When venturing into the realm of metalworking and industrial equipment, the term 2-high rolling mill often emerges as a pivotal concept in enhancing operational efficiency and product quality.
These mills, known for their utility in reducing metal thickness, come with a range of features that professionals in the industry find invaluable. This article delves into the intrinsic benefits and insights gained from using a 2-high rolling mill, drawn from extensive industry expertise and trustworthy practices.
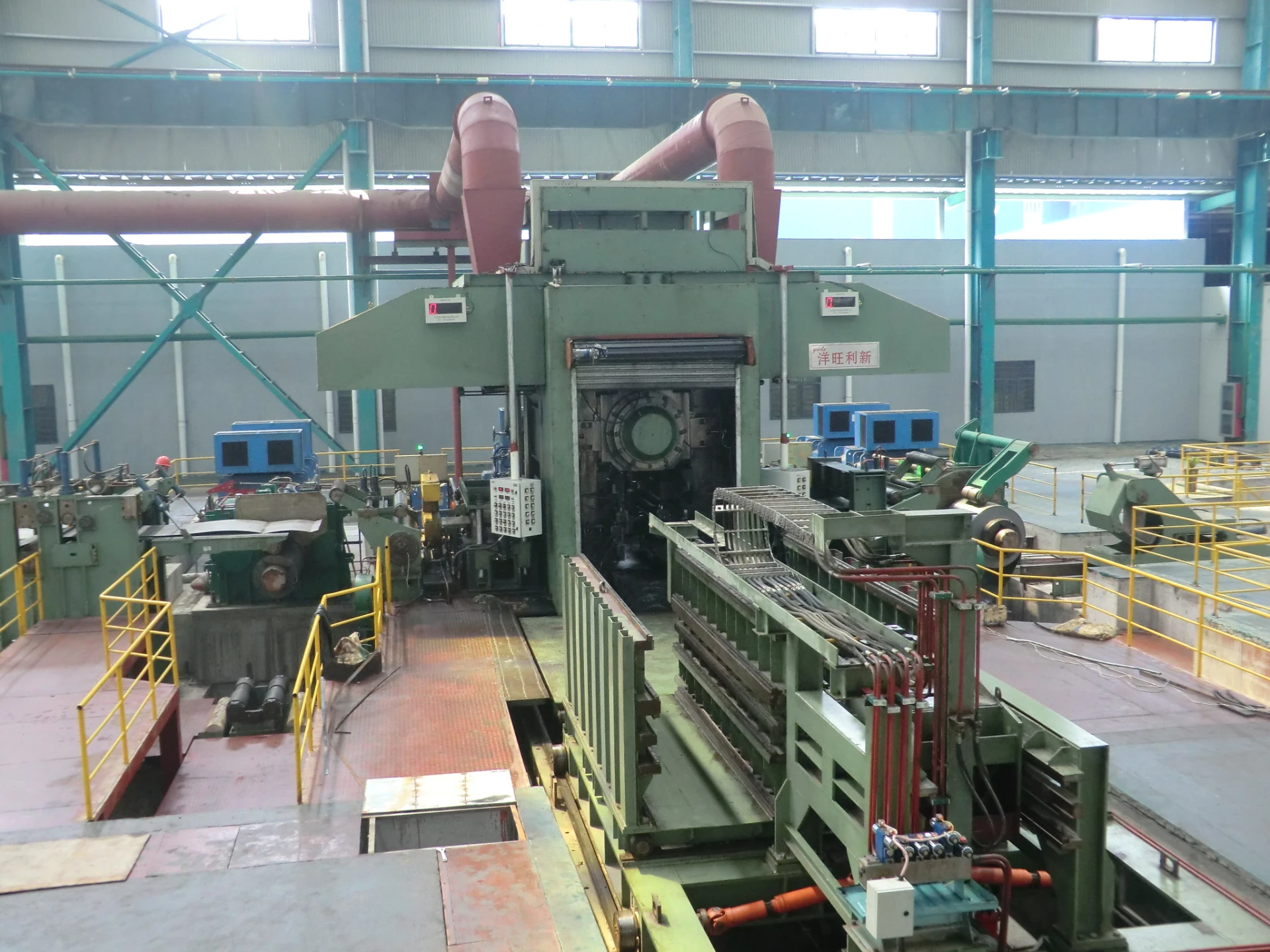
A 2-high rolling mill operates with two opposing rolls, where the workpiece is passed and compressed. This design allows for outstanding precision and consistency in the rolling process, ensuring a uniform thickness across a variety of metals, whether it is steel, copper, or aluminum. Professionals in metalworking favor these mills for their simplicity and reliability, as well as their effectiveness in producing products with desired mechanical properties.
