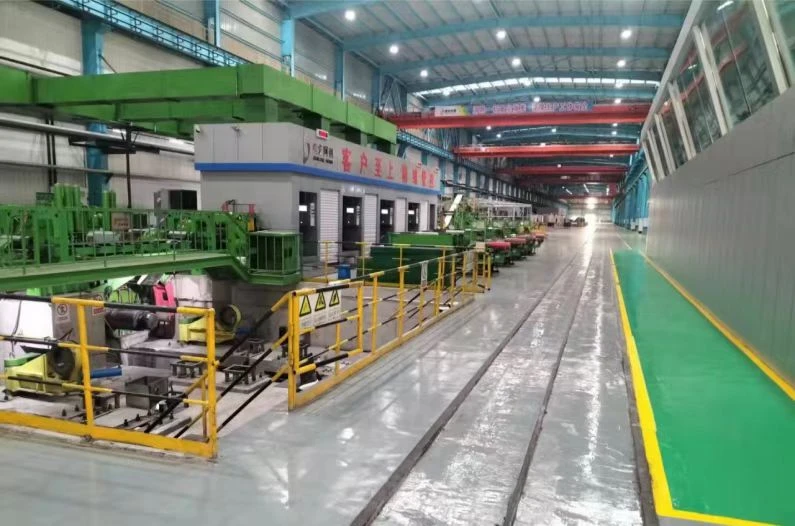
The skinpass rolling mill is characterized by precision and control—two key elements that ensure improved flatness, minimized residual stress, and enhanced microstructure of the material. These improvements are crucial in products requiring tight adherence to specifications, such as automobile panels and home appliances, where defects can lead to significant performance and aesthetic issues.
Authoritative manufacturers highlight the employment of both single and double skinpass rolling mill setups, depending on the required end-product specifications. Advanced mills, like the 6-high and 4-high skinpass mills, offer enhanced control over the process, allowing operators to manipulate tension, pressure, and roll speed meticulously, thus achieving highly desired material properties.
skinpass-walzwerk-prozess
Trustworthiness in the product quality emerging from the skinpass process is further endorsed by the consistent output of metals with excellent paint adhesion, surface toughness, and resistance to further processing deformations. This credibility is essential for sectors such as automotive, where product failure is simply unacceptable.
From an operational perspective, the skinpass process contributes significantly to reducing subsequent processing woes, such as rust and storage stain issues, by refining the surface to close-up open grain structures. It effectively eliminates the tendency for stretcher strains, also known as Lüders bands, which mar the surface appearance.
Experience gathered across global steel production giants illustrates the tangible improvements in yield strength and ductility, attributed to controlled work hardening introduced during skinpassing. These mechanical enhancements cater to diverse industrial applications, meeting stringent engineering demands.
In conclusion, the skinpass rolling mill is a linchpin in steel production, pivotal in transforming basic rolled products into refined, market-ready goods with superior quality and performance attributes. Its role underscores an expert blend of technical precision and industry-proven methodologies. The process offers manufacturers a reliable path not just to meet, but often exceed, the expectations of quality-conscious end-users—a promise of durability and aesthetic excellence embodied in every expertly skinpassed sheet.