Automatic Gauge Control (AGC) in strip rolling represents a breakthrough in modern manufacturing processes, illustrating the profound alignment of precision engineering and advanced computational techniques. This specific domain within the metallurgical industry has evolved significantly, promising improvements in product quality, resource efficiency, and operational reliability.
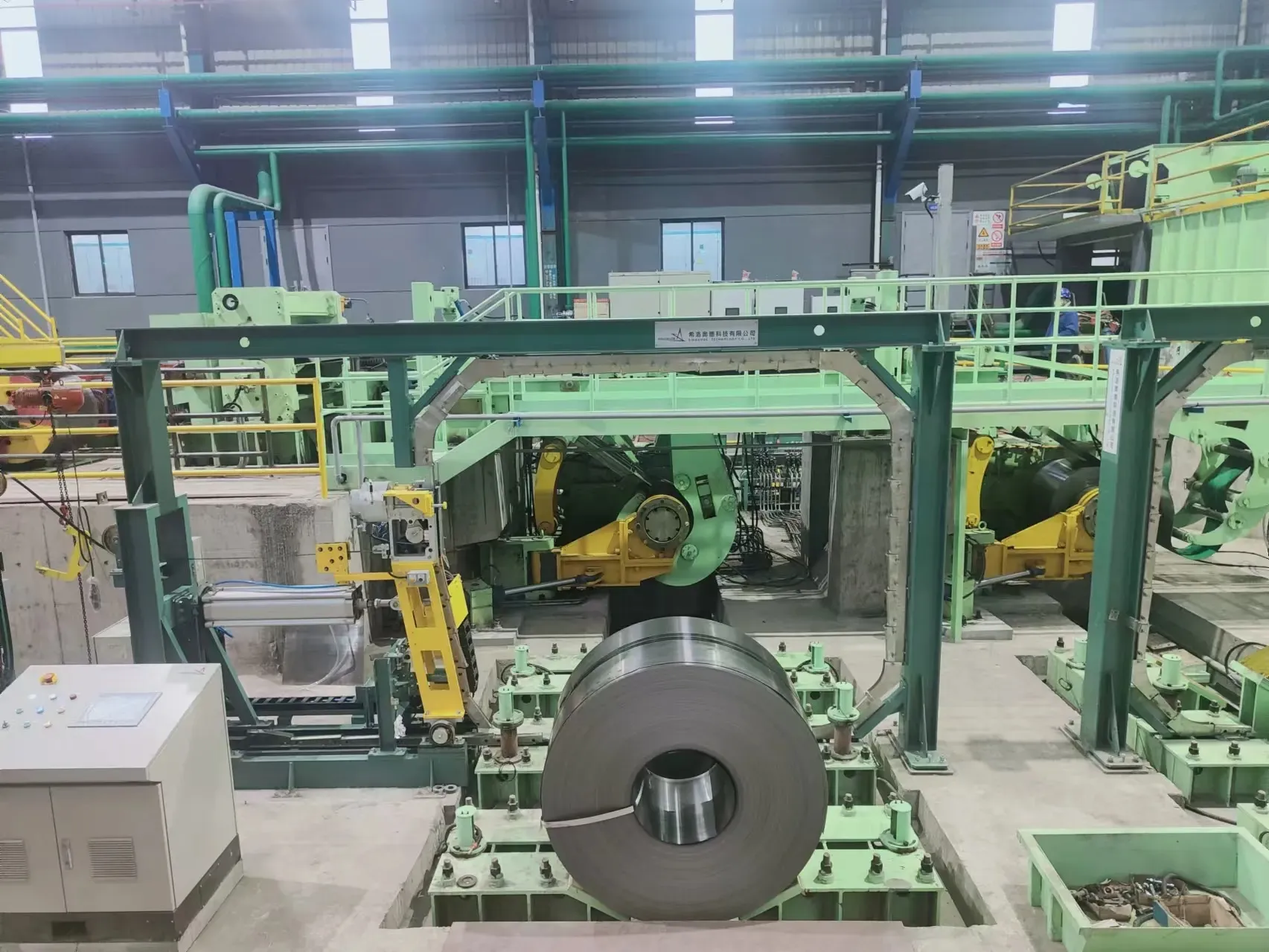
Over the past two decades, industries worldwide have seen a tremendous shift towards automation, particularly in processes such as strip rolling, where precision is paramount. The advent of AGC systems has been a game-changer. These systems are engineered using sophisticated algorithms, often backed by artificial intelligence, to control the thickness of metal strips with unprecedented accuracy.
