Cold strip mills, essential to the manufacturing landscape, stand as pivotal components in producing high-quality steel products. Their operation involves precision, innovation, and a commitment to the highest manufacturing standards. As an SEO specialist with extensive knowledge, here’s why the exploration of cold strip mills must be methodical and informed by experience and expertise.
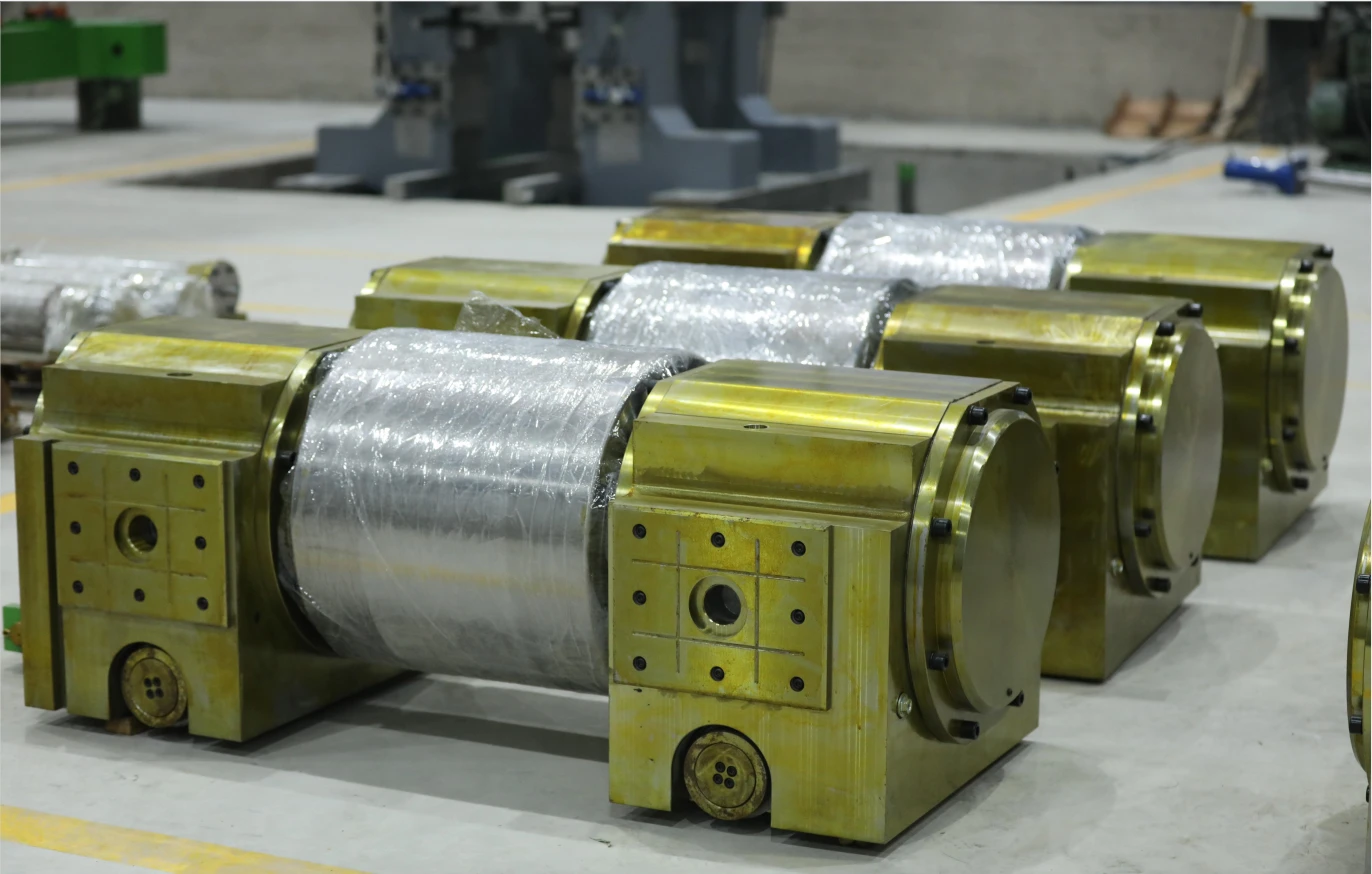
Manufacturing facilities house towering cold strip mills which play an instrumental role in refining raw steel into thin strips. This transformation is not merely physical but also structural, enhancing the properties of steel to create products that are integral to various industries. Automotive, construction, and appliance sectors all depend on these robust strips that originate from the complexities of cold milling.
The expertise required to operate these mills is non-trivial. Engineers must understand the dynamics of cooling and pressure adjustments to prevent defects in the finished strips. This finely tuned balancing act is a testament to the specialized knowledge requisite for the process. Operators need a deep understanding of materials science, thermodynamics, and mechanical engineering to oversee the intricacies of the machines.

Industry experts highlight that the evolution of cold strip mills hinges on technological advancements and continuous innovation. The incorporation of automated control systems has drastically improved efficiency, reducing human error and ensuring consistent output quality. Robotics and AI-driven analytics contribute significantly to the precision of steel shaping, allowing unprecedented control over thickness and uniformity. This expertise in cutting-edge technology speaks to the authority cold strip mills hold in modern manufacturing.
Cold strip mill
Trust in cold strip mill operations comes from an established record of reliability and safety. Manufacturers adhere to rigorous safety protocols and regulatory standards to ensure operations are secure and dependable. The commitment to quality benchmarking, where each strip is scrutinized for imperfections, reinforces consumer confidence across supply chains.
Organizations leveraging cold strip mill technology often share their experiences to bolster trust among stakeholders and clients. Their testimonials highlight improved productivity and product reliability, reflecting real-world applications that showcase substantial returns on investment. These enterprises often certify their processes through internationally recognized quality management systems, such as ISO certifications, which further substantiate the trustworthiness of their production lines.
End-user experiences confirm the superior performance attributes of products made from cold strip mills. Automobile manufacturers, for example, benefit from steel strips' uniformity and strength, crucial for safety and efficiency. Similarly, appliance manufacturers tout the durability and corrosion resistance of cold-milled steel, enhancing the longevity and market competitiveness of their products.
In conclusion, understanding cold strip mills goes beyond the surface-level mechanics to appreciating the amalgamation of experience, expertise, authority, and trust embedded within their operations. As the industry progresses, innovations will continue to drive the capabilities and applications of cold strip mills, solidifying their indispensable role in global manufacturing arenas. Whether through adopting new technologies or optimizing existing processes, the future of cold strip mills is poised to redefine what's possible in steel production, maintaining their pivotal position in the industrial sector.