Narrow strip mills play a crucial role in the production of narrow width steel strips, which are essential in numerous industrial applications due to their strength, versatility, and durability. Navigating the world of narrow strip mills requires not only a comprehensive understanding of the machinery involved but also a keen insight into the industry's evolving trends and technological advancements. This article delves into the unique nuances of narrow strip mills, combining industry expertise with authoritative insights to ensure a trustworthy and enriching read.
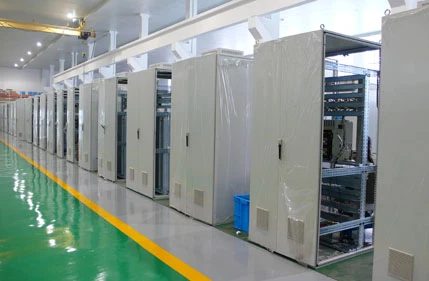
The manufacturing of narrow width strips in a strip mill involves a precise and engineered process that transforms raw steel materials into strips of specific dimensions. The machinery utilized in narrow strip mills is adept at handling slender strip dimensions, often less than 600 mm in width, while maintaining high production quality and efficiency. The most advanced narrow strip mills in the market today incorporate automation technologies such as PLCs (Programmable Logic Controllers) to fine-tune the operation processes. This level of automation ensures precision in the cutting, rolling, and finishing of the strips, which is vital to meeting the high standards set by various industries.
Expert operators in narrow strip mills are crucial for overseeing the complex workflows and ensuring that each phase of the production process adheres to stringent quality controls. Hands-on experience is paramount; seasoned operators can quickly adjust parameters to address issues like temperature variances or material inconsistencies, thereby minimizing downtime and wastage.
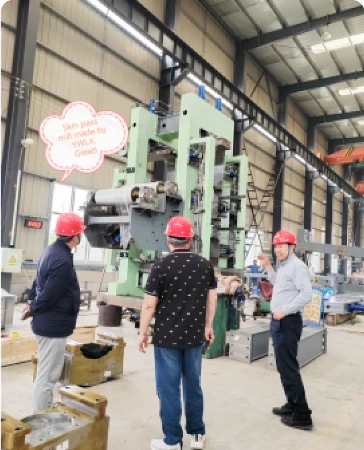
Material choice is another area where experience and expertise come into play. Steel used in narrow strip mills is often treated with specialized coatings or composite materials to enhance properties such as corrosion resistance, tensile strength, and surface finish. Selecting the optimal material composition is vital for meeting the specific needs of sectors ranging from automotive to construction. Engineers and material scientists work collaboratively to develop innovative solutions that help narrow strip products keep pace with demanding industry requirements.
The environmental impact of narrow strip milling cannot be overlooked, making sustainable practices increasingly important. New advancements in technology allow strip mills to minimize energy consumption and reduce waste through efficient recycling processes. Experts in the field are continually researching methods to enhance energy efficiency and waste management, ensuring that narrow strip mills not only meet their production goals but also adhere to environmental standards.
Narrow strip mill
Establishing credibility with stakeholders is crucial, and this comes through transparency and adherence to international quality certifications. Trustworthiness in narrow strip milling is gained by meeting and often exceeding ISO standards, thereby assuring clients and partners that the products manufactured are of the highest quality possible. Manufacturers who invest in certifications and ongoing training inherently boost their reputability within the industry.
Emerging trends indicate a growing demand for customization in narrow strip products, where clients seek specific dimensions and coatings tailored to niche applications. This burgeoning need for personalized solutions drives innovation within strip mills, pushing the boundaries of what traditional machinery can accomplish. Leaders in the industry are those who can seamlessly integrate customization into their production lines, offering quick and precise adjustments without compromising on quality or lead times.
The journey through narrow strip milling is enriched by the contributions of seasoned technologists and engineers whose deep-seated knowledge propels the industry forward. Real-world experience melded with a strong grasp of theoretical principles ensures that these professionals can devise novel solutions to production challenges. Their authoritative insights assist in maintaining the reliability of processes and the consistency of output, fostering trust and reliance among users of narrow strip mill products.
In conclusion, the intricate world of narrow strip mills is characterized by its demand for technical acumen, ongoing innovation, and a steadfast commitment to quality and sustainability. By understanding the intersection of machinery, materials, and market demands, one can navigate the complexities of narrow strip mills with assured expertise. Thus, staying ahead in the industry hinges on an unwavering dedication to quality, environmental conscientiousness, and the provision of cutting-edge, customized solutions that meet the evolving needs of diverse sectors.