Gravity roller conveyors have transformed the landscape of material handling, offering a streamlined solution for industries seeking efficiency without the complexity of powered systems. These conveyors rely on gravitational forces to move goods, making them an energy-efficient option for transporting products over short distances. Besides efficiency, they embody a straightforward design and minimalistic operational requirements, which are quintessential for businesses aiming to optimize their operations while maintaining a robust logistical backbone.
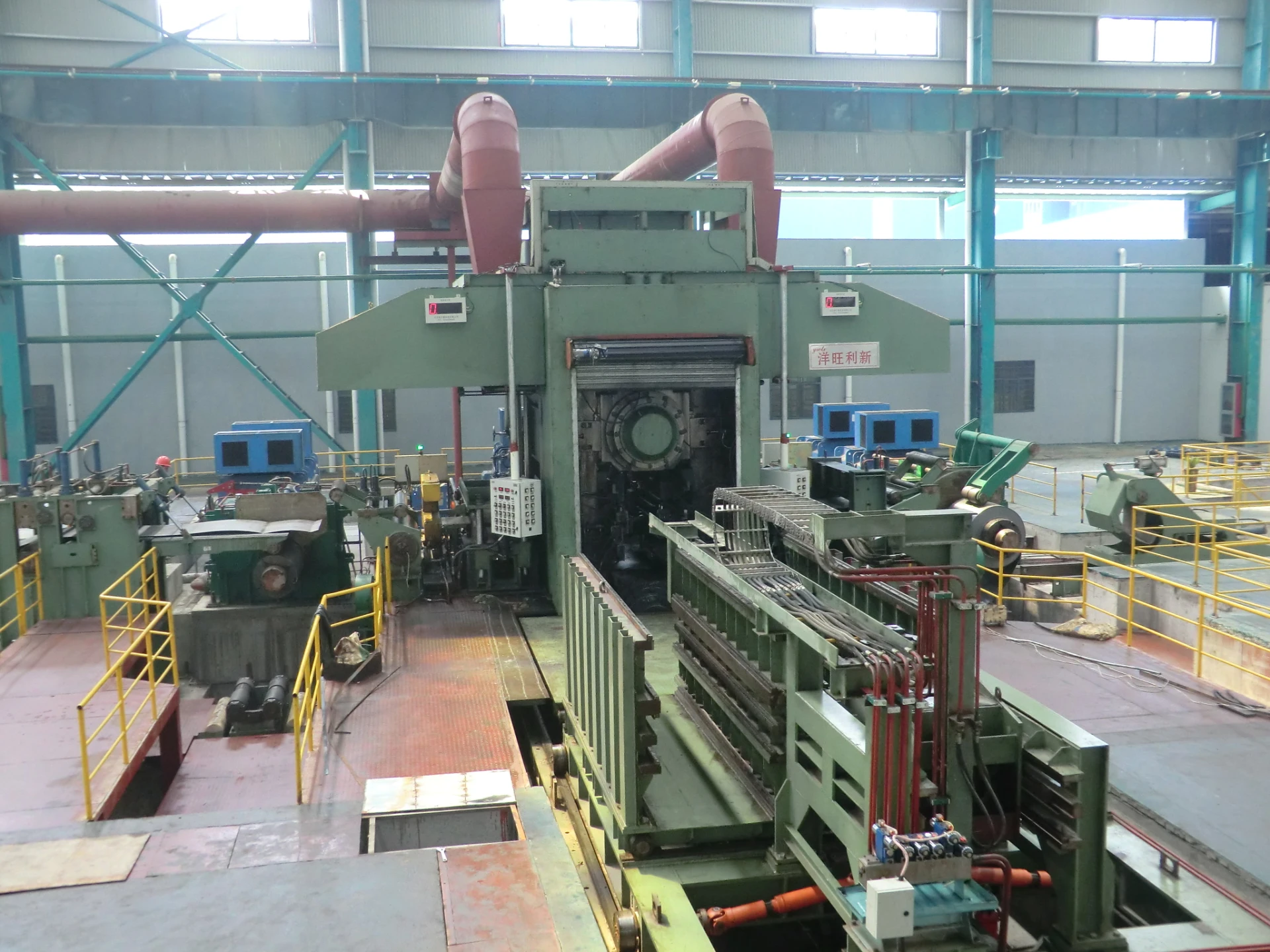
In terms of expertise,
gravity roller conveyors excel in environments where simplicity and durability are paramount. They are crafted from high-quality materials, including steel, aluminum, and sometimes plastic, depending on the specific needs of the application. Their design incorporates a series of rollers, mounted on axles, freely rotating under the weight of the products. This design simplicity ensures minimal maintenance, thereby reducing downtime and enhancing productivity.
A key aspect of their authoritativeness in the material handling sector is their adaptability. Gravity roller conveyors can be customized to fit various industrial needs, from simple conveyance tasks in warehouses to complex sorting and distribution functions in larger production facilities. They can be integrated with additional components like workstation lifts, gravity-skate wheel conveyors, and even be employed as part of automated systems to further refine efficiency levels.
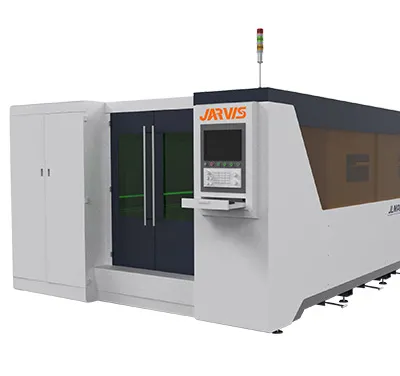
Trustworthiness in gravity roller conveyors comes from their long-standing history of reliability and effectiveness. They have been a staple in sectors such as manufacturing, assembly lines, and distribution centers. Their operative efficiency is bolstered by their ability to handle diverse load types, from light cartons to heavier assemblies. The inherent flexibility allows businesses to reconfigure their layout cost-effectively, adapting swiftly to changing operational demands.
gravity conveyor rollers
In a practical experience dimension, implementing gravity roller conveyors can significantly cut operational costs. Without the need for motors or complex control systems, businesses enjoy savings on energy and equipment upkeep. This not only yields financial benefits but also aligns with sustainable business practices by reducing carbon footprints associated with powered conveyance systems.
Moreover, in environments with a focus on safety, gravity roller conveyors present a reduced risk scenario. The absence of powered components reduces potential hazards, making them a safer choice for human interaction. This safety is enhanced by training and ergonomic design adjustments that cater to operator convenience and ease of loading and unloading, further highlighting their role in maintaining a safe working environment.
From a market perspective, the evolution of gravity roller conveyors conjoins finely with lean management principles, reinforcing the value of maximizing efficiency by minimizing waste. This approach aligns with contemporary business strategies that prioritize lean operations and continuous improvement.
To conclude, gravity roller conveyors are not just a component; they are a catalyst for efficient, safe, and cost-effective material handling solutions. Their proven track record, adaptability, and straightforward design have established them as an authoritative presence in logistics and material handling industries worldwide. As businesses pivot towards more sustainable and efficient operations, gravity roller conveyors will undoubtedly remain a fundamental element of industrial design and strategy, driving success through simplicity and reliability.