The essence of AGC lies in its ability to respond dynamically to variations in the rolling process. Traditional methods largely relied on human operators to manually gauge and adjust the rolls, a time-intensive and error-prone approach. AGC systems, however, utilize a combination of sensors and feedback loops to continuously monitor the strip thickness. By instantly correcting deviations from the desired specifications, AGC ensures uniformity and enhances the mechanical properties of the rolled product.
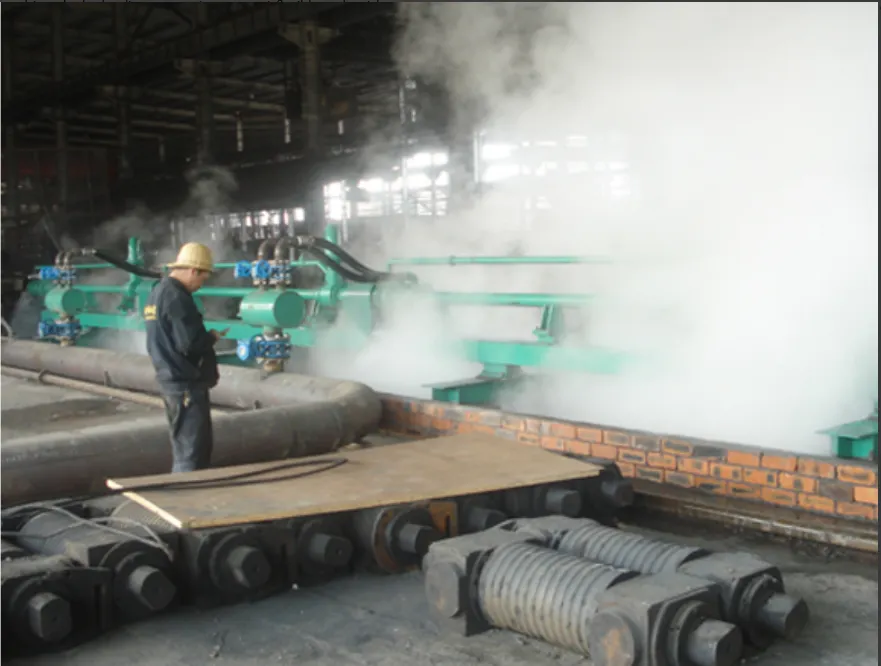
One of the standout features of modern AGC systems is their reliance on process modeling. These models predict outcomes by simulating various rolling scenarios using parameters such as strip speed, roll force, and material properties. By doing so, they can preemptively adjust the rolling parameters to maintain optimal conditions. This level of foresight not only improves efficiency but significantly reduces material wastage, leading to considerable cost savings and a more sustainable operation.
Moreover, the application of AGC systems isn't solely limited to ensuring consistent thickness. They play an integral role in guaranteeing the surface quality of the rolled product as well. By maintaining uniform pressure and minimizing variations during the rolling process, AGC helps in reducing defects such as flat spots and rough finishes, which are crucial for industries where surface integrity is essential.
A case study highlighting the effectiveness of AGC can be seen in the aerospace industry, where the demand for lightweight yet durable materials is critical. The precision offered by AGC has enabled manufacturers to produce materials that meet stringent specifications while also managing to reduce excess weight without compromising strength. This precise control underscores the AGC's capacity to improve the manufacturability of high-performance materials.
automatic gauge control in strip rolling
Expertise in AGC is supported by continuous research and development efforts across the globe. Leading industrial nations have invested heavily in refining AGC technologies, promoting collaborations between academic institutions and manufacturing giants. Such partnerships have led to the development of next-generation sensors and data acquisition systems that enhance the precision and adaptability of AGC in strip rolling.
Authorities in the field advocate for widespread adoption of AGC technologies, citing numerous benefits such as enhanced production rates and quality consistency. Industry standards today increasingly reflect the capabilities brought about by AGC, mandating manufacturers to incorporate this technology to remain competitive.
Trustworthiness in AGC systems is bolstered by rigorous testing and validation frameworks. Manufacturers often subject these systems to extensive trials, replicating myriad environmental conditions and rolling scenarios. These exhaustive checks ensure that AGC systems can withstand operational pressures and deliver performance consistently across varied conditions.
For companies looking to integrate AGC systems into their operations, the return on investment can be substantial. Not only do these systems reduce operational costs and elevate product quality, but they also enhance the overall productivity by minimizing downtime associated with manual adjustments and quality control checks. Investment in AGC is a commitment to innovation, efficiency, and sustainability.
In conclusion,
Automatic Gauge Control in strip rolling stands as a testament to the power of integrating technology with traditional manufacturing practices. It underscores a significant step towards the future of industrial manufacturing, promising advancements not just in terms of technical performance but also eco-friendly practices and economic gains. The adoption of AGC marks a crucial stride in achieving greater manufacturing excellence and positions industries to meet the challenges and demands of tomorrow's market.