In the ever-evolving world of metallurgy and manufacturing, the round wire rolling mill stands as a pivotal piece of technology. This machinery, robust and meticulously designed, plays a critical role in shaping metals that form the backbone of various industries. Specializing in transforming raw metal into fine wires, this equipment must combine precision, durability, and efficiency to meet the high standards set by modern manufacturing demands.
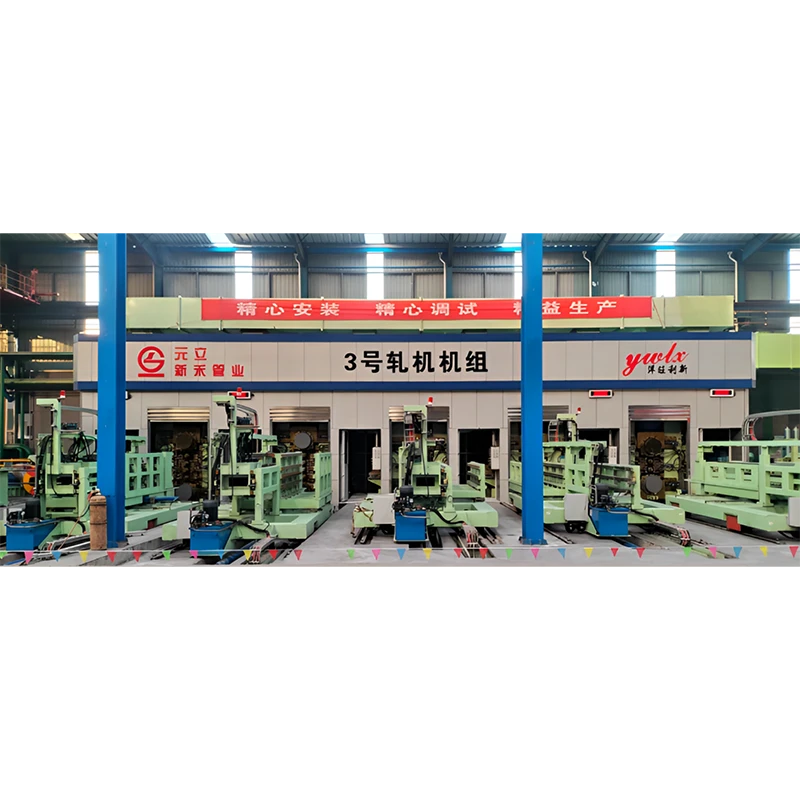
From an expert's viewpoint, understanding the intricacies of a round wire rolling mill is crucial for any industry professional. These mills operate by exerting large amounts of pressure on metal rods, reshaping them into thinner, more manageable wire forms through a series of carefully calibrated rolls. The mill's process is akin to an artisan sculpting metal, each roll reducing the rod’s diameter and simultaneously improving its structural integrity and surface finish.
One of the primary attributes of a successful round wire rolling mill is the material it processes. Professionals working with these machines need to consider the composition of the starting material, which can range from copper, aluminum, to more exotic alloys. Material selection impacts the rolling mill settings and the resulting wire properties, such as tensile strength and conductivity. Each material presents unique challenges; for instance, copper is malleable yet requires careful handling to prevent surface oxidation during processing.