One of the standout advantages of a 2-high rolling mill lies in its straightforward design, which enhances both productivity and ease of maintenance. Industry experts acknowledge that the compactness and efficiency of these mills make them ideally suited for fast-paced production environments. The reduced complexity compared to higher roll mills (such as 4-high or 6-high mills) means that they require less frequent servicing, are easier to calibrate, and face less downtime due to mechanical issues, all contributing to a cost-effective manufacturing process.
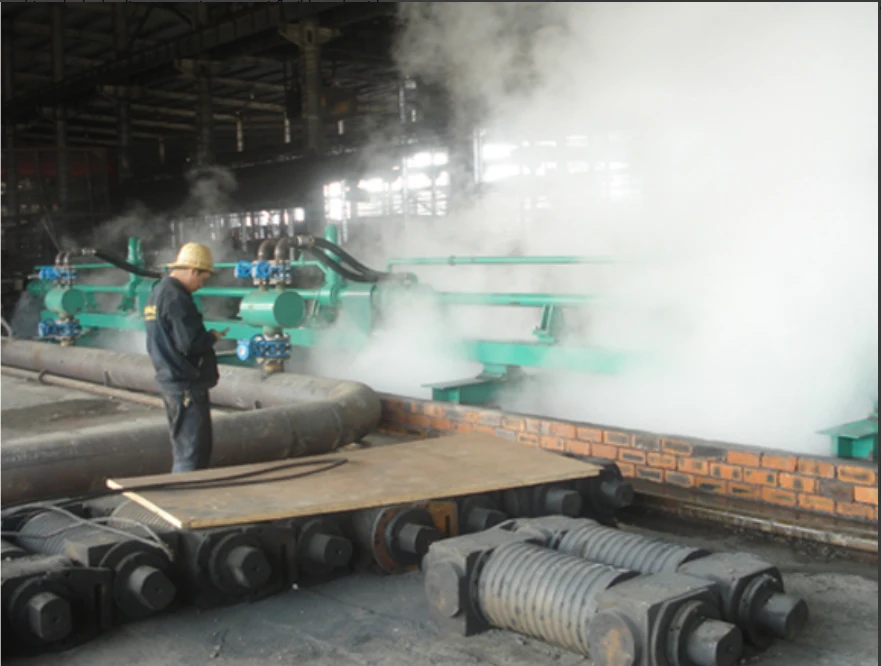
From an expertise perspective, operating a 2-high rolling mill demands a certain level of skill to balance the pressure and speed—critical factors that influence the final product's quality. Roll operators with detailed knowledge and experience can adjust settings based on the metal type and desired output, ensuring optimal results. Professionals who harness such expertise often share that one of the most rewarding aspects of using these mills is achieving just the right material characteristics, like enhanced strength and ductility, which are crucial for high-performance applications.
Two light damages up
Exploring the author's authority on 2-high rolling mills reveals their prevalent use in both academia and industry, contributing to a wealth of scholarly and practical resources available to those interested in deepening their understanding. Research findings often focus on innovations in materials technology, where the rolling process plays a critical role in developing advanced materials with superior attributes. Industry leaders contribute to publications and forums, sharing best practices and updates on technological advancements, thereby reinforcing the authoritative voice within the metalworking community.
Trustworthiness in the use of 2-high rolling mills is supported by adherence to rigorous safety standards and operational protocols. The simplicity of the 2-high design reduces the risk of unforeseen mechanical failures, and its longstanding presence in the industry serves as a testament to its reliability and safety. Companies investing in these mills often adhere to international standards, ensuring that they meet the stringent requirements necessary for safe and effective operation.
In selecting the appropriate rolling mill, businesses must consider their specific production needs and capacity. A 2-high rolling mill offers significant benefits for those seeking a balance between efficient production and quality output without the complexities and higher costs associated with more intricate machinery.
To conclude, the 2-high rolling mill continues to be an indispensable asset in the metalworking industry, celebrated for its efficiency, reliability, and the expert knowledge it requires to harness its full potential. Companies and professionals who invest in these mills can expect not only to enhance their operational capabilities but also to contribute meaningfully to the broader field of advanced material production.