Rollenspannungsregelung, known as roller tension control in English, plays a critical role in industries where material processing and handling are central. A precise understanding and application of roll tension control can drastically improve product quality, operational efficiency, and equipment longevity. This emphasis not only enhances the production process but also satisfies the stringent demands of modern manufacturing.
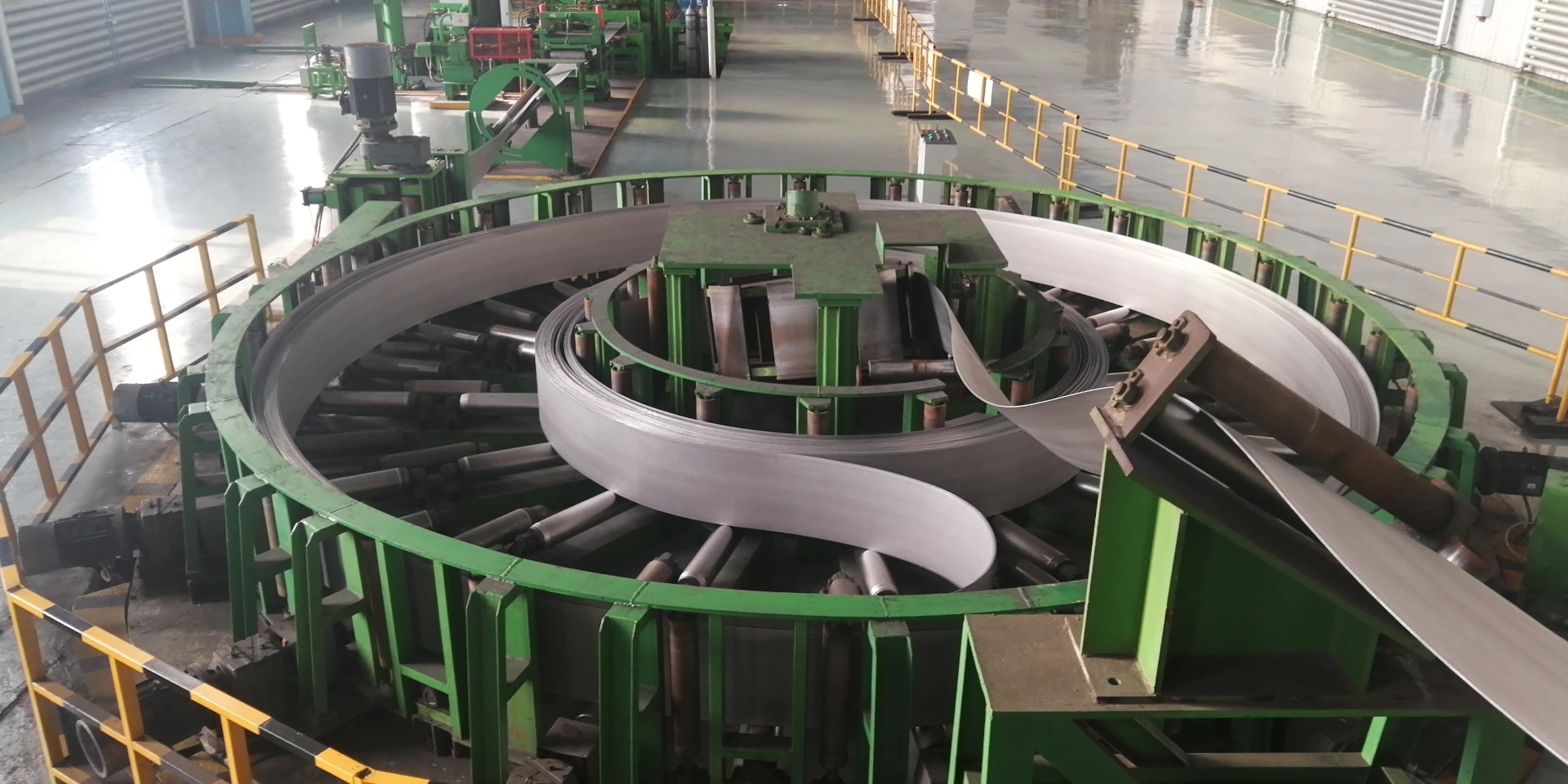
Roll tension control involves maintaining the appropriate tension on materials as they wind or unwind during processing. This technology is especially relevant in industries such as textiles, packaging, plastics, and paper manufacturing. Here, the adept use of roll tension control can mean the difference between success and operational failure.
