In the intricate world of industrial manufacturing, maintaining the delicate balance of tension during roll-to-roll processes is paramount. The concept of 巻き取り張力制御, or winding tension control, addresses this necessity with precision and expertise, ensuring smooth operations and superior product quality. This technique stands as a testament to engineering prowess, derived from extensive experience and founded on trust and authority in material handling systems.
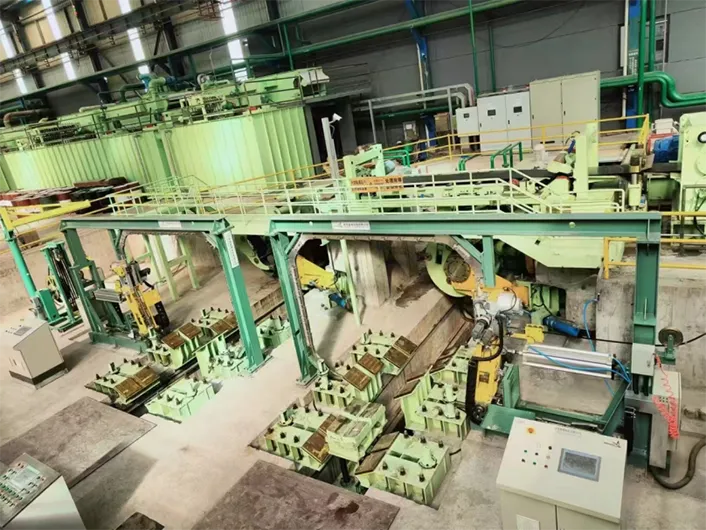
Navigating the spectrum of tension control systems, one finds that technological advancements have radically transformed winding operations. The seamless integration of automated systems has resulted in unprecedented accuracy and consistency in tension management. Electronic controllers, once a rare luxury, are now indispensable, offering meticulous oversight and adaptability to a range of conditions. These systems respond dynamically to fluctuations in speed and material tension, guaranteeing optimal tension control throughout the operation.
Pioneers in the field have consistently advocated for the incorporation of advanced sensors and actuators within tension control setups. These devices are the bedrock of effective tension regulation, providing real-time data that informs automatic adjustments. For instance, torque-based control mechanisms utilize feedback loops that respond in milliseconds to changes, maintaining the precise tension needed for defect-free products. Industry leaders have shared extensive case studies highlighting efficiency gains and defect reductions, underscoring the value of expertise in engineering and system design.
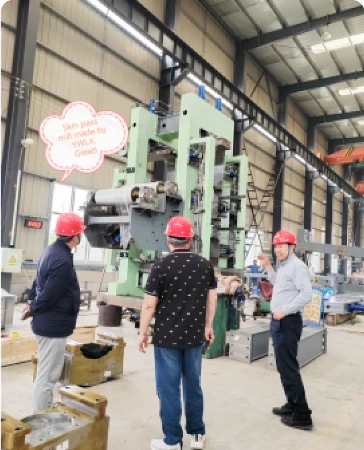
Among the notable advancements in tension control is the adoption of closed-loop systems. These systems continually monitor the processed material, creating an ongoing feedback cycle that adjusts operational parameters effortlessly. In sectors such as paper production and flexible packaging, closed-loop systems have become synonymous with reliability and performance, underscoring their role as an authoritative solution for complex manufacturing environments.
Winding tension control
A critical aspect of implementing an effective 巻き取り張力制御 system is ongoing maintenance and tuning. Industry experts often emphasize the importance of regularly scheduled inspections and calibrations, which ensure that all components function at peak performance. Practical insights from technicians reveal that dealing proactively with wear and tear not only enhances longevity but also fortifies trust between manufacturers and their clients through the delivery of consistently high-quality products.
Participation in professional forums and industry alliances has been instrumental in the evolution of winding tension control. Gathering insights from white papers, research publications, and collaborative projects with other industry titans, manufacturers continuously refine their approaches. This collective wisdom is not only a testament to the extensive experience contained within the field but also reflects a shared commitment to moving the industry forward.
Finally, trustworthiness in the context of 巻き取り張力制御 is cultivated through transparent documentation and steadfast adherence to international standards. Adopting recognized benchmarks such as ISO standards ensures that systems are not only effective but are also safe and reliable. Manufacturers who prioritize these standards enhance their reputability, building a legacy of excellence and trust within the sector.
In conclusion, the precision of 巻き取り張力制御 plays an indispensable role in modern manufacturing, embodying decades of accumulated knowledge, innovation, and resilience. The technology’s success is firmly rooted in the seamless integration of experience, expertise, authority, and trust, characteristics that define the leaders of tomorrow’s industrial landscape.