Rolling mills are indispensable tools in metalworking, transforming raw metal into various shapes and sizes through deformation. Understanding the different types of rolling mills can provide significant insights, enhancing decision-making in industrial applications. Each type of mill has distinct functionalities, making it imperative to understand their specific roles in metal production processes.
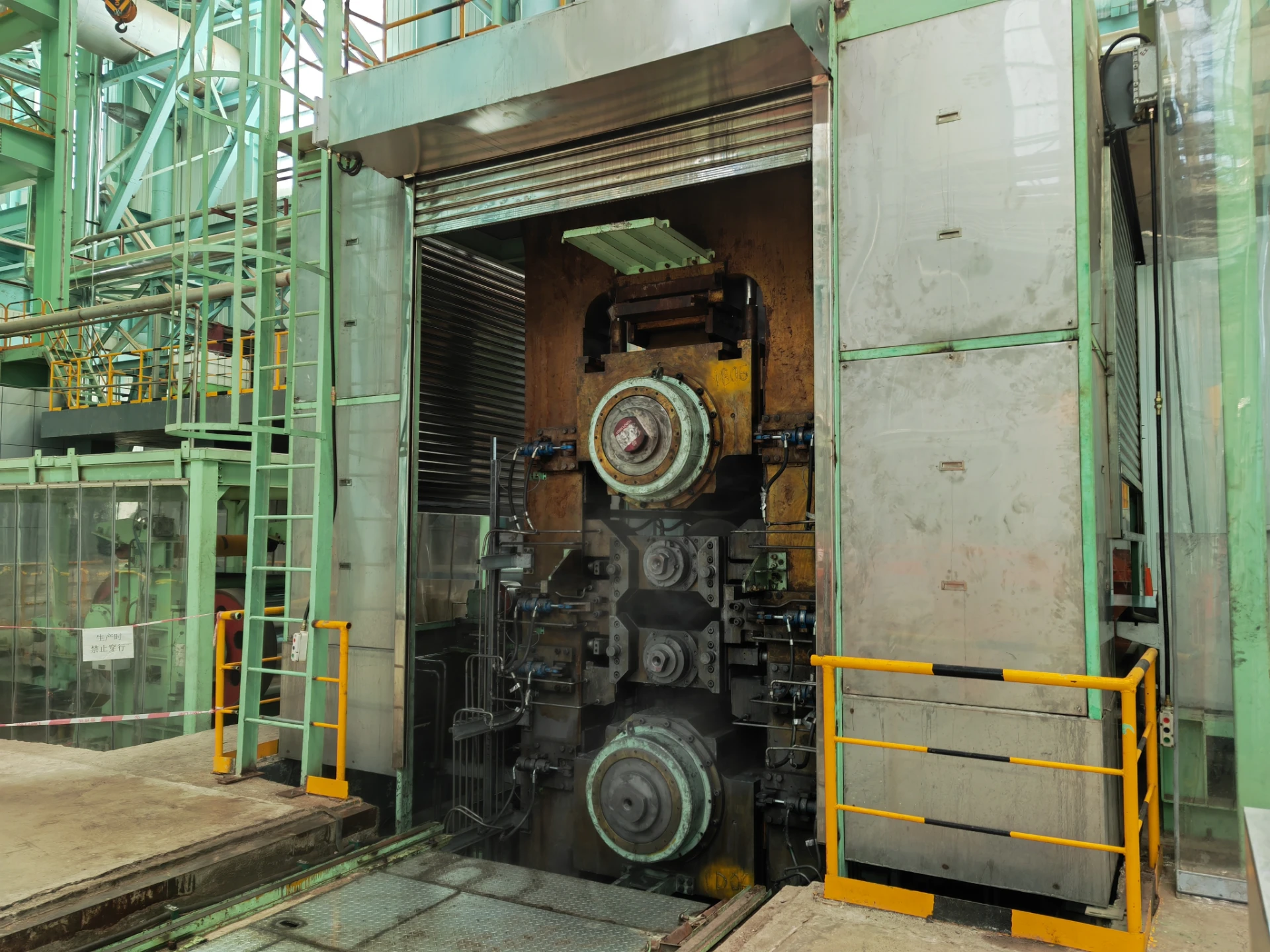
The two-high rolling mill is the simplest form of milling equipment and consists of two horizontally opposed rolls. Its straightforward design allows for easy maintenance and operation, making it ideal for small batch production or laboratory settings. However, this type of mill is limited by its capacity and lack of precision, suitable mostly for rough rolling operations where accuracy is not the primary concern.