Experience in implementing roll tension control underscores its transformative impact. Consider a mid-sized packaging company that recently integrated a sophisticated roll tension control system. Before implementation, the company faced frequent material tears and inconsistent product quality, which led to increased waste and elevated costs. The introduction of roll tension control minimized these issues by ensuring optimal tension was maintained throughout the process. Consequently, this led to tighter quality control, reduced material waste, and improved customer satisfaction due to consistent product standardization.
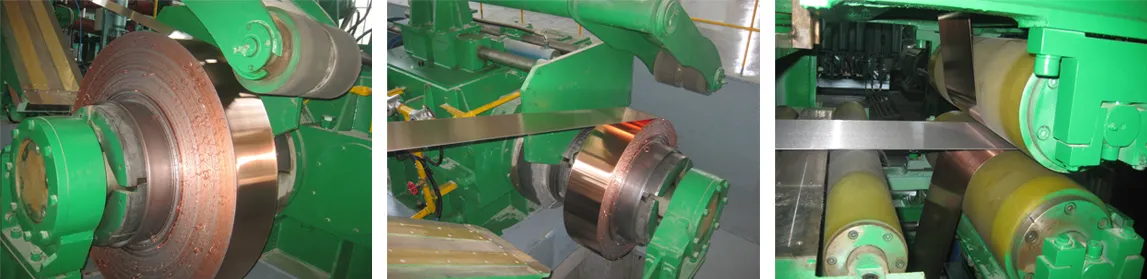
Expertise in roll tension control is paramount. Understanding the nuances of different materials and their respective tension requirements demands a high level of technical skill. For example, materials like paper require a delicate balance; too much tension can tear the material, while too little can cause slackness and misalignment. Experts in this field leverage advanced sensors and automated systems that adjust in real-time to maintain the desired tension, illustrating an impressive level of technological integration and precision.
rollenspannungsregelung
In terms of authoritativeness, industry leaders and technical experts continuously explore advancements in roll tension technology. Much of today’s cutting-edge research focuses on precision sensors and AI-driven systems that predict tension adjustments before anomalies occur. Publications detailing the benefits and technicalities of roll tension control contribute significantly to field knowledge, cementing the importance of this technology in achieving high-quality outputs in manufacturing.
Trustworthiness is bolstered through consistent, evidence-backed results. Companies that have adopted advanced roll tension systems report noticeable improvements in operational efficiency and product quality. Furthermore, original equipment manufacturers (OEMs) often collaborate with industry experts to develop solutions tailored to specific material properties and processing objectives, thereby ensuring that technology meets the distinct needs of each industrial application. These partnerships often include rigorous trials and iterations to guarantee efficacy and reliability.
Beyond its practical applications, roll tension control exemplifies a commitment to sustainable practices. By optimizing material usage and minimizing waste, companies can significantly reduce their environmental footprint. This aspect is crucial as industries worldwide strive towards greener operations and sustainability. The reduction in wastage not only lowers costs but also aligns with global environmental objectives, contributing to a brand’s reputation as a responsible corporate entity.
In conclusion, roll tension control is indispensable in today's manufacturing landscape, requiring a blend of experience, technical expertise, authoritative knowledge, and trust. The successful application of this technology enhances product quality, operational efficiency, and environmental sustainability. As industries continue to evolve, so too will the technologies that define them, with roll tension control leading the charge in ensuring a seamless and efficient transition into the future of manufacturing.