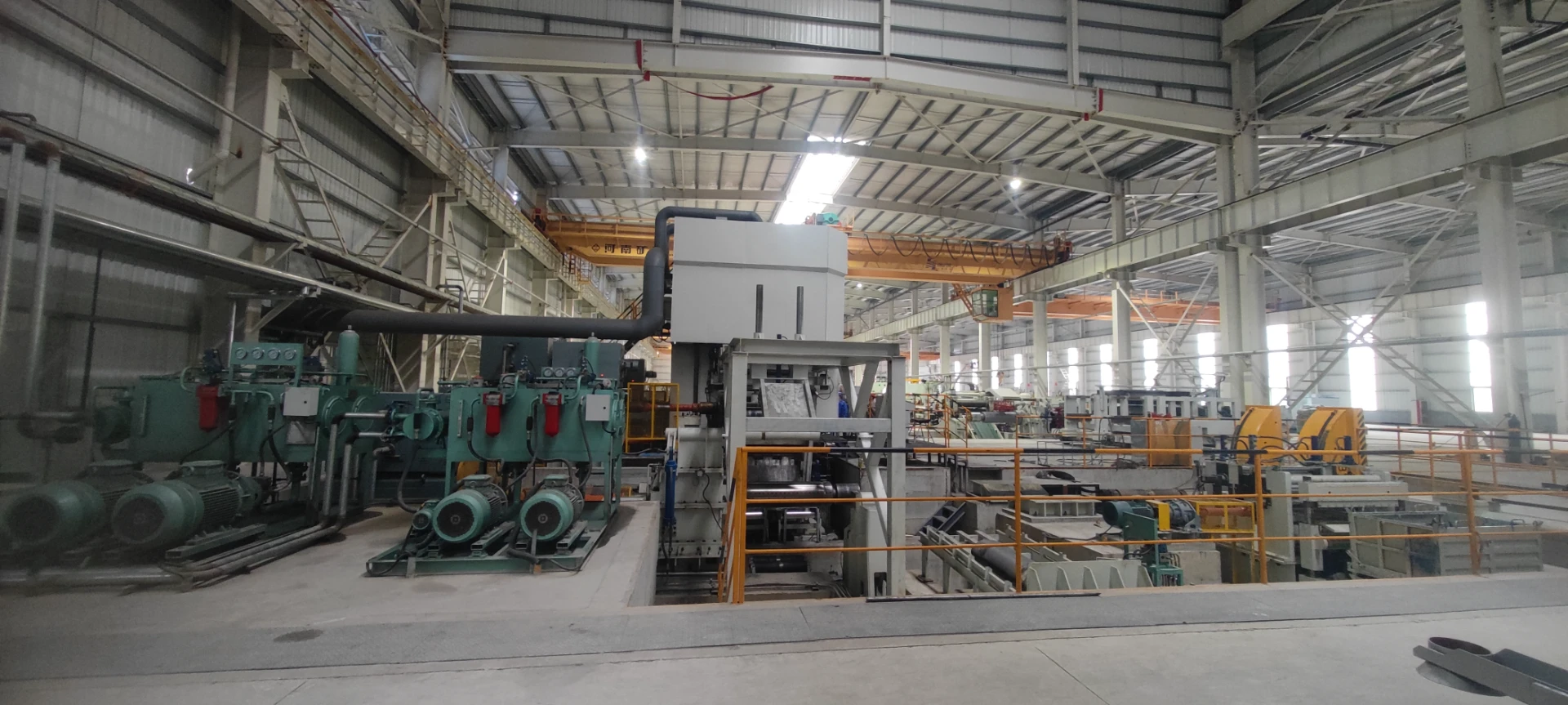
Expert operation of a rolling mill demands an acute understanding of the mechanical forces at play. The roll pressure, typically controlled through hydraulic or mechanical systems, must be finely tuned to achieve the desired wire thickness without compromising the wire’s quality. The speed of the rolling process is another critical factor. Rolling too quickly can lead to undesirable heat buildup, affecting the wire’s temper and causing structural weaknesses.
Precision engineering is also crucial in maintaining the high-quality output of a round wire rolling mill. Regular maintenance checks and calibrations ensure that the rolls are aligned correctly and the machinery operates smoothly. State-of-the-art monitoring systems can aid operators by providing real-time data on roll pressure, temperature, and other critical parameters, allowing for on-the-fly adjustments that maintain optimal performance.
round wire rolling mill
Trustworthiness in a rolling mill comes from its consistent output. Manufacturers invest heavily in quality assurance processes to ensure each batch of wire meets stringent specifications. This process often involves both automated and manual inspection techniques, where sample wires are tested for diameter consistency, surface finish, and material properties. Creating a cycle of feedback and improvement, these tests inform future runs, optimizing processes and reducing waste.
Harnessing the capabilities of round wire rolling mills requires not just technical skill but a dedication to innovation. The evolving demands of sectors such as telecommunications, construction, and electronics push the boundaries of what these machines can achieve. Manufacturers who understand and invest in cutting-edge technology and skilled workforce gain a competitive edge, producing wires that meet the future’s stringent requirements.
The authoritative role of the round wire rolling mill in today's industries cannot be overstated. As businesses seek to enhance efficiency and product quality, these machines are increasingly becoming focal points of technological advancement. Those with comprehensive expertise in metalworking, along with a commitment to excellence, find themselves uniquely positioned to lead in this crucial aspect of material production.
For companies and professionals looking to stay ahead, leveraging the experience and knowledge housed in round wire rolling mills is essential. Embracing modern advancements while respecting the craft’s foundational principles ensures not only technical success but also a legacy of quality and reliability in metal manufacturing.