Cold rolling of strip metal is a fundamental process in the manufacturing of high-quality metal products. This technique involves the rolling of metal strips at room temperature to achieve a denser material with improved surface finish and dimensional accuracy. With years of expertise in metal processing, I present the nuances of cold rolling that professionals in the industry recognize as crucial to achieving superior product quality.
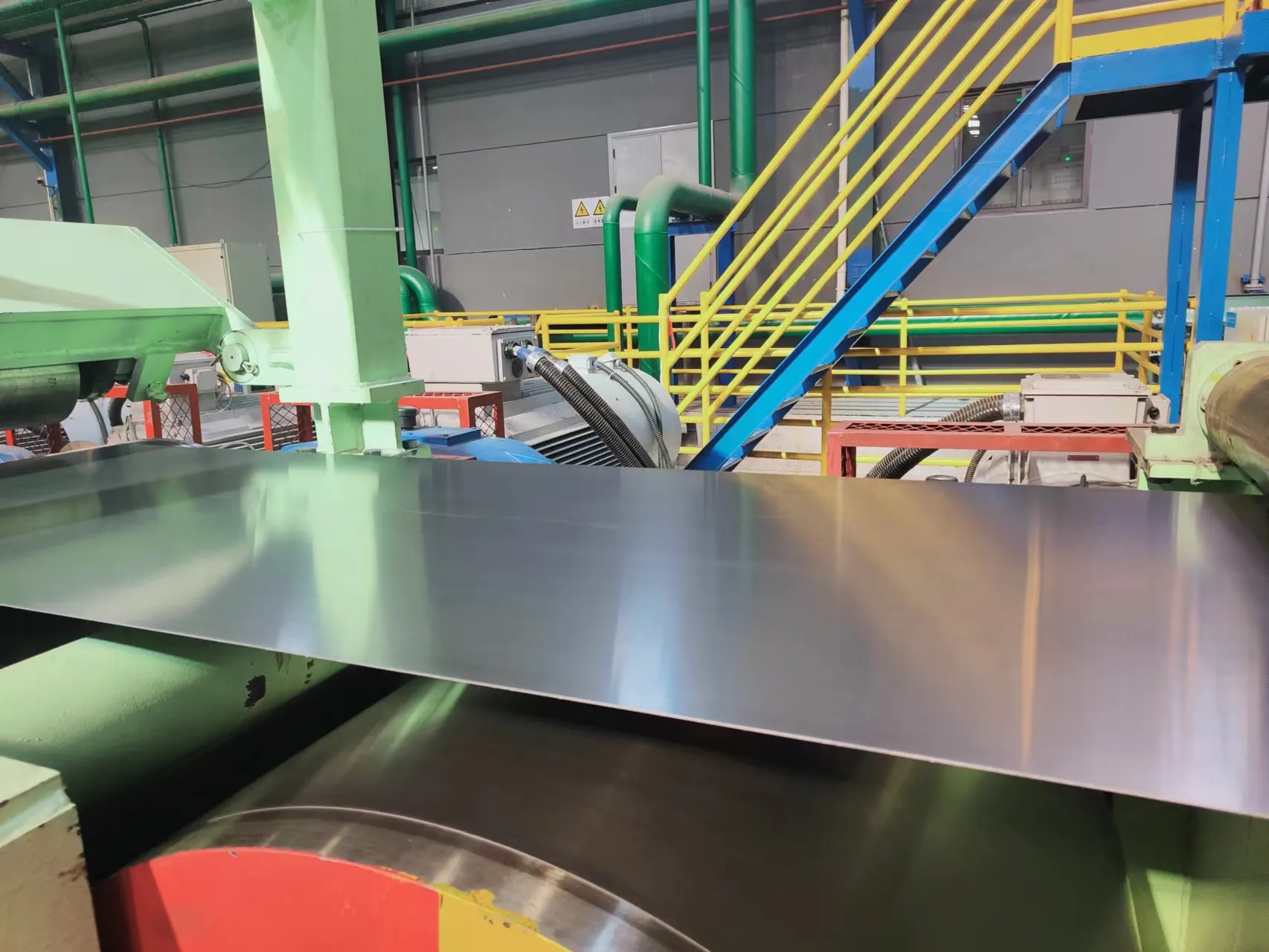
Cold rolling enhances the mechanical properties of the metal, including its yield and tensile strength, while also providing an excellent surface finish. This is primarily because the process compresses the grain structure of the metal, leading to enhancements in its durability and reliability. Manufacturers highly value these attributes in applications that require precision, such as automotive panels and appliance housings.
