Understanding the complexities of rolled strip production is crucial for industries that rely on precision-engineered materials. As a vital component in manufacturing, the rolled strip offers unmatched versatility and utility across numerous sectors, including automotive, aerospace, packaging, and electronics.
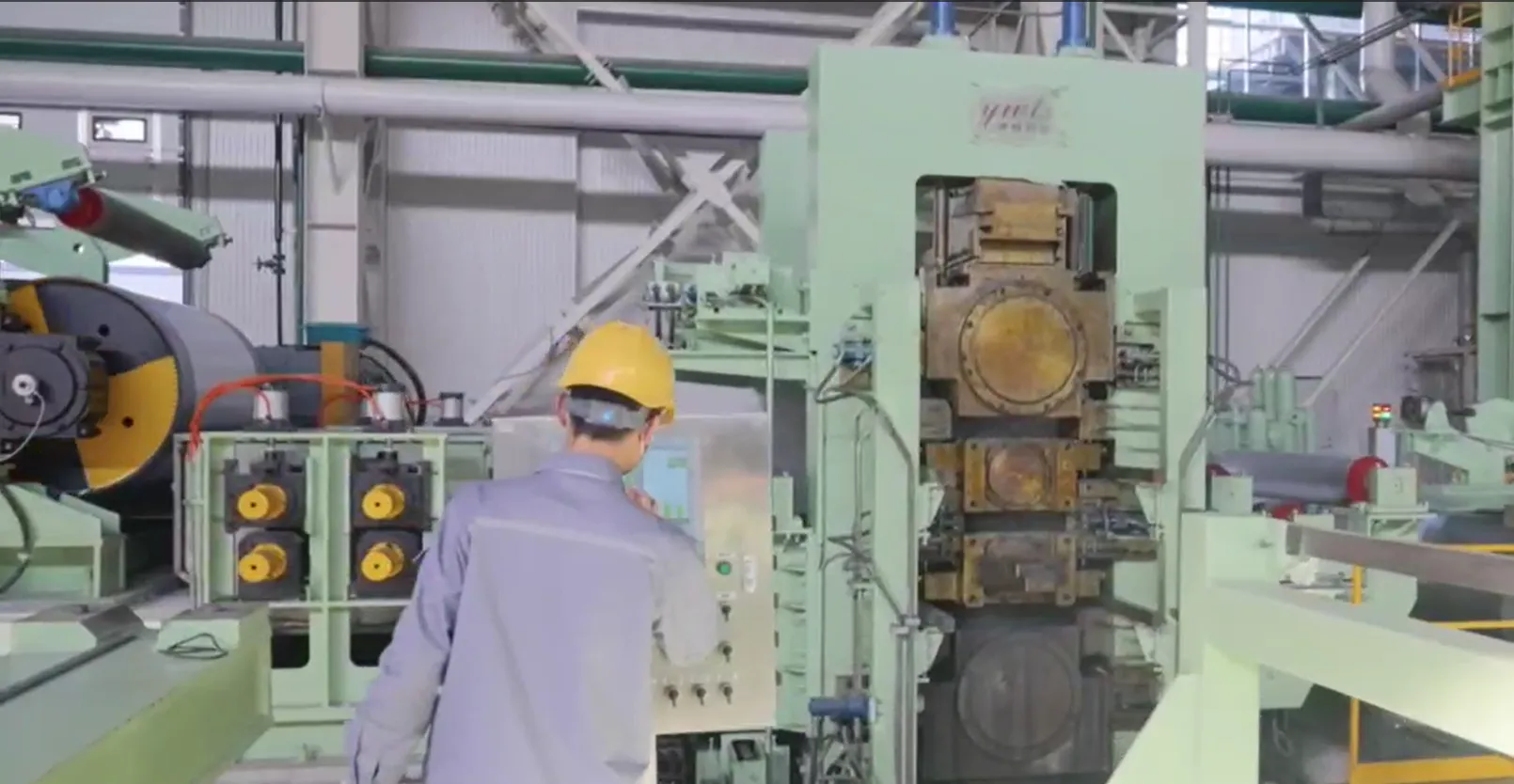
Real-world experience underscores the importance of selecting the appropriate rolled strip for specific applications. Engineers and fabricators often face challenges related to material durability, thickness,
and tolerance requirements. Roll forming technology has evolved to meet these demands, ensuring the delivery of consistent quality and performance. By optimizing rolling processes, manufacturers can reduce material waste, enhance structural integrity, and improve the dimensional precision of the finished strips.
From a professional standpoint, understanding the metallurgical properties of rolled strips is paramount. These strips are typically produced from metals like steel, aluminum, and copper, each offering distinct benefits and limitations based on the intended use. For instance, in the automotive industry, steel rolled strips are favored for their strength and durability, while aluminum strips are preferred for applications demanding lighter weight materials, such as in aerospace technologies.
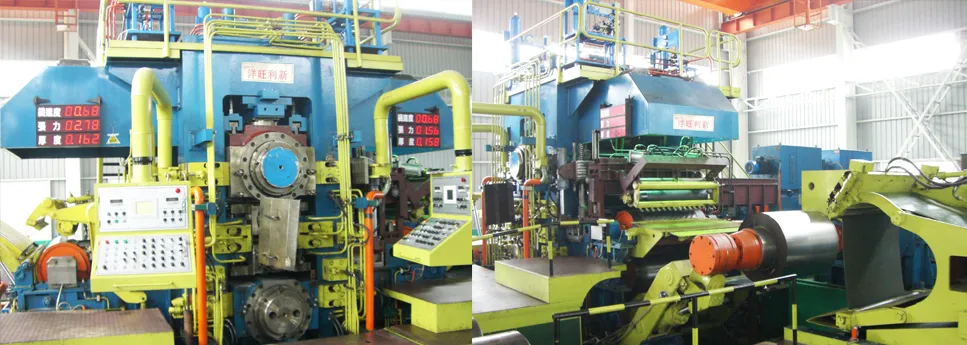
Professionals in the field are keenly aware of the regulatory standards that govern rolled strip production. ISO and ASTM guidelines ensure that materials meet stringent criteria for safety and reliability. Companies must stay current with industry standards to maintain their credibility and trustworthiness. This involves regular training and updates for personnel involved in the production and inspection of rolled strips.
rolled strip
Authoritativeness is established through continuous investment in state-of-the-art rolling technology and rigorous quality assurance measures. Leading manufacturers employ automated systems that precisely control the rolling process, minimizing human error and ensuring uniformity across batches. These systems can detect deviations in strip thickness and surface quality, enabling quick corrective actions and maintaining high standards of production.
Trustworthiness in the rolled strip industry hinges on transparent and ethical business practices. Suppliers who provide comprehensive product data, including detailed specifications and performance metrics, instill confidence in their clients. Building long-term partnerships with clients involves open communication and a commitment to meeting bespoke requirements, thereby fostering a reputation for reliability and excellence.
The rolled strip product landscape is continually evolving, driven by the need for increased functionality and environmental sustainability. Innovations in material science are leading to the development of new alloys and composites that offer superior performance while reducing the carbon footprint of production processes. Recycling initiatives and the use of eco-friendly lubricants in rolling mills further enhance the sustainable credentials of modern rolled strips.
In conclusion, staying competitive in the rolled strip market requires a deep understanding of material science, advanced manufacturing techniques, and adherence to industry standards. By prioritizing experience, professional expertise, and steadfast adherence to ethical practices, companies can secure their position as leaders in this industrial niche. This approach not only ensures the deliverance of high-quality rolled strips but also strengthens relationships with customers, underscoring a commitment to excellence and trust.