Steel sheet metal lamination is a critical process in the metalworking industry, where precision and quality are paramount. This process involves the transformation of raw steel into thin, flat pieces that can be further processed for various industrial applications, including construction, automotive, and consumer goods. Given its importance, understanding the intricacies of steel sheet lamination can provide a competitive edge for businesses seeking to improve the performance and durability of their products.
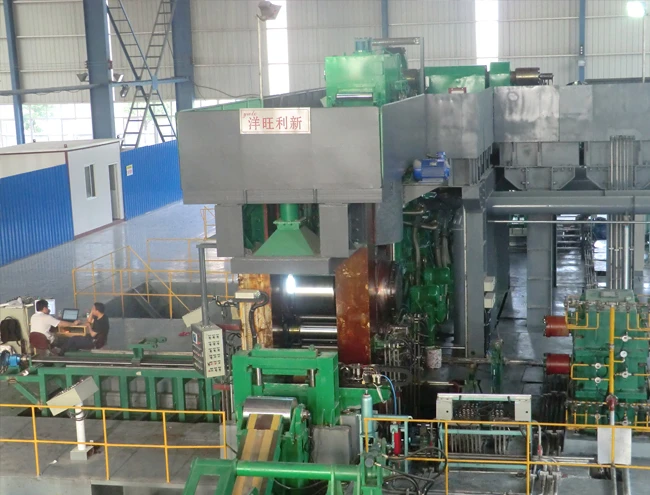
One of the primary aspects of steel sheet lamination is the selection of the appropriate type of steel. Depending on the intended application, different steel grades may be required to ensure optimal performance. For instance, high-strength low-alloy (HSLA) steels are often chosen for automotive applications due to their excellent strength-to-weight ratio, which enhances vehicle fuel efficiency while maintaining safety standards.
The process begins with the careful preparation of the steel slabs, which are cleaned and heated to ensure ductility. This heating is crucial as it makes the steel more malleable, allowing it to be processed into thin sheets without compromising its structural integrity. Achieving precise control over temperature and pressure during this stage is fundamental to producing high-quality laminated sheets that meet industry standards.

In the actual lamination process, the steel is passed through a series of rollers that gradually reduce its thickness. This technique, known as cold rolling, enhances the material's strength and surface finish while ensuring tight tolerances. Cold rolling is often preferred due to its capability to produce a superior surface finish and high dimensional accuracy. The expertise involved in managing the rolling process cannot be understated, as it requires a deep understanding of metallurgical principles and a keen eye for detail.
Experienced professionals in the field emphasize the importance of maintaining equipment and employing advanced technologies to monitor the lamination process. For instance, using precision sensors and real-time monitoring systems helps detect any anomalies during production, allowing for immediate adjustments that prevent defects and reduce waste.
lamination of steel sheets
Post-lamination treatment such as annealing and galvanizing further improves the functional properties of the steel sheets. Annealing relieves internal stresses, imparting increased ductility and making the sheets easier to work with in subsequent manufacturing operations. Galvanizing, on the other hand, provides a protective zinc coating that enhances corrosion resistance, a vital attribute for steels used in outdoor or harsh environments.
Expertise in steel sheet lamination extends beyond technical proficiency. Building trust with clients involves transparent communication about material capabilities, anticipated performance in specific applications, and adherence to global quality standards. Demonstrating experience through case studies or customer testimonials can further enhance credibility and authority in the field.
Trustworthiness is further reinforced through compliance with industry certifications and proactively addressing environmental and safety concerns. Implementing eco-friendly practices, such as recycling scrap material and minimizing energy consumption during production, not only aligns with sustainable business models but also appeals to environmentally-conscious consumers.
In summary, steel sheet metal lamination combines intricate technical processes and expert knowledge to produce materials that are integral to numerous industries. Mastery of this domain involves not only producing high-quality laminated steel sheets but also ensuring that the process is efficient, reliable, and sustainable. By aligning these practices with client needs and industry trends, businesses can establish themselves as authoritative leaders in the field of steel sheet lamination.