Two-roll laminators have revolutionized the manufacturing industry by offering unparalleled precision and efficiency in material processing. Commonly utilized in sectors such as metalworking, plastics, and textiles, these machines are integral in transforming raw materials into high-quality finished products.
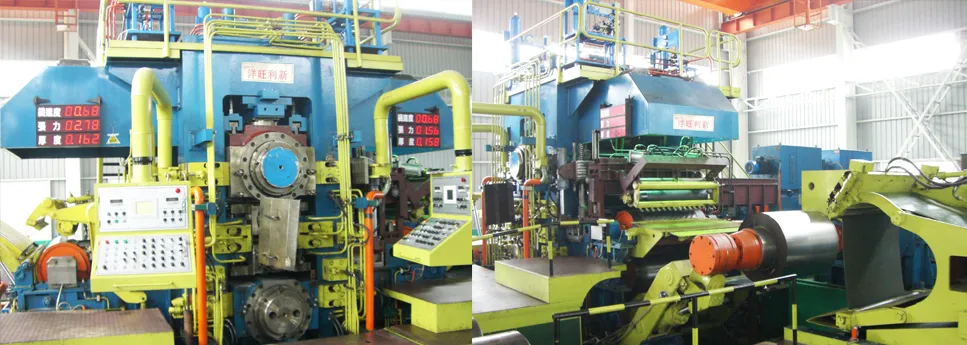
An exemplary feature of two-roll laminators is their capability to produce consistent thickness across materials, crucial for industries that demand uniformity in product specifications. Unlike other laminating systems that may struggle with variances in material thickness, these machines maintain consistency by applying even pressure during the lamination process. This precision directly contributes to enhanced product quality, reducing waste and ensuring client satisfaction.
Several industries have reaped significant benefits from incorporating two-roll laminators into their production lines. For instance, in the metal industry, these machines are crucial for producing metal sheets with exact thicknesses required for construction and automotive applications. Similarly, the plastics industry relies on them to create films and sheets with precise dimensional tolerances, essential for packaging and manufacturing processes.
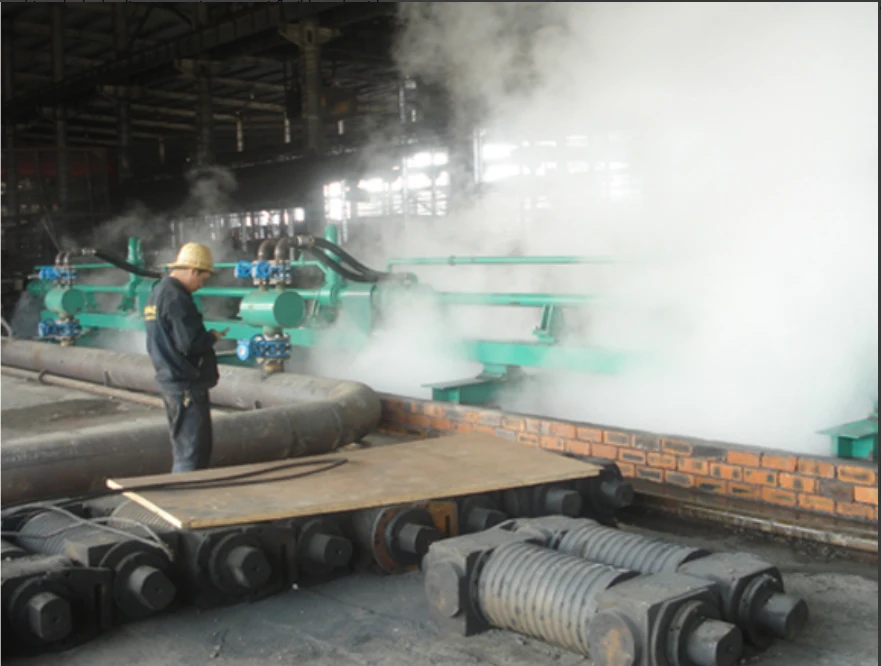
The expertise embedded in operating a two-roll laminator cannot be understated. Operators must possess a profound understanding of the material science and mechanics involved in the lamination process. Appropriate adjustment of variables such as temperature, pressure, and speed is essential to optimize output quality. Specialist training is often necessary to enhance these competencies, which in turn amplifies the operational efficiency and lifespan of the machinery.
Moreover,
these machines are celebrated for their durability and reliability. Manufactured with high-strength materials, they withstand extreme operational conditions, thus attesting to their trustworthiness in demanding industrial settings. Regular maintenance, including lubrication and alignment checks, is pivotal in prolonging machine longevity and preventing unscheduled downtimes, which can be costly for manufacturing workflows.
2-storey rolling mill
In addition to physical reliability, two-roll laminators have an authoritative presence in the industry due to continuous advances in technology. Manufacturers invest heavily in R&D to introduce cutting-edge features such as automated control systems, which enhance accuracy and reduce manual intervention. These innovations not only bolster productivity but also ensure that operators can achieve desired outcomes with minimal effort.
From an environmental perspective, two-roll laminators are increasingly designed to adhere to eco-friendly standards. Energy-efficient models reduce power consumption, while advanced control systems minimize material waste. Consequently, companies that integrate these machines into their operations can enhance their sustainability credentials, aligning with global environmental goals.
A noteworthy example of trusted brands leading the laminator market includes companies that offer customer-centric aftersales service. These services often cover comprehensive training programs, technical support, and parts replacement, ensuring users maintain peak operational efficiency and deal effectively with any technical challenges that arise.
In conclusion, two-roll laminators are vital in contemporary manufacturing, fortifying their status through consistent product quality, expert operation, robust construction, and innovative technological features. Their contribution to enhanced precision in industries ensures they remain indispensable tools in industrial transformation. Companies willing to invest in such technology can expect to achieve superior material processing results, uphold high standards of production, and capture a competitive edge in their respective fields.