The three-high rolling mill, an innovative update on the two-high configuration, incorporates a third horizontal roll. This design allows for continuous rolling, as the material can be passed back and forth between the top and bottom rolls without the need to manually return it to the starting point. This results in increased efficiency and reduced operator fatigue, making the three-high mill a popular choice in larger-scale production environments.
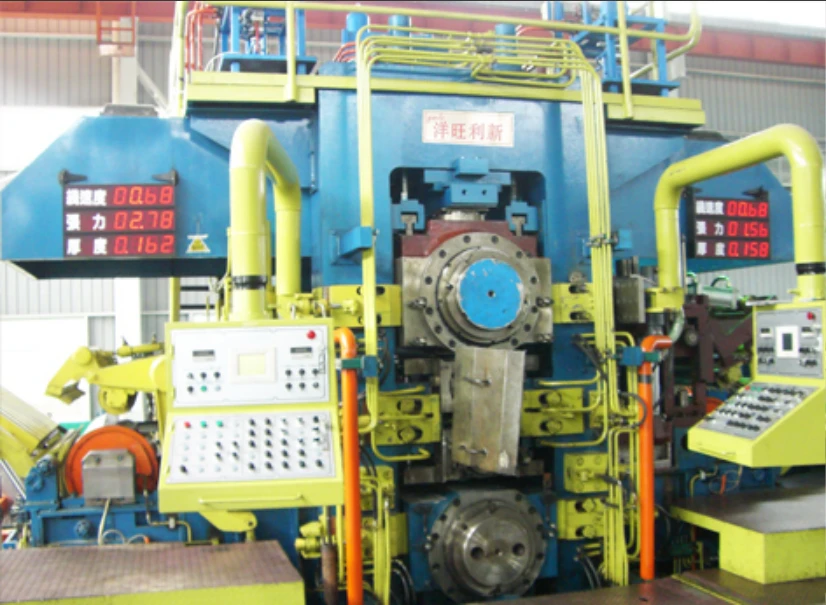
Four-high rolling mills are a notable advancement, engineered to exert greater pressure during the rolling process. They incorporate smaller working rolls that manage the material transformation while larger backup rolls support them to prevent deflection. This type of mill is instrumental in creating thinner and more precise sheet metals, making it a staple in manufacturing industries where tight tolerances and high precision are required.
Cluster rolling mills, a natural extension of the four-high design, include multiple smaller rolls. This configuration ensures low roll deflection, further refining the thickness and surface quality of the metal. These mills are particularly valuable in producing metal foils and ultra-thin materials, sectors where dimensional accuracy and surface finish are non-negotiable.
Universal rolling mills possess the capability to roll metal in multiple directions, addressing the limits of previous designs that primarily focused on longitudinal deformation. With vertical rolls on both sides, it provides the flexibility to control both width and depth simultaneously, which is crucial for producing H-sections, rails, and I-beams. This makes universal mills essential in construction and infrastructure projects where structural integrity and versatility are imperative.
types of rental tents
Planetary rolling mills, equipped with a set of small rolls arranged in a cluster around a large backing roll, offer swift and efficient reduction of incoming material size. They are best suited for hot rolling processes, accommodating significant reductions in thickness in a single pass. This type of rolling mill is valuable in industries focused on high-volume, low-cost production, where efficiency and throughput are prioritized.
Each type of rolling mill plays a pivotal role in today’s metalworking landscape, influencing the quality, efficiency, and specialty of production processes. By selecting the appropriate type of mill, manufacturers can optimize production, reduce waste, and enhance product quality. Understanding these nuances allows companies to better align with market demands and maintain competitive edge in an ever-evolving industry.
Deciphering the ideal match between material and mill type requires keen expertise and experience. Various factors, such as metal type, desired product dimensions, production volume, and surface finish requirements, all dictate the choice of milling machine. Collaboration with seasoned engineers and industry experts can strongly influence the optimization process, ensuring that the production line operates at maximum efficiency with minimal downtime and resource expenditure.
To reinforce authoritative knowledge, it is crucial to remain updated with technological advancements and adaptive strategies in rolling mill technologies. Attending industry conferences, engaging in professional networks, and investing in continuous education are all strategic moves to stay ahead in the metal manufacturing sector.
By understanding the fundamental distinctions and applications of the various types of rolling mills, stakeholders can make informed decisions that enhance operational efficiency, ensure product quality, and fulfill market requirements. Emphasizing expertise, experience, authority, and trust, industry professionals can leverage these insights to drive innovation and success in metalworking operations.