In my extensive experience, the quality of cold-rolled strip is greatly influenced by the initial material quality and the specific procedures employed during the rolling process. It's essential for manufacturers to begin with premium raw materials. This approach guarantees that any imperfections such as inclusions or impurities are minimized, ensuring that the final product meets rigorous specifications.
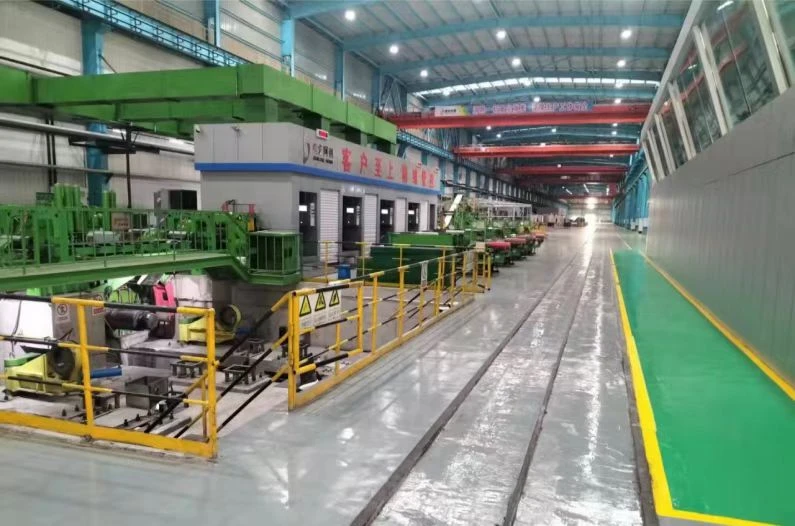
When delving into the technical aspects, cold rolling requires precision in the setup of rolling mills. These mills must be meticulously aligned and maintained to prevent any deviations that might affect the strip's thickness or shape. Automation solutions and modern control systems have become invaluable, streamlining operations and enhancing accuracy, which meets the high demands of today's market.
The expertise required in cold rolling extends beyond the mechanics of the process; it also encompasses an understanding of the material's behavior under stress. The cold rolling process significantly work-hardens the material, increasing its strength and sometimes resulting in residual stresses. Professionals must adeptly manage these factors, frequently employing annealing steps to alleviate stress and refine the grain structure before further rolling or forming operations.
cold rolling strip
Credibility in the cold rolling process is demonstrated not only through adherence to international standards but also through the establishment of quality assurance measures. Regular inspection and testing regimes are imperative to ascertain that the final strip meets the desired criteria in terms of thickness, hardness, and surface finish. Employing non-destructive testing methods such as ultrasonic testing and eddy current inspections can further validate the integrity of the strip without causing any damage.
To establish authority within the field, it’s crucial for industry participants to maintain a robust knowledge base regarding technological advancements and emerging trends. For instance, the advent of smart manufacturing and the integration of AI algorithms into process control have revolutionized efficiency in cold rolling operations. Staying abreast of such innovations ensures sustained competitiveness and the ability to provide customers with cutting-edge solutions.
Lastly, fostering trustworthiness in business practices is critical. Transparent communication with customers, including providing comprehensive technical support and guidance, can strengthen relationships and cement an organization’s reputation in the market. By continually delivering products that exceed expectations, companies can differentiate themselves in the competitive landscape of metal manufacturing.
In conclusion, cold rolling of strip metals is a sophisticated process that requires a blend of expertise, precision, and innovation. As experts in the field continue to push boundaries, the cold-rolled products manufactured today are emblematic of both technological progress and a deep-seated commitment